In this tutorial, you will use the Short Fiber Composite SN Analysis in the DesignLife Add-on to carry out a fatigue analysis on a typical test coupon, which has been manufactured by machining an injection moulded flat plate. This analysis capability has been targeted at short fiber injection-moulded composites, but is in principle also applicable to laminates.
Analysis Type | Fatigue |
Features Demonstrated | DesignLife Add-on, DesignLife system, vibration fatigue, inputs and loading conditions |
Licenses Required | Ansys Mechanical Enterprise PrepPost and Ansys nCode Enterprise |
Help Resources | DesignLife Add-on |
Tutorial Files | FatigueShortFiber.zip |
This tutorial guides you through the following topics:
- 18.1. Problem Description
- 18.2. Access Data Files
- 18.3. Review FE Results
- 18.4. Load the DesignLife Add-on
- 18.5. Insert a DesignLife System
- 18.6. Configure Short Fiber Composite Analysis
- 18.7. Define Orientation Tensor File
- 18.8. Define Inputs and Loading Conditions
- 18.9. Solve and Review the Results
- 18.10. Materials Database Definition
The challenges in estimating damage in composite materials (as compared with metals) derive from the fact that, in general, composite materials are inhomogeneous and anisotropic. Their physical properties may vary throughout a structure and be strongly directional. In order to obtain any useful estimate of damage, it is essential that the inhomogeneity and anisotropy of the material are taken into account both in the structural FE analysis (defining the load-stress transfer function) and in the fatigue analysis (defining the stress-life relationship).
In this tutorial, you will use the Short Fiber Composite SN Analysis in the DesignLife Add-on to carry out a fatigue analysis on a typical test coupon, which has been manufactured by machining an injection moulded flat plate. This analysis capability has been targeted at short fiber injection-moulded composites, but is in principle also applicable to laminates.
Data files for this tutorial can be found here on the Ansys customer site.
The files you need are:
SHORT_FIBER_TIME_DOMAIN.wbpz - this is the model that you will set up by following the steps below. Copy the file to a working folder and complete the worked example using the copy. Make sure that you have write permission to the working folder.
FOT_Fatigue90deg.csv and FOT_Fatigue0deg.csv - these are the orientation tensor files.
Lomov_coupon_R01.mxd - this is the materials database.
This example models a tensile specimen test, held at one end and with an enforced displacement of 0.86 mm at the other end to simulate the maximum load.
First, review the results from the finite element analysis:
Start Workbench, and select
> .Browse to the working folder and select SHORT_FIBER_TIME_DOMAIN.wbpz.
Open the Static Structural - 90 deg system in Mechanical by double-clicking the Model cell and review the different results as shown below:
Total Deformation
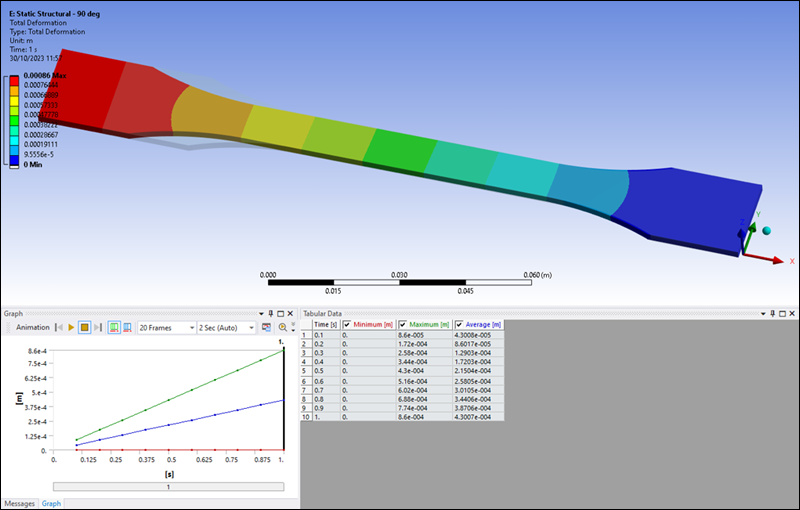
Normal Stress
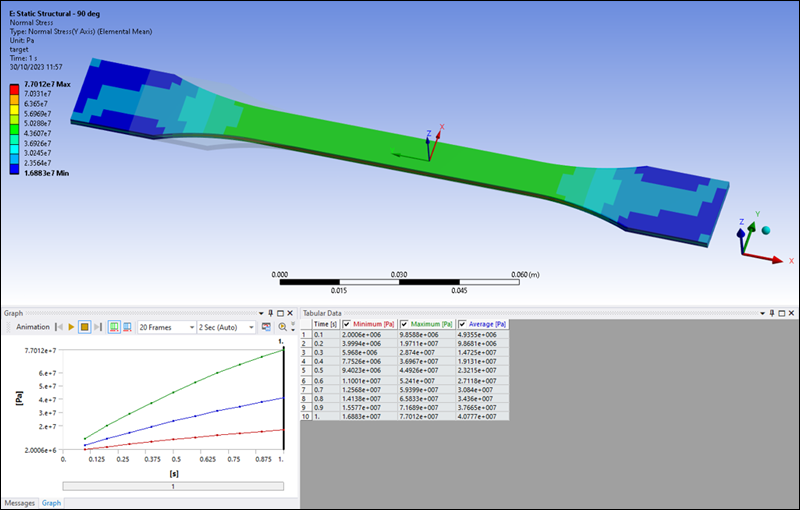
Review the Normal Stress in each direction and note the difference between the different layers:
Normal Stress X-Axis
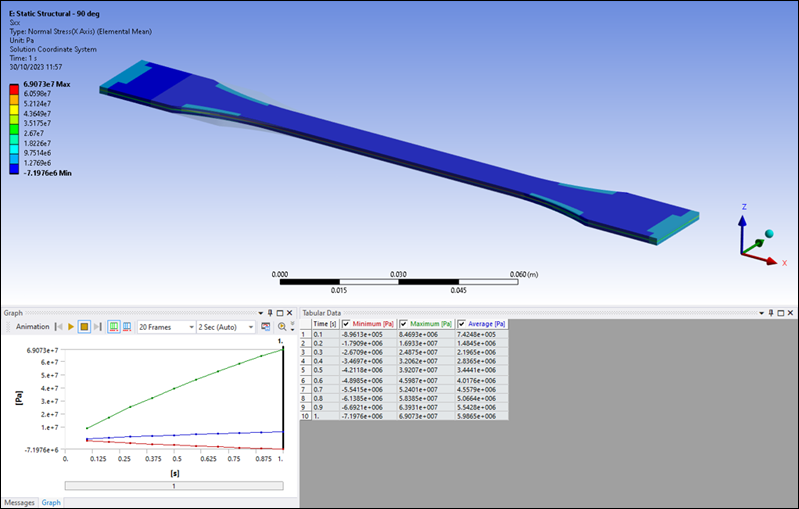
Normal Stress Y-Axis
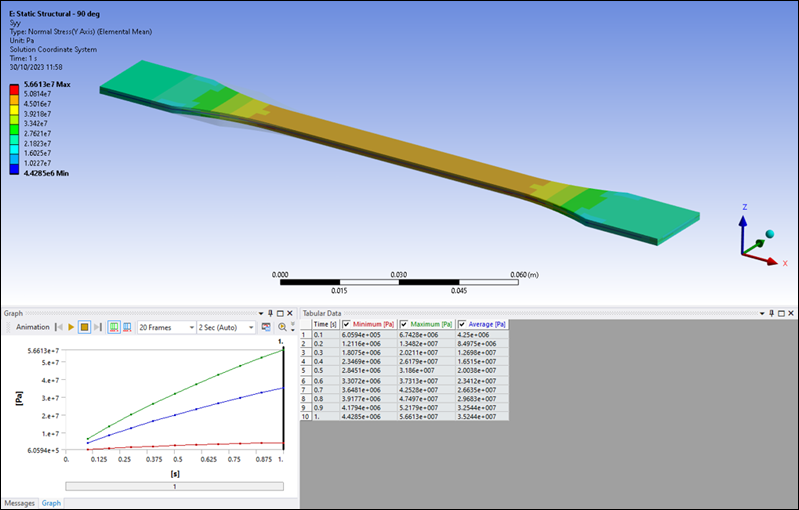
Normal Stress Z-Axis
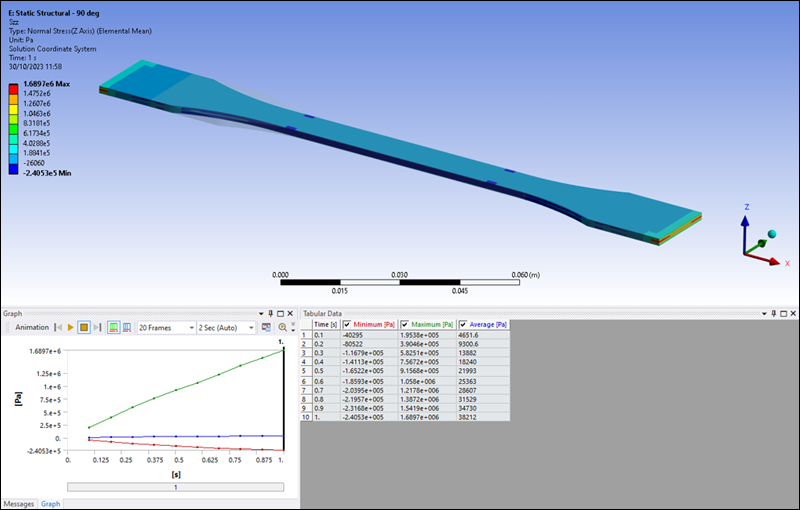
Review the Shear Stress for the different orientations and note the difference between the different layers:
Shear Stress XY Component
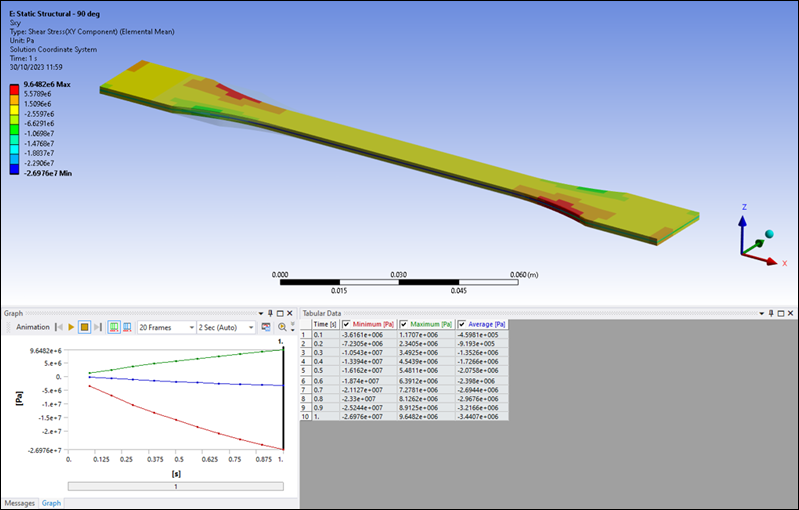
Shear Stress YZ Component
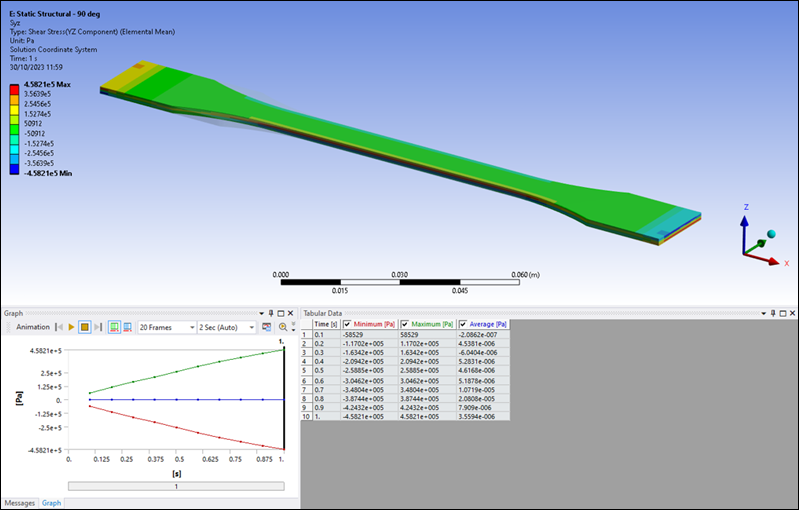
Shear Stress XZ Component
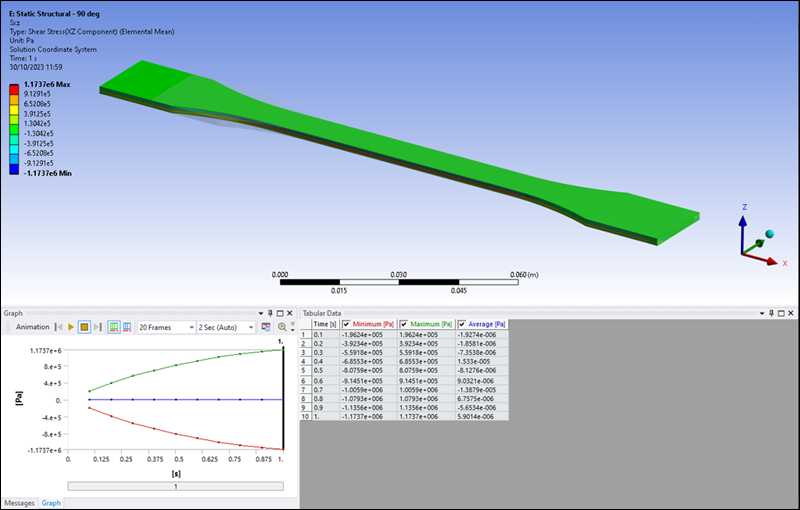
To make the DesignLife capabilities available, click the
icon in the ribbon.The icon is highlighted in blue, indicating that the add-on is loaded.
Once the add-on is loaded, the Ansys nCode DesignLife ribbon is visible, exposing all the DesignLife capabilities.
From the DesignLife ribbon, select to insert a new DesignLife analysis directly from Mechanical.
Click the New Analysis icon and verify that the nCode DesignLife (F5) object is inserted into Mechanical.
For this example, you will perform a Analysis Domain defaults to the option when the DesignLife system is connected to a Static Structural system.
fatigue calculation using Constant Amplitude loading. TheSelect the
analysis type to perform the nCode Short Fiber Composite Analysis Engine. This analysis engine performs an SN-based analysis using short fiber, orientation-dependent materials.The Basquin method is used to define the SN curves for the fatigue calculation (SNMethod) for Short Fiber Composite Analysis. This method uses a set of one or more parameterized stress-life curves and interpolates between them (or extrapolates) based on the share of fibers in the direction of the loading. Each individual SN curve is similar to the standard SN formulation.
The local SN curve will be determined based on a set of SN (Basquin) curves from the nCode MXD database. The corresponding Material Type property for the material map should be set to . The dataset used for Short Fiber Composite Analysis is the nCodeSFCBasquinCurveContainer.
The only supported Solution Location for Composite Analysis is . Results will be recovered from the element centroid. If element centroid results are not available in the FE results file, nCodeDT will average the stresses from the nodes.
The EntityDataType nCode property is set to . Stresses will therefore be recovered from the FE results file. Stresses can result from a static, transient, or modal analysis, but will normally be from an elastic analysis.
Select the Analysis Settings element under nCode DesignLife (F5) and ensure that Analysis Domain is set to .
Set the Analysis Type to . The main objects required for a DesignLife analysis are then generated automatically. These are the Solution Group, Load Mapper and Materials objects.
In the Details panel for the Analysis Settings, set the following values:
Mean Stress Correction to
None
Multiaxial Assessment to
Standard
Combination Method to
Abs Max Principal
The Orientation Tensor File must be defined for the Short Fiber Composite analysis. Composites, in general, have anisotropic structures and properties.
The material orientation tensor describes the microstructure in terms of the distribution of fiber orientations at each calculation point (element, layer, section point) in the structure and this information is required if nCodeDT is to take into account the anisotropy of fatigue properties in the analysis.
The material orientation tensor will normally be derived from a simulation of the manufacturing process. The nCode MaterialOrientationTensor property is set to and the file specified by Orientation Tensor File must be in the Glyphworks-compatible CSV format described under Analysis Settings in the Mechanical Add-ons Guide.
In the Details panel for the Analysis Settings, select
FOT_Fatigue90deg.csv
from your working folder as the Orientation Tensor File.Set the Number of Translational Processes to
1
.
The Solution Group defines the portion of the geometry that will be used for the fatigue analysis calculations. By default, all bodies are selected. In the case of this tutorial model, Geometry is therefore set to .
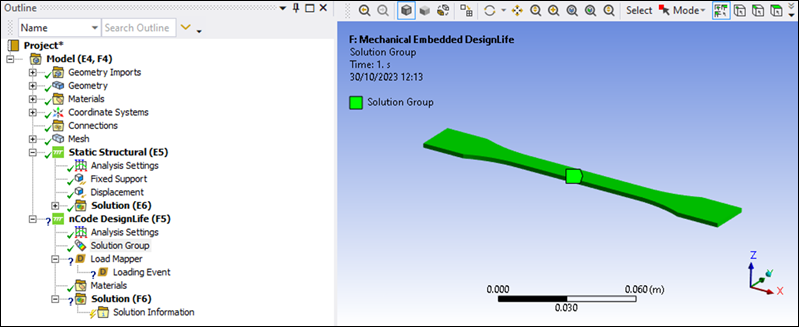
The fatigue loads can be specified as either
, or for the domain.
Select the Load Mapper and click the button next to .
Click Loading Event.
. This adds the firstEnsure that the Type for this event is set to .
Set the Repeat Count for the Loading Event to
1
.Under Add Load in the Loading Event, click and then click .
This creates a Constant Amplitude Load object.
Set the following options for the newly-created Constant Amplitude Load object:
Environment - this selects the system from which the *.rst file will be picked for the nCode fatigue analysis. Select the environment so that the results of the static system are used.
Define By - the loading can be defined by or . In this case, select and then choose the loading corresponding to
0.5 s
in the Static Structural system.Max Factor - set this parameter to
1
.Min Factor - set this parameter to
-1
.These two values mean that the FE results will be scaled by 1 (Max Factor) and then by -1 (Min Factor) to form the 2-point constant-amplitude cycle.
Right-click the Solution (F6) object in the project tree and select .
While solving, selecting Solution Information will show the solver's progress and display errors as they are encountered.
The fatigue results may be viewed as either life or damage. You can add a result by selecting the DesignLife toolbar with the Solution active in the tree.
Alternatively, right-click the Solution (F6) object and insert the following results:
Select
> and set the Maximum Life displayed to 1e10.Select
> and set the Minimum Damage displayed to 1e-10.
Right-click the Solution (F6) object in the project tree and (see below).
The results are shown as a contour plot in the Mechanical graphics window. The tabular data (below) shows the most damaged ElementID and its corresponding Life or Damage.
The default materials applied for the analysis are taken from the
iceflow_standard.mxd database, which can be found in the
mats folder in the nCode installation. When the Analysis
Type is set to , the default
material is Valox 508 GF30
.
You will now modify the default material for Short Fiber Composite analysis:
Scope the body using the
selection tool in Mechanical.Select the Materials object under nCode DesignLife (F5) in the project tree.
In the Modify Material Parameters field, click .
Click Materials Assignment object.
. This creates a newClick in the Database field and select the Lomov_coupon_R01.mxd as the *.mxd database file where all the nCode materials are defined.
This file is copied to the current directory. The DesignLife Add-on filters the materials found in this database. For
, it lists those that are valid for Short Fiber Composite analysis (nCodeSFCBasquinCurveContainer type).In the Material fields, select the new
lomov_coupon
material.Solve again and see how the material assignment impact on the results.
Life Result
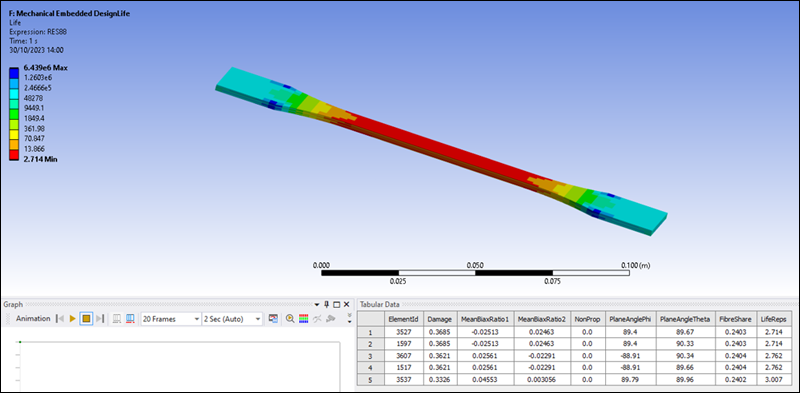
Damage Result
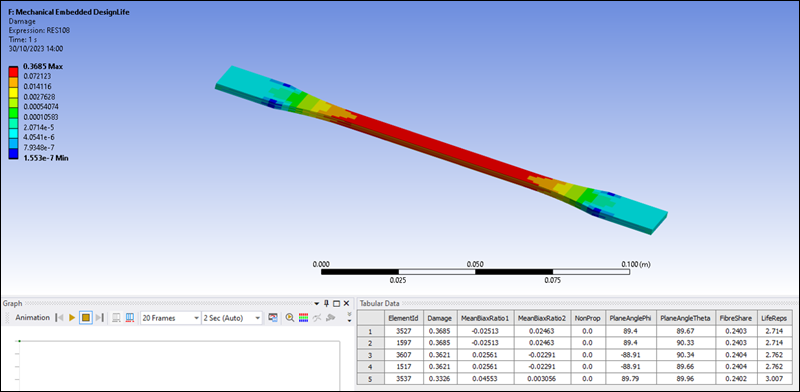
You have completed the fatigue analysis and accomplished the overall objective for this tutorial.
Congratulations! You have completed the tutorial.