Use this panel to control the output of spatially averaged solutions and spray data from the simulation model. Check the Spatially Averaged and Spray box to activate the options. The options are the same as those described for Spatially Resolved data in the previous section, except for the user-defined frequency. The spatially averaged solutions are written as comma-separated-value (.csv) files. Since the spatially averaged data takes up much less space in the solution file, it is not necessary to limit the frequency to the extent that is necessary for the spatially resolved data.
Note: The parameters reported in dynamic.csv, flame.csv, flow_into_cylinder.csv, flow_into_primary_region.csv, mass/molefraction.csv, particle.csv, particle_size_distribution.csv, speciesmass.csv, thermo.csv and two_phase.csv are only for the in-cylinder region (or a primary region, for non-engine cases). If a cylinder/primary region has Sub-Chamber-typed region(s) connected to it, the spatial averaging considers the Sub-Chamber region(s) as part of the cylinder/primary region.
In the Spatially Averaged Species sub-panel, select which gas species data will be saved in the output files. Move species from the Choices list to the Selection list to include them as a Spatially Averaged Species. You can type into the Filter box to limit the species presented in the Choices list. Three .csv files dedicated to species data output. Speciesmass.csv, massfraction.csv, and molefraction.csv include the data of species mass, mass fraction and mole fraction, respectively. If the simulation type is Eulerian two-phase flow (Gas-Phase and Eulerian Two-Phase Flow Simulations), all the liquid species' data will be saved in these solution files.
As for the spatially averaged solution variables and spray variables, Table 3.6: Spatially averaged variables that are always output to the .csv files summarizes the variables’ names, their output files, and their descriptions.
Table 3.6: Spatially averaged variables that are always output to the .csv files
Output File[a] | ||
---|---|---|
The x coordinate of the center of mass in the cylinder.
| ||
The y coordinate of the center of mass in the cylinder. | ||
The z coordinate of the center of mass in the cylinder. | ||
Total angular momentum of the in-cylinder flow in the x direction, relative to the instantaneous mass center in the cylinder. where | ||
Similar to Total angular momentum-x, but for the angular momentum in the y direction. | ||
Similar to Total angular momentum-x, but for the angular momentum in the z direction. | ||
Root mean square of the x-, y-, z-angular momentum. Unit: g-cm 2 /s. | ||
The ratio of the angular velocity of the in-cylinder
flow about the x axis to engine rotating velocity. | ||
Similar to Tumble ratio-x, but for the angular velocity
in the y direction. | ||
Similar to Tumble ratio-x, but for the
angular velocity in the z direction. Note that this swirl ratio definition assumes that the axis of the cylinder aligns with the z-axis. | ||
Total kinetic energy of the in-cylinder gas. Unit: g-cm 2 /s 2. | ||
Mass-averaged dissipation rate of turbulent kinetic energy. Unit: cm 2 /s 3. | ||
Mass averaged turbulent velocity, defined as
| ||
Mass-averaged turbulent contribution to the effective
kinematic viscosity. The value in each cell is calculated as | ||
Mass-averaged effective (laminar + turbulent) thermal conductivity of the gas phase. Unit: erg/cm-s-K. | ||
Pure chemical heat release rate in the cylinder or in region 1, calculated directly based on chemical heat release in the cells. Unit: J/deg for engine cases, J/s for non-engine cases. | ||
Accumulated chemical heat release rate in the cylinder or in region 1. Unit: J. | ||
Rate of wall heat transfer through the wall of cylinder or region 1. The heat transfer includes both convective and radiative heat transfer, if applicable. Unit: J/deg for engine cases, J/s for non-engine cases. | ||
Accumulated wall heat transfer loss through the wall of cylinder or region 1. The heat loss includes both convective and radiative heat loss, if applicable. Unit: J. | ||
The difference between chemical heat release rate and wall heat transfer loss rate. Unit: J/deg for engine cases, J/s for non-engine cases. [b] | ||
This heat release rate is based on the in-cylinder averaged pressure and volume time/crank angle profiles, assuming a constant gamma (1.35), and is calculated as follows, where dt may also be dCA in engine cases ( t is time, CA is crank angle):
Numerically, the gradient terms at time n are calculated using values at time n and n -1, for example, . Unit: J/deg for engine cases and J/s for non-engine cases. | ||
Accumulated apparent heat release amount derived from the in-cylinder pressure-volume curve, assuming a constant gamma (1.35). Unit: J. | ||
T |
This heat release rate is based on the in-cylinder averaged pressure and
volume time/crank angle profiles, using variable gamma values, where gamma is the specific
heat ratio (
...where | |
Accumulated apparent heat release from PV-VarGamma |
T |
Accumulated apparent heat release amount derived from the in-cylinder pressure-volume curve, using variable gamma values. Unit: J. |
Heat capacity of gas-phase mixture at constant volume. Unit: J/Kg-K. | ||
Heat capacity of gas-phase mixture at constant pressure. Unit: J/Kg-K. | ||
Total mass of the gas in a primary region (for non-engine cases). Unit: g. | ||
Total volume of the gas in a primary region (for non-engine cases). Unit: cm3. | ||
Total volume of the gas in the whole computational domain. Unit: cm 3. | ||
In-cylinder (or Region) averaged equivalence ratio |
T | Equivalence ratio calculated using the averaged species mass fractions in a cylinder or primary region, defined as the ratio of oxygen needed to convert carbon and hydrogen to CO2 and H2O to the oxygen available in the mixture. Where [C], [H], and [O] are the sum concentrations of carbon, hydrogen, and oxygen atoms in the mixture, respectively: This definition of equivalence ratio is essentially an element ratio that considers all the species in the mixture. It measures the equivalence ratio of a mixture in its unburned state. Using this definition, a mixture’s equivalence ratio remains invariant as it changes from unburned to completely combusted in the combustion process. |
In-cylinder (or Region) averaged residual fraction |
T |
The averaged residual fraction is the mass fraction of the residual mixture in a cylinder or primary region. The residual fraction is estimated by using the equivalence ratio calculated in the row above and the spatially averaged mixture composition as inputs. It also assumes that the fuel is completely converted to combustion product. Specifically, the residual gas includes CO2, H2O as well as N2 needed to generate CO2 and H2O through complete combustion. For lean mixtures, the residual also includes excess O2, subject to its availability in the mixture. |
In-cylinder (or Region) averaged progress equivalence ratio |
T | The progress equivalence ratio is calculated as: where [C], [H], and [O] are the sum concentrations of carbon, hydrogen, and oxygen atoms in species excluding CO2, H2O, and O2, and [O] from O2 is the concentration of oxygen atoms from O2. Using this variation definition, the φ value varies as a combustible mixture changes from its unburned state to completely burned state in the combustion process. |
In-cylinder (or Region) averaged progress residual fraction |
T |
The "progress" residual fraction is calculated using the same assumption as the regular residual fraction described above, but it uses the "progress" equivalence ratio when estimating the N2 needed to generate the combustion product and the excess O2 for lean mixtures. |
Total mass of CO normalized by total fuel mass in the cylinder (for engine cases) or region 1 (for non-engine cases). Unit: g/kg-fuel. | ||
Total mass of NO normalized by total fuel mass in the cylinder (for engine cases) or region 1 (for non-engine cases). Unit: g/kg fuel. | ||
Total mass of NO2 normalized by total fuel mass in the cylinder (for engine cases) or region 1 (for non-engine cases). Unit: g/kg fuel. | ||
Emission index (EI) of NO x species. In this NOx definition, NO is first converted to NO 2 and then the mass of the converted NO 2 is summed up with the actual NO 2. This parameter is normalized by the total mass of fuel. Unit: g/kg-fuel. | ||
Total mass of soot species normalized by total fuel mass in the cylinder (for engine cases) or region 1 (for non-engine cases). Unit: g/kg fuel. | ||
Total mass of unburned hydrocarbon (UHC) species normalized by total fuel mass in the cylinder (for engine cases) or region 1 (for non-engine cases). The hydrocarbon species include species that contain both C and H atoms, and no other atoms. Unit: g/kg-fuel. | ||
ppm of unburned hydrocarbon converted to C1 level. Unit: ppm. | ||
The volatile organic compound species include species that contain both C and H atoms, and the species may contain other atoms, such as oxygen (O) or nitrogen (N). | ||
ppm of volatile organic compound converted to C1 level. Unit: ppm. | ||
Average molecular weight of the gas mixture in the cylinder (for engine cases) or region 1 (for non-engine cases). | ||
T |
In-cylinder averaged compressibility factor, calculated by | |
Number of computational cells in which detailed chemistry is being solved. | ||
Number of clusters created by the Dynamic Cell Clustering method. | ||
Averaged number of active species obtained from the Dynamic Adaptive Chemistry method. | ||
Minimum number of active species obtained from the Dynamic Adaptive Chemistry method among all the cells. | ||
Maximum number of active species obtained from the Dynamic Adaptive Chemistry method among all the cells. | ||
Averaged number of active reactions obtained from the Dynamic Adaptive Chemistry method. | ||
Minimum number of active reactions obtained from the Dynamic Adaptive Chemistry method among all the cells. | ||
Maximum number of active reactions obtained from the Dynamic Adaptive Chemistry method among all the cells. | ||
Number of convergence failures |
C |
Number of convergence failures encountered when solving chemistry in CFD cells or DCC clusters. |
Number of transported species |
C |
Number of species being solved in flow transport. When chemistry is inactive and species lumping has been applied, only a subset of species participates in flow transport. |
Density of the burnt gas mixture when the flame propagates. Unit: g/cm3. | ||
Density of the unburnt gas mixture when the flame propagates. Unit: g/cm3. | ||
Averaged plasma velocity of the particles used to track spark-ignition kernel flames. Unit: cm/s. | ||
Averaged laminar flame speed of all the cells containing the flame front surface. Unit: cm/s. | ||
Averaged turbulent flame speed of all the cells containing the flame front surface. Unit: cm/s. | ||
Averaged flame stretch factor of all the cells containing the flame front surface. The stretch factor is part of the turbulent flame speed correlation and it accounts for the stretching effect of curvature and turbulence on flame propagation speed. Unit: dimensionless. | ||
Chem_heat_release_rate_end_gas |
F |
Chemical heat release rate in the end gas zone. Unit: J/deg for crank-angle-based simulation and J/s for time-based simulation. |
Chem_heat_release_rate_flame_front |
F |
Chemical heat release rate in the end gas zone. Unit: J/deg for crank-angle-based simulation and J/s for time-based simulation. |
Chem_heat_release_rate_post_flame |
F |
Chemical heat release rate in the post flame zone. Unit: J/deg for crank-angle-based simulation and J/s for time-based simulation. |
Accum_chem_heat_release_rate_end_gas |
F |
Accumulated chemical heat release in the end gas zone. Unit: J. |
Accum_chem_heat_release_flame_front |
F |
Accumulated chemical heat release in the flame front zone. Unit: J. |
Accum_chem_heat_release_post_flame |
F |
Accumulated chemical heat release in the post flame zone. Unit: J. |
Accumulated injected fuel mass at specific time or crank angle from injector N. Unit: g. | ||
Accumulated injected fuel mass at specific time or crank angle from all injectors. Unit: g. | ||
Total mass of off-wall liquid droplets at specific time or crank angle. Unit: g. | ||
Total film area |
S |
Total wall boundary area covered by wall film for the whole domain. Unit: cm2. |
Total film mass |
S |
Total mass of wall film in the entire domain. Unit: g. |
Averaged wall film thickness for the whole domain, calculated as the total liquid film volume divided by the total wall film area. Unit: cm. | ||
Film mass from (injector name, nozzle name) |
S |
Mass of wall film originated from each individual nozzle hole. Unit: g. |
Total impinged mass |
S | Total mass of injected liquid parcels that have ever impinged on wall boundaries. It is an accumulated quantity. The impinged liquid parcels could have been converted to wall film or remain as airborne droplets after being rebounded from the wall. Unit: g. |
Impinged mass from (injector name, nozzle name) |
S | Accumulated impinged mass of liquid parcels from a specific nozzle hole. Unit: g. |
Total mass of fuel vapor in the entire computational domain at specific time or crank angle. Unit: g. | ||
Averaged Sauter Mean Diameter of all the airborne spray droplets in the computational domain. Airborne refers to droplets that are traveling in the gas phase and are not part of the wall film. Unit: micron. | ||
Maximum Weber number of all spray droplets in the computational domain. | ||
For the calculation, all spray parcels are projected onto the axis of a nozzle and then the mass of these liquid parcels is accumulated starting at nozzle exit. The liquid penetration length is defined as the distance between the nozzle exit and the location where accumulated liquid mass reaches 95% of the total liquid mass. Unit: mm. | ||
For the calculation, all computational cells containing fuel vapor are projected onto the axis of a nozzle and then the mass of the fuel vapor in these cells is accumulated starting at nozzle exit. The vapor penetration length is defined as the distance between the nozzle exit and the location where accumulated fuel vapor mass reaches 99.9% of the total liquid mass. Unit: mm. | ||
Output for the nozzle(s) of solid cone injector(s). Breakup length is the distance from the nozzle exit within which a liquid core is assumed to exist. Beyond the breakup length, the Rayleigh-Taylor model is applied, and the liquid core breaks up into spray droplets. See Figure 6.2: KH/RT breakup model for solid-cone sprays and Equation 6–35 of the Ansys Forte Theory Manual for more details. Unit: mm. | ||
Output for the nozzle(s) of solid cone injector(s). Ansys Forte uses the concept of "blob" to simulate the liquid phase injected out of the nozzle. A blob is similar to a droplet in the mathematical sense that they are both discrete, while blobs injected continuously from the nozzle simulate the liquid core within the breakup length. If the internal flows are not cavitating near the nozzle exit, blob diameter is the same as the nozzle diameter. If the internal flows are cavitating, blob diameter is smaller than the nozzle diameter. See Effective Injection Velocity and Effective Flow Exit Area of the Ansys Forte Theory Manual for more details. Blob diameter is denoted as "initial diameter" in Nozzle Flow Model in the Ansys Forte Theory Manual. Unit: micron. | ||
Output for the nozzle(s) of solid cone injector(s). Discharge coefficient is calculated as the actual mass flow rate divided by the theoretical mass flow rate. This parameter is specified as input if you select an empirical discharge coefficient. If not, Ansys Forte, uses a nozzle flow model to calculate it. See Discharge coefficient of the Ansys Forte Theory Manual for more details. | ||
Output for the nozzle(s) of solid cone injector(s). Blob injection velocity is the injection speed of the blobs exiting the nozzle. Also known as "effective injection velocity", as discussed in Effective Injection Velocity and Effective Flow Exit Area of the Ansys Forte Theory Manual for more details. Unit: m/s. | ||
Estimated sac volume pressure of (injector name, nozzle name) |
Output for the nozzle(s) of solid cone injector(s). This is an estimated pressure in the sac volume of the injector. It is also known as the "inlet pressure" because it is estimated upstream of the nozzle entrance. It refers to the location at point 1 and is denoted as p1 in Nozzle Flow Model of the Ansys Forte Theory Manual for more details. Unit: MPa. | |
Output for the nozzle(s) of solid cone injector(s). This is the cone angle of liquid phase injection near the nozzle exit. This parameter is specified as input if an empirical cone angle is the selection. If not, Ansys Forte uses a nozzle flow model to calculate it. See Spray Angle of the Ansys Forte Theory Manual for more details. Unit: degree. | ||
Convective heat transfer coefficient averaged over each wall boundary. Unit: W/m 2 -K. | ||
Convective heat transfer flux averaged over each wall boundary. Unit: W/m 2. | ||
Convective heat transfer rate summed over each wall boundary. Unit: W. | ||
Radiative heat flux of (wall name) |
W |
Radiative heat flux on a wall boundary. In the calculation for this output, the amount of radiation heat transfer in a region is shared proportionally by its bounding walls based on wall surface areas. Unit: W/m2. |
Radiative heat trans rate of (wall name) |
W |
Radiative heat transfer rate allocated on a wall boundary. In the calculation for this output, the amount of radiation heat transfer in a region is shared proportionally by its bounding walls based on wall surface areas. Unit: W. |
y+ value averaged over each wall boundary. y+ is a
dimensionless distance used in law-of-the-wall model. At each location along the wall, y+
is defined as where C μ is a turbulence model
constant, k is turbulent kinetic energy, y is
the distance from the first off-wall grid point to the wall, v is the
kinematic viscosity of the local fluid. Unit: dimensionless. | ||
Mass of wall film droplets summed over each wall boundary. Unit: g. | ||
Film area of (wall name) |
W |
Wall boundary area covered by wall film for a specific wall boundary. Unit: cm2. |
Avg film thickness of (wall name) |
W |
Averaged wall film thickness for a specific wall boundary, calculated as the liquid film volume divided by the wall film area on a specific wall boundary. Unit: cm. |
Impinged mass of (wall name) | W | Accumulated mass of injected liquid parcels that have ever impinged on a specific wall boundary. Unit: g. |
Accum Net Mass Flow |
Accumulated net mass flowing across all open boundaries. Unit: g. | |
Accum Mass Flow of All Inlets |
O |
Total accumulated mass flowing across all inlet boundaries into the simulation domain. Unit: g. |
Total accumulated mass flowing across all outlet boundaries out of the simulation domain. Unit: g. | ||
Net Mass Flow Rate |
Instantaneous mass flow rate across all open boundaries. Unit: g/s. | |
Instantaneous mass flow rate across all inlet boundaries. Unit: g/s. | ||
Instantaneous mass flow rate across all outlet boundaries. Unit: g/s. | ||
Instantaneous mass flux across all inlet boundaries. Unit: g/cm2-s. (Flux is defined as flow rate divided by area.) | ||
Instantaneous mass flux across all outlet boundaries. Unit: g/cm2-s. | ||
Accum Net Vol Flow | O |
Accumulated net volume flow across all open boundaries. Unit: cm3. |
Accum Vol Flow of All Inlets | O |
Accumulated net volume flow across all inlet boundaries. Unit: cm3. |
Accum Vol Flow of All Outlets | O |
Total accumulated volume flow across all outlet boundaries. Unit: cm3. |
Net Vol Flow Rate | O |
Instantaneous volumetric flow rate across all open boundaries. Unit: cm3/s. |
Instantaneous volumetric flow rate across all inlet boundaries. Unit: cm3/s. | ||
Instantaneous volumetric flow rate across all outlet boundaries. Unit: cm3/s. | ||
Instantaneous volumetric flux across all inlet boundaries. Unit: cm/s. (Volumetric flux is the same as averaged normal velocity across the boundary.) | ||
Instantaneous volumetric flux across all outlet boundaries. Unit: cm/s. | ||
Accum Mass Flow of (open boundary name) |
O |
Accumulated mass flowing across a specific open boundary. Unit: g. |
Mass Flow Rate of (open boundary name) |
O |
Instantaneous mass flow rate across a specific open boundary. Unit: g/s. |
Mass Flux of (open boundary name) |
O |
Instantaneous mass flux across a specific open boundary. Unit: g/cm2-s. |
Accum Vol Flow of (open boundary name) |
O |
Accumulated volume flow across a specific open boundary. Unit: cm3. |
Vol Flow Rate of (open boundary name) |
O |
Instantaneous volumetric flow rate across a specific open boundary. Unit: cm3/s. |
Vol Flux of (open boundary name) |
O |
Instantaneous volumetric flux across a specific open boundary. Unit: cm/s. |
Mass_flow_rate_from_region_n |
FC |
Mass flow rate from non-cylinder/non-primary region n into the cylinder/primary region due to convective transport. "Cylinder" corresponds to engine cases and "primary" corresponds to non-engine cases. In engine cases, if a cylinder has a sub-chamber region connected to it, the sub-chamber region is considered as part of the cylinder in this calculation. Unit: g/deg for engine cases, g/s for non-engine cases. |
Accum_mass_flow_from_region_n | FC |
Accumulated mass flow from non-cylinder/non-primary region n into the cylinder/primary region due to convective transport. Unit: g. |
Only activated with rotation wall boundary | ||
Torque of (rotation boundary name) | RO | Torque applied by the rotation wall boundary on the fluid with respect to
the rotation axis. Unit: N-m. Calculated as:
Where T is the torque projected on the rotation axis,
S is a surface triangle on the triangulated rotor surface,
|
Power of (rotation boundary name) | RO | Power applied by the rotation wall boundary on the fluid. Calculated as the torque times the angular velocity of the rotation. Unit: W. |
Force-axial of (rotation boundary name) | RO |
Force applied by the rotation wall boundary on the fluid along the axial direction of the rotation. Unit: N. Calculated as:
Where S is a surface triangle on the triangulated rotor surface,
|
Force-radial of (rotation boundary name) | RO | Magnitude of force applied by the rotation wall boundary on the fluid along the radial direction of the rotation. Unit: N. |
Force-x of (rotation boundary name) | RO | The x-component of force applied by the rotation wall boundary on the fluid in Cartesian coordinate. Unit: N. |
Force-y of (rotation boundary name) | RO | The y-component of force applied by the rotation wall boundary on the fluid in Cartesian coordinate. Unit: N. |
Force-z of (rotation boundary name) | RO | The z-component of force applied by the rotation wall boundary on the fluid in Cartesian coordinate. Unit: N. |
Only activated with planetary motion wall boundary | ||
Torque of (planetary motion boundary name) | PL | Torque applied by the planetary-motion wall boundary on the fluid with
respect to the primary axis. Calculated as the cross product of the eccentric radius vector
and the force applied by this wall boundary. Unit: N-m. Calculated as:
Where T is the torque projected on the primary rotation
axis, |
Power of (planetary motion boundary name) | PL | Power applied on the planetary-motion wall boundary on the fluid. Calculated as the torque times the angular velocity of the primary rotation. Unit: W. |
Force-axial of (planetary motion boundary name) | PL |
Force applied by the planetary-motion wall boundary on the fluid along the axial direction of the rotation. Unit: N. Calculated as:
where S is a surface triangle on the triangulated
rotor surface, |
Force-radial of (planetary motion boundary name) | PL | Magnitude of force applied by the planetary-motion wall boundary on the fluid along the radial direction of the rotation. Unit: N. |
Force-x of (planetary motion boundary name) | PL | The x-component of force applied by the planetary-motion wall boundary on the fluid in Cartesian coordinate. Unit: N. |
Force-y of (planetary motion boundary name) | PL | The y-component of force applied by the planetary-motion wall boundary on the fluid in Cartesian coordinate. Unit: N. |
Force-z of (planetary motion boundary name) | PL | The z-component of force applied by the planetary-motion wall boundary on the fluid in Cartesian coordinate. Unit: N. |
Only activated by Eulerian Two-Phase Flow Simulation | ||
Averaged liquid volume fraction |
TPh |
Averaged volume fraction of the liquid phase in Eulerian two-phase fluid mixture, in the cylinder (for engine cases) or region 1 (for non-engine cases). |
Only activated when arc channel tracking (ACT) spark ignition model is used | ||
Energy discharge rate of (spark name) |
SP |
Discharge rate of electrical energy. Unit: W. |
Accum energy discharge of (spark name) |
SP |
Accumulated electrical energy discharge. Unit: J. |
Energy reserve in (spark name) |
SP |
Remaining electrical energy stored in the secondary coil of the spark ignition system for the current spark discharge event. Until J. |
Arc channel length of (spark name) |
SP |
The current length of the spark arc channel, calculated by concatenating all the arc channel particles from the anode end to the cathode end. Unit: mm. |
Current in secondary coil of (spark name) |
SP |
The current in the secondary coil during the energy discharge process. Unit: Ampere. |
Total voltage fall of (spark name) |
SP |
Total voltage fall across the ignition system, including the anode, spark arc channel, and cathode. Unit: Volt. |
Voltage fall across arc of (spark name) |
SP |
Voltage fall across the spark arc channel. Unit: Volt. |
Breakdown voltage of (spark name) |
SP |
Gas breakdown voltage based on Paschen's Law. Unit: Volt. |
Only activated when Fluid-Structure Interaction (FSI) is enabled | ||
Deflection |
FSI |
Maximum deflection of the body. For springs, tracks the implied deflection resulting from the fluid forces even if the threshold for motion is not achieved. Unit: degrees (for torsional spring motion) or cm (for beams and linear springs). |
Applied Deflection |
FSI |
Maximum deflection of the body, takes into account the threshold for motion and represents the actual position of the moving body seen by the simulation. Unit: degrees (for torsional spring motion) or cm (for beams and linear springs). |
Pressure Force |
FSI |
Area integrated pressure force on the body. Unit: Dyne. |
Torque |
FSI |
Torque on the body with respect to the body's end position from area integrated pressure force. Unit: Dyne-cm. |
Neutral Axis Position |
FSID |
Position along the bending beam at the neutral axis, allows plotting the current shape of the beam in the Monitor. Unit: cm. |
Deflection |
FSID |
Deflection along the bending beam as a function of the neutral axis position, allows plotting the current shape of the beam in the Monitor. Unit: cm. |
[a] D: dynamic.csv; T: thermo.csv; H: Whole_domain_parameters.csv; C: chemsolver.csv; F: flame.csv; S: spray.csv; W: wall_boundary_parameters.csv; O: open_boundary_flow.csv; FC: flow_into_cylinder.csv or flow_into_primary_region.csv; RO: rotation _boundary_parameters.csv; PL: planetary_boundary_parameters.csv; SP: spark.csv; TPh: two_phase.csv; FSI: [boundary name]_fsi.csv; FSID: [boundary_name]_displacements.csv
[b] HRR (heat release rate) reported in the HRRfromPV.csv file is
based on the in-cylinder averaged pressure and volume time/crank angle profiles, assuming
a constant gamma, and is calculated as follows, where dt may also be dCA in engine cases
(t is time, CA is crank angle):
Table 3.7: Spatially averaged variables that are output to the .csv files when the Method of Moments soot model is used
Spatially Averaged Statistical Solution for Selected Parameters: If
this box is checked, the mean and standard deviation (SD) of a group of selected parameters will
be reported in thermo_stat.csv. Currently, the selected output parameters
include Pressure
, Temperature
, Equivalence
ratio
, Residual fraction
, Progress equivalence
ratio
, and Progress residual fraction
. Like
thermo.csv, thermo_stat.csv also considers cells in
each in-cylinder region (or primary region). If a cylinder/primary region has Sub-Chamber-typed
region(s) connected to it, the spatial averaging considers the Sub-Chamber region(s) as part of
the cylinder/primary region. The mean and SD are weighted by either cell volume fraction (for
pressure) or cell mass fraction (for all the other parameters). Take equivalence ratio
() as an example, the mass-weighted mean (
) and SD (
) for the
cells in a region are calculated as:
in which the weight is the mass of cell
divided by the total mass of the cylinder/primary region:
Itemized Wall Film Mass and Impinged Mass: If this box is checked,
detailed itemized wall film mass and impinged mass will be reported in two new output files:
itemized_wallfilm_mass.csv and
itemized_impinged_mass.csv. These two files report the wall film/impinged
mass from every individual nozzle onto every individual wall boundary. The total number of
output variables equals the number of nozzles times the number of wall boundaries. The variable
names are: Film mass from (injector name) (nozzle name) on (wall name)
and
Imp mass from (injector name) (nozzle name) on (wall name)
. Unit is g.
Pocket tracking is used to track the evolution of centroid location, volume, mass, and state variables of enclosed fluid volumes (called pockets). This feature is typically used in compressor or pump applications.
Check the Enable Pocket Tracking check box to turn on this feature. When this feature is enabled, Forte will track contiguous pockets of fluid in the computational domain. Gap cells created using Gap Feature Controls are used to define the boundaries for the pockets. Minimum Pocket Volume Fraction sets a volume fraction threshold, in which volume fraction is defined as the volume of a pocket divided by the volume of the whole computational domain. A pocket will be tracked only if its volume fraction exceeds this threshold value. Maximum Number of Tracked Pockets sets the maximum number of pockets that can be tracked at a specific time. This number should be roughly two to three times the maximum number of active pockets coexisting in the fluid domain. Pockets are tracked dynamically in the simulation. The x, y, z coordinates of pocket centroid, total volume, total mass, volume-averaged pressure, and mass-averaged temperature of all the pockets are reported in pocket_tracking.csv. Following here are several notes about the Pocket Tracking feature:
When pocket tracking is turned on, the pocket indices are reported as a spatially-resolved output variable called PocketIndex. It can be visualized in post-processing, for example, in Ansys EnSight. The PocketIndex values correspond to the pocket numbering used in pocket_tracking.csv. The index value of a pocket does not change throughout this pocket's life cycle.
The first several pocket slots in pocket_tracking.csv are reserved for the pockets exposed to open boundaries. These isolated volumes are not really “pockets”, but volumes separated from other volumes by gap cells. Therefore, these special “pockets” are marked as “OPEN_pocket_n”, in which n is the pocket index.
Gap cells are used to separate the fluid domain into pockets, but gap cells are not considered as part of the pockets, so the volume, pressure, temperature, and mass of the pockets reported in pocket_tracking.csv do not consider gap cells.
Since the pockets are defined as volumes separated by gap cells, a pocket will disappear when it merges into other pockets. If there is a need to keep monitoring the pressure in a pocket after it has disappeared, you can consider using the moving (spherical) monitor probe instead.
When the Equivalence Ratio Histogram check box is checked, you can save equivalence ratio distribution results in histogram format for each cylinder region (for engine cases) or primary region (for non-engine cases). To use the uniform bin option, specify the total number of bins and the uniform bin width. The other option is to specify the bin boundaries through a tabulated profile. The tabulation assumes that the lower bound for equivalence ratio is 0 and the upper bound is Infinity. The number of bins equals the number of entries in the table plus one. For example, if you include 0.5, 1.0, 1.5 in the table, four bins will be reported in the output csv files: [0, 0.5), [0.5, 1.0), [1.0, 1.5), and [1.5, ∞).
For each cylinder region or primary region, six output files are written:
phi_histogram_mass.csv: reports the mixture mass contained in each bin.
phi_histogram_massfrac.csv: reports the mixture mass fraction of each bin, which equals the mixture mass in this bin divided by the total mixture mass of the cylinder/primary region.
phi_histogram_avgphi.csv: reports mass averaged equivalence ratio for each bin based on its cell population.
phi_cumulative_distribution_mass.csv
: reports the cumulative mixture mass for the cell population whose equivalence ratio is larger than or equal to a bin boundary value.phi_cumulative_distribution_massfrac.csv: reports the cumulative mixture mass fraction for the cell population whose equivalence ratio is larger than or equal to a bin boundary value.
phi_cumulative_distribution_avgphi.csv: reports the mass averaged equivalence ratio for the cell population whose equivalence ratio is larger than or equal to a bin boundary value.
In addition, if the check box Report Species Mass Distribution is checked, the mass distribution of each of the species in the Spatially Averaged Species list (on the Spatially Averaged and Spray panel) will be reported in the following files:
phi_histogram_[species_name]_mass.csv: reports the mass of the selected species contained in each bin.
phi_cumulative_distribution_[species_name]_mass.csv: reports the cumulative mass of the selected species for the cell population whose equivalence ratio is larger than or equal to a bin boundary value.
When the Enable Time Averaging Output check box is checked, Ansys Forte will calculate the running time-averaged values of flow parameters at open boundaries in open_boundary_flow.csv and calculate the running time-averaged torque, power, and force parameters for rotating or planetary-motion boundaries in rotation_boundary_parameters.csv and planetary_motion_boundary_parameters.csv, respectively. By default, values from all time points will be used to calculate the running time average. If a starting time or starting (global) crank angle is specified, running time average will start after the specified starting point and the output is set to zero before the starting point. If the running average calculation control is modified between a fresh run and a restart run, the following conventions will be used to handle the running average data at the beginning of the restart run:
If the running average has not started yet at the restart time and the new running average starting time/crank angle is earlier than the restart time, running average will begin at the restart time.
If the running average has already started and the new running average starting time/crank angle is earlier than the restart time and different from the old starting time/crank angle, the running average will keep using the old starting time/crank angle in the restart run.
If the running average has already started and the new running average starting time/crank angle is later than the restart time, the running average will begin when the run reaches the new starting time/crank angle.
The parameters reported in the FORTE.log file are described in Table 3.8: Summary Data reported in Ansys Forte log, for engine simulations, including the name of the parameter, its units, and a description of what it represents or how it is calculated.
Table 3.8: Summary Data reported in Ansys Forte log, for engine simulations
Starting with the 2023 R1 release, a new post-processing
tool, the Engine Performance Utility, is available to estimate and customize the engine
performance data. The new tool is accessible from the Utility
ribbon group or menu, and this is the corresponding icon . Since this is a post-processing utility, before using it, make sure that
a working folder exists and contains the full
*.csv
set of spatially averaged data from a previously run engine
simulation. Usually this is the Nominal
folder.
The engine performance utility allows three different engine inputs to calculate:
The Engine Summary with Project Values.
The Engine Summary with User Values.
The 2-Stroke Scavenging Metrics.
The first one is basically an extension of the already existing engine_summary.csv
output file provided at the end of each engine
simulation and is described in Table 3.8: Summary Data reported in Ansys Forte log, for engine simulations
(which is part of the Summary Data Reported in Ansys Forte Log, for Engine Simulations),
with the addition that the new post-processing utility provides a report per cycle and per cylinder, allowing a more detailed analysis of the engine
performance. In the post-processing utility, each cycle is identified by the
[0°;360°] or [0°;720°] local crank angle range. If a cycle is not fully
covered by the simulation, then the performances are evaluated based only on the simulated
portion of the cycle. The simulated cycle coverage is reported. After running the utility, a
new *.csv
output file is generated in the
existing working folder. In the case of a multi-cylinder simulation, N number of engine_summary_custom_X.csv
files are produced, where N is the number of total cylinders, and X is the cylinder ID the report refers to. If multiple cycles per cylinder are
present, an extra column is added per cycle to the engine_summary_custom_X.csv
file.
Table 3.9: Engine Performance output parameters describe the output parameters of the engine performance utility.
Parameter |
Units |
Description |
---|---|---|
Cylinder Index | [-] |
ID of the cylinder analyzed |
Cycle Index | [-] |
ID of the cycle analyzed |
Initial Cyclic CA | [deg] |
Local initial crank angle of the simulated cycle |
Final Cyclic CA | [deg] |
Local final crank angle of the simulated cycle |
Cycle Coverage | [%] |
Percentage of the cycle covered by the simulation |
Engine Bore | [cm] |
Bore diameter |
Displacement Volume | [cm3] |
Cylinder volume swept by the piston engine. It is calculated as:
|
Combustion Chamber Volume at TDC | [cm3] |
Volume of the combustion chamber at TDC |
Geometric Compression Ratio | [-] |
Engine compression ratio, estimated as follows:
where |
Gross Indicated Work | [kJ] |
Gross indicated engine work based on the integration of in-cylinder pressure-volume profiles over the full simulated cycle, where 1 represents the local initial crank angle and N the final one. The gross indicated work is calculated as:
|
Gross Indicated Power | [kW] |
The gross indicated power is based on the gross indicated work evaluated between the initial and final local crank angles. It is estimated as:
in which |
IMEP | [MPa] | Indicated Mean Effective Pressure. IMEP is based on the gross indicated work. The definition is consistent with the gross indicated work and gross indicated power. IMEP is calculated as:
in which |
Total Fuel Mass | [g] |
Total mass of in-cylinder direct injected fuel and premixed fuel to the engine. The premixed fuel is calculated based on all hydrocarbon species and/or hydrogen contained in the intake charge at intake valve closure (IVC). For a multi-cylinder simulation, it is the fuel mass of the entire engine that is split between the cylinders. It can be modified from the utility input interface. |
Fuel Mass per Engine Cycle | [g/cyc] |
The in-cylinder fuel mass per each cycle. For a multi-cylinder and multi-cycle simulation, the sum of all these values gives the total fuel mass of the engine. The amount of fuel share per cylinder can be modified from the utility input interface. |
Fuel Lower Heating Value per g | [kJ] |
Fuel Lower Heating value. It can be modified from the utility input interface. |
Gross ISFC | [g/kW-h] |
Gross Indicated Specific Fuel Consumption, estimated based on fuel mass and power. Gross ISFC is calculated as:
in which |
Combustion Efficiency | [ ] |
Combustion efficiency of the engine, calculated as:
in which |
Thermal Efficiency | [ ] |
Thermal efficiency of the engine, calculated as:
in which |
Max Pressure | [MPa] |
Maximum pressure achieved in the engine during the simulated cycle. |
Max Temperature | [K] |
Maximum temperature reached in the engine during the simulated cycle. |
Max Pressure Rise Rate | [MPa/deg] |
Maximum pressure rise rate reached in the engine during the simulated cycle. |
Total Chemical Heat Release | [J] |
Total heat release from chemical reaction over the simulated cycle. The value is obtained by subtracting the last cycle data point of parameter "Accumulated chemical heat release" reported in thermo.csv from its value at the beginning of simulated cycle. |
Total Wall Heat Transfer Loss | [J] |
Total wall heat transfer loss from the beginning of cycle to the end of it. The value is obtained based on the parameter "Accumulated wall heat transfer" reported in thermo.csv. |
Cooling Loss Ratio | [ ] |
The ratio of Total Chemical Heat Release and Total Wall Heat Transfer Loss over the
simulated cycle, represented by symbol |
Total Apparent Heat Release (Chemical - Heat Loss) | [J] |
Accumulated apparent heat release, calculated as the difference between Total Chemical Heat Release and Total Wall Heat Transfer Loss over the simulated cycle. |
Total Apparent Heat Release (From PV, Variable Gamma) | [J] |
Accumulated apparent heat release, based on the P, V, and gamma time profiles from the beginning of the simulated cycle to the end of it, using variable gamma (specific heat ratio) values. It is calculated based on the parameter "Accumulated apparent heat release from PV-VarGamma" reported in thermo.csv. |
Total Apparent Heat Release (From PV, Constant Gamma) | [J] |
Accumulated apparent heat release, based on the pressure and volume time profiles from the beginning of simulated cycle to the end it, using a constant gamma (1.35). It is calculated based on the parameter "Accumulated apparent heat release from PV-ConGamma" reported in thermo.csv. |
Degree of Constant Volume (Apparent) | [ ] |
Degree of Constant Volume (DCV) based on apparent heat release rate (
where
in which
The Burning DCV (
where |
Degree of Constant Volume (Burning) | [ ] |
Similar to the Apparent DCV, the Burning DCV is defined as:
where |
Degree of Constant Volume (Cooling) | [ ] |
Similar to the Apparent DCV, the Cooling DCV is defined as:
where |
CA @ 2% Heat Release | [deg ATDC] |
Time at which 2% of the accumulated heat release over the simulated cycle is reached, in crank angle degrees. |
CA @ 10% Heat Release | [deg ATDC] |
Time at which 10% of the accumulated heat release over the simulated cycle is reached, in crank angle degrees. |
CA @ 30% Heat Release | [deg ATDC] |
Time at which 30% of the accumulated heat release over the simulated cycle is reached, in crank angle degrees. |
CA @ 50% Heat Release | [deg ATDC] |
Time at which 50% of the accumulated heat release over the simulated cycle is reached, in crank angle degrees. |
CA @ 90% Heat Release | [deg ATDC] |
Time at which 90% of the accumulated heat release over the simulated cycle is reached, in crank angle degrees. |
10%-90% Heat Release Duration | [deg] |
Combustion duration, as measured by the time between 10% and 90% heat release over the simulated cycle, in crank angle degrees. |
Soot @ end of cycle | [g] |
Emissions index for soot at the end of the simulated cycle, in units of grams. |
[g/kg-f] |
Emissions index for soot at the end of the simulated cycle, in units of grams per kilogram of fuel. | |
[g/kW-h] |
Emissions index for soot at the end of the simulated cycle, in units of grams per kilowatt-hour. | |
[ppm] |
Emissions index for soot at the end of the simulated cycle, in units of ppm. | |
EINOx @ end of cycle | [g] |
Emissions index for NOx at the end of the simulated cycle, in units of grams. |
[g/kg-f] |
Emissions index for NOx at the end of the simulated cycle, in units of grams per kilogram of fuel. | |
[g/kW-h] |
Emissions index for NOx at the end of the simulated cycle, in units of grams per kilowatt-hour. | |
[ppm] |
Emissions index for NOx at the end of the simulated cycle, in units of ppm. | |
CO @ end of cycle | [g] |
Emissions index for CO at the end of the simulated cycle, in units of grams. |
[g/kg-f] |
Emissions index for CO at the end of the simulated cycle, in units of grams per kilogram of fuel. | |
[g/kW-h] |
Emissions index for CO at the end of the simulated cycle, in units of grams per kilowatt-hour. | |
[ppm] |
Emissions index for CO at the end of the simulated cycle, in units of ppm. | |
UHC @ end of cycle | [g] |
Emissions index for unburned hydrocarbons at the end of the simulated cycle, in units of grams. Hydrocarbons in this accounting include all species that have non-zero composition for both H and C atoms, including those that contain oxygen. |
[g/kg-f] |
Emissions index for unburned hydrocarbons at the end of the simulated cycle, in units of grams per kilogram of fuel. Hydrocarbons in this accounting include all species that have non-zero composition for both H and C atoms, including those that contain oxygen. | |
[g/kW-h] |
Emissions index for unburned hydrocarbons at the end of the simulated cycle, in units of grams per kilowatt-hour. Hydrocarbons in this accounting include all species that have non-zero composition for both H and C atoms, including those that contain oxygen. | |
[ppm] |
Emissions index for unburned hydrocarbons at the end of the simulated cycle, in units ppm. Hydrocarbons in this accounting include all species that have non-zero composition for both H and C atoms, including those that contain oxygen. | |
VOC @ end of cycle | [g] |
Emissions index for volatile organic compounds at the end of the simulated cycle, in units of grams. VOC species include species containing both H and C atoms, and the species may also contain other atoms, such as oxygen (O) or nitrogen (N). |
[g/kg-f] |
Emissions index for volatile organic compounds at the end of the simulated cycle, in units of grams per kilogram of fuel. VOC species include species containing both H and C atoms, and the species may also contain other atoms, such as oxygen (O) or nitrogen (N). | |
[g/kW-h] |
Emissions index for volatile organic compounds at the end of the simulated cycle, in units of grams per kilowatt-hour. VOC species include species containing both H and C atoms, and the species may also contain other atoms, such as oxygen (O) or nitrogen (N). | |
[ppm] |
Emissions index for volatile organic compounds at the end of the simulated cycle, in units of ppm. VOC species include species containing both H and C atoms, and the species may also contain other atoms, such as oxygen (O) or nitrogen (N). |
The second option focuses as well on the engine summary report but provides the flexibility to override a set of parameters to see their effects on the engine performance. Those parameters are:
The total fuel mass injected. It allows accounting for extra premixed/fuel.
The lower heating value. A tunable single value for the fuel composition is employed in the simulation. Instead of using the default values of 44 kJ/g and 120 kJ/g for premixed hydrocarbon species and hydrogen, respectively, you can input its estimated value.
The multi-cylinder fuel mapping. Applicable only for multicylinder cases, it allows customizing the fuel split between cylinders instead of using the default uniform distribution among all the cylinders.
The third option calculates the scavenging metrics for 2-stroke engines and writes them out to a file, scavenging_metrics_x.csv, in the running directory. The input panel requires specifying:
The running directory where all the csv files generated from the run can be found.
The reference density. The default value is set to 1.225 kg/m3, the air density at standard temperature and pressure conditions.
The exhaust port closing (EPC) global crank angle.
The intake port regions from which the flow is entering into the cylinder at EPC.
Table 3.10: Scavenging metrics output parameters describes the output parameters of the scavenging metric utility.
Table 3.10: Scavenging metrics output parameters
Parameter name | Units | Description |
Cylinder Index | [-] | ID of the cylinder analyzed |
Engine Bore | [cm] | Bore diameter |
Engine Stroke | [cm] | Stroke length |
Displacement Volume | [cm3] |
Cylinder volume swept by the piston
|
Reference Cylinder Mass | [g] |
Reference cylinder mass
|
Mass of Fresh Charge Delivered or Ingested | [g] |
Accumulated mass flow from intake ports to cylinder at EPC (from flow_into_cylinder.csv )
|
Mass of Fresh Charge Trapped | [g] |
In-cylinder mass of fresh charge species at EPC (from species.csv)
|
Total Trapped Mass-Including Residuals | [g] |
In-cylinder total mass at EPC (from thermo.csv)
|
Mass of Short-circuiting | [g] |
Difference between the mass of fresh charge delivered and trapped.
|
Trapping Efficiency | [-] |
Ratio between the trapped mass and the freshly delivered mass.
|
Scavenging Efficiency | [-] |
Ratio between the trapped mass and the trapped mass including residuals.
|
Relative Charge | [-] |
Ratio between the trapped mass including residuals and the cylinder mass.
|
Delivery Ratio | [-] |
Ratio between the freshly delivered mass and the cylinder mass.
|
Charging Efficiency | [-] |
Ratio between the trapped mass and the cylinder mass.
|
The engine summary utility can also be run from the Ansys Forte Command-Line Interface (CLI). After setting up the Forte environment as described in the Command-line Interface, run from the terminal the following command (these examples are described for Linux systems).
For the first two examples, Example 3.1: ENG_SUMM.txt for the Engine input option: Engine Summary with Project Values and Example 3.2: ENG_SUMM.txt for the Engine input option: Engine Summary with User Values. , use the following command:
>> forte.sh CLI -project <ProjectPath>\MyProject.ftsim --engine_performance -engine_input <PathToInputFile>\ENG_SUMM.txt
where the ENG_SUMM.txt
is an input file
containing all the user-defined values. See the examples below, one for each engine performance
option.
Example 3.1: ENG_SUMM.txt for the Engine input option: Engine Summary with Project Values
ENGINE_SUMMARY_CONTROLS:
running_dir = "<ProjectPath>\Nominal"
engInputs_option = "Engine Summary with Project Values"
END
Example 3.2: ENG_SUMM.txt for the Engine input option: Engine Summary with User Values.
The Multi-Cylinder Four-Stroke Engine Simulation in the Ansys Forte Tutorials is used for this example, in which the total fuel mass, the lower heating values, and the fuel mass split per cylinder are overridden.
ENGINE_SUMMARY_CONTROLS:
running_dir = "<ProjectPath>\Nominal"
engInputs_option = "Engine Summary with User Values"
enable_user_totFuelMass = true
totFuelMass_engsumm = 2.5 [g]
enable_user_lhv = true
lhv_engsumm = 42 [kJ/g]
enable_fuel_to_cyl = true
fuel_to_cyl = {{"ID 1",0.3},{"ID 2", 0.2},{"ID 3", 0.3},{"ID 4", 0.2}}
END
For Example 3.3: ENG_SUMM.txt for the Engine input option: 2-Stroke Scavenging Metrics, replace the
--engine_performance
option with the --engine_scavenging
option and
use the following command:
>> forte.sh CLI -project <ProjectPath>\MyProject.ftsim --engine_scavenging -engine_input <PathToInputFile>\ENG_SUMM.txt
The related ENG_SUMM.txt
looks like:
Example 3.3: ENG_SUMM.txt for the Engine input option: 2-Stroke Scavenging Metrics
The Two-Stroke Engine Simulation in the Ansys Forte Tutorials is used for this example.
ENGINE_SUMMARY_CONTROLS:
running_dir = "<ProjectPath>\Nominal"
engInputs_option = "2-Stroke Scavenging Metrics"
rhoA_scavenging = 1.225 [kg/m3]
EPC_scavenging = 261.7 [degrees]
intake_region_scavenging = {"Intake1","Intake2", "Intake3"}
END
The Output Controls node on the Workflow tree offers Spatially Averaged and Spray Analysis. Select this option if you want to investigate spray data in a customized way. With the Penetration Analysis Editor panel, you can select any defined nozzles or injectors to study (see Spray Model for defining nozzles under Spray Models).
For nozzle-based analysis, the following four variables, which are described in Table 3.11: Spray penetration data available for reporting in custom_spray_penetration.csv, may be selected for output: Axial penetration, radial penetration, normal penetration, and spray angle. For injector-based analysis, you need to specify the origin and direction of the axis for the whole injector. The liquid and vapor penetration length thresholds can be customized as well.
The resulting output will be written in a file named custom_spray_penetration.csv, which will be located in the working directory together with other spatially averaged data files. This .csv file contains both nozzle-based and injector-based analysis results. The output variable names start with a(num)_, where (num) is the index of the customized analysis following its order on the setup tree.
Table 3.11: Spray penetration data available for reporting in custom_spray_penetration.csv
Spray Analysis Data in custom_spray_penetration.csv, depending on options | ||
---|---|---|
Axial Penetration (For nozzle-based analysis, variable name ends with '_AxialP (mm)') |
[mm] |
For the calculation, all spray parcels are projected onto the axis of the nozzle that injects them, and then the mass of these liquid parcels is accumulated starting at nozzle exit. The axial penetration is defined as the distance between the nozzle exit and the location where the accumulated liquid mass reaches a threshold fraction of the total liquid mass specified by the cutoff parameter. Note: The definition of this parameter is essentially the same as that of "Liquid penetration length" shown in Table 3.6: Spatially averaged variables that are always output to the .csv files, except that the threshold fraction of the liquid mass is adjustable by "cutoff" instead of fixed as 95%. |
Radial Penetration (For nozzle-based analysis, variable name ends with '_RadialP (mm)') |
[mm] |
For the calculation, the mass of the spray parcels is accumulated starting at nozzle exit. The radial penetration length is defined as the absolute distance between the nozzle exit and the spray parcel location where the accumulated liquid mass reaches a threshold fraction of the total liquid mass specified by the "cutoff" parameter. |
Normal Penetration (For nozzle-based analysis, variable name ends with '_NormalP (mm)') |
[mm] |
For the calculation, all spray parcels are projected onto the axis of the nozzle that injects them, and then the mass of these liquid parcels is accumulated starting at the axis of the nozzle. The normal penetration is defined as the normal distance between the nozzle axis and the location where the accumulated liquid mass reaches a threshold fraction of the total liquid mass specified by the "cutoff" parameter. It is a measure of spray diffusion away from the axis of injection. |
Spray Angle (For nozzle-based analysis, variable name ends with '_SprayAngle (deg)') |
[degree] |
For the calculation, all spray parcels are projected onto the axis of the nozzle that injects them, and then the mass of these liquid parcels is accumulated starting at the axis of the nozzle. For each spray parcel, a spreading angle can be defined by evaluating the ratio of its normal distance to the nozzle axis to its axial distance from the nozzle exit. A half-spray-cone angle is then defined where the accumulated liquid mass reaches a threshold fraction of the total liquid mass specified by the "cutoff" parameter. The spray angle reported doubles the half-spray-cone angle. |
Injector Liquid Penetration (For injector-based analysis, variable name ends with '_LiqPene (mm)') |
[mm] |
Liquid penetration along a user-specified injector axis. The calculation method of this parameter is essentially the same as that of "Liquid penetration length" shown in Table 3.6: Spatially averaged variables that are always output to the .csv files for spray.csv, except that (1) the threshold fraction of the liquid mass is customizable instead of being fixed at 95%, and (2) the analysis is along the user-specified injector axis instead of a nozzle axis. |
Injector Vapor Penetration (For injector-based analysis, variable name ends with '_VapPene (mm)') |
[mm] |
Vapor penetration along a user-specified injector axis. The calculation method of this parameter is essentially the same as that of "Vapor penetration length" shown in Table 3.6: Spatially averaged variables that are always output to the .csv files for spray.csv, except that (1) the threshold fraction of the vapor mass is customizable instead of being fixed at 99.9%, and (2) the analysis is along the user-specified injector axis instead of a nozzle axis. |
Figure 3.25: Illustration of axial and radial penetrations (assuming the liquid mass threshold "cutoff" is 100%)
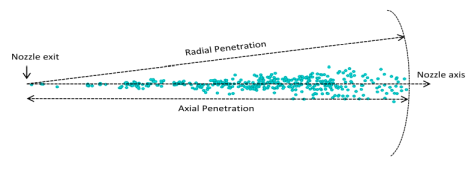
Figure 3.26: Illustration of normal penetration (assuming the liquid mass threshold "cutoff" is 100%)

In an engine system, it is often desirable to monitor the mass flow rate and accumulated mass flow through valves or ports between an engine cylinder and regions connected to it. The standard spatially averaged output flow_into_cylinder.csv reports these quantities, but it only reports the total mass flow through all the valves or ports that connect a cylinder region and a neighboring non-cylinder region. In practice, there may be more than one valve or port connecting the cylinder and the non-cylinder region. Port Flow Monitor can be used to monitor the mass flow through each individual valve/port or a selected group of valves/ports.
For each port flow monitor, you can select which valve(s)/port(s) to monitor by drawing either a bounding box or a bounding sphere that completely encompasses them. If the bounding box option is selected, a reference frame can be used to define the orientation of the box. The length, width, and height of the box are assumed to be aligned with the x, y, z-axes of the local reference frame. The specified location marks the center of the box. If the bounding sphere option is selected, the specified location marks the center of the sphere.
In a multicylinder simulation, if port flow monitors are used, an output file called port_flow_monitor_n.csv will be created for each cylinder, in which n corresponds to the cylinder index. Within each port_flow_monitor_n.csv, mass flow rate and accumulated mass flow through all the monitored valves/ports will be reported. The reported values follow the same sign convention as the one used by flow_into_cylinder.csv: positive if flow goes into the cylinder; negative if flow goes out of the cylinder.