The following topics about applying boundary conditions (BCs) and loading are available:
Internal heat generation loads are applied to selected MESH200 element components representing the embedded copper traces and vias:
After the reinforcings have been created (EREINF) from MESH200 and base-element intersections, the boundary conditions applied on MESH200 are transferred to the smeared reinforcing members (BFPORT):
Figure 59.6: Internal Heat Generation of 2 W/mm3 Transferred from Surface MESH200 to Generated REINF265 Members
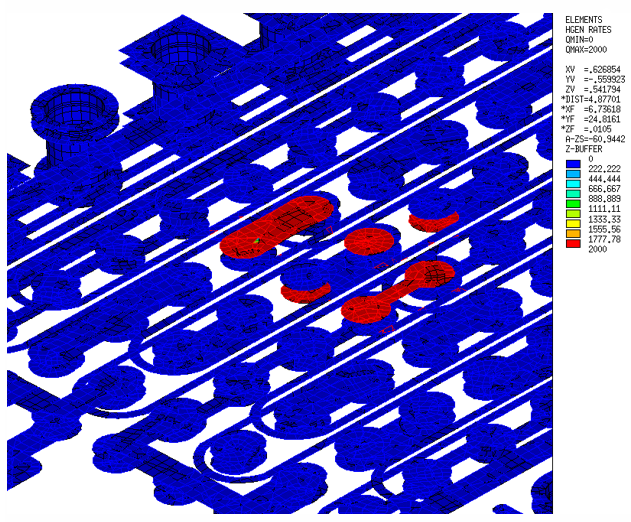
Convection boundary conditions are applied on the top and bottom faces of the PCB: