NLAD-ETCHG criteria are the rules used to determine whether the mesh type must be changed and, if so, which component (as scoped to a whole part) should be modified. Several criteria types are available. You determine how frequently the criteria should be checked.
When the defined criteria are met, the mesh-type change occurs via general remeshing. For NLAD-ETCHG, general remeshing applies only to:
Energy-based (NLADAPTIVE,,,ENERGY) and position-based (NLADAPTIVE,,,BOX) criteria.
During remeshing, the selected hex-dom component(s) are completely remeshed to obtain a tetrahedral mesh whose element edge lengths are the same as that of the deformed hex-dom mesh. The remeshing operation effectively refines the mesh, as the tetrahedral element volume is smaller than a hexahedral element volume with the same edge length.
Mesh-quality-based criteria.
During remeshing, the selected region is completely remeshed to obtain a high-quality tetrahedral mesh.
The following topics about NLAD-ETCHG criteria are available:
Also see Specifying Criteria-Checking Frequency.
The energy-based criterion is based on the magnitude of strain energy of the
element compared to the mean strain energy of components to which the element
belongs. During the substep at which the element's strain energy is greater than or
equal to the mean strain energy of its components times the user-defined
VAL1
(NLADAPTIVE,ADD), the entire
component is remeshed even if only one element's strain energy exceeds the mean
strain energy.
Use this criterion to create a denser (by volume) tetrahedral mesh from a hex-dom
mesh to achieve high-accuracy simulation in regions where a high concentration of
stress exists and elements are too large. You can also use it to refine the mesh at
specific intervals of substeps if a very small value or 0 is input for
VAL1
in subsequent substeps when the tetrahedral mesh
has been created.
Example 4.3: A Typical Case for Energy-Based Criterion in NLAD-ETCHG
NLAD-ETCHG for energy-based criteria at the first two checking frequencies (N and N +M):
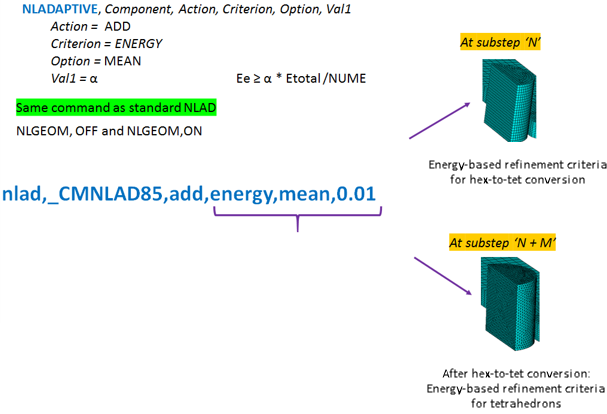
The position-based criterion is defined by a region in global Cartesian coordinates.
If all nodes of any element within the NLAD-ETCHG component are within the defined region during the substep at which NLAD-ETCHG criteria are checked, the entire component is refined via general remeshing.
Use this criterion to refine the mesh in regions where it is difficult to predict which elements of the model will be present or will move into. It is commonly used in rubber seal analysis where small cavities are filled by the deformation of a compressed seal.
If some elements could potentially move into two different regions, define two different components for the same elements so that one component can be associated with each region. In such a case, the NLAD-ETCHG will remesh the whole component based on the first region any of the elements move into.
Example 4.4: A Typical Case for Position-Based Criterion in NLAD-ETCHG
NLAD-ETCHG for position-based criteria at the first two checking frequencies (N and N + M):
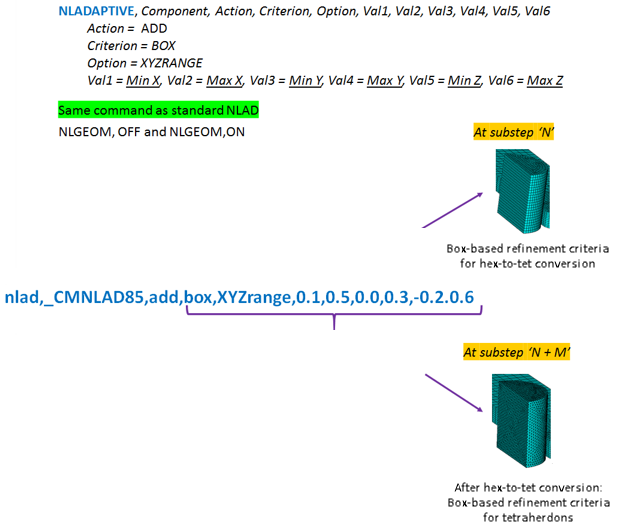
The element components chosen to define a mesh-quality-based criterion should include only the elements falling into the large-deformation region, as long as the components are modeled as shown in Figure 4.1: Multipart Multibody Schematic. When creating your model, design the components carefully to ensure that they are scoped on a full body.
The mesh-quality-based criterion (NLADAPTIVE,,,MESH) as applied to NLAD-ETCHG uses two simultaneous criteria:
SHAPE Option (for converting SOLID185/SOLID186)
SKEWNESS Option with Jacobian Ratio (for subsequent remeshing of SOLID187)
If you specify only the SHAPE option on an initial hex-dom component, NLAD-ETCHG remeshes the SOLID185/SOLID186 mesh in the component to a SOLID187. After the SOLID187 mesh is created, however, no further remeshing or other changes occur to the component unless you specify a new criterion on it.
If you specify only the SKEWNESS option on an initial hex-dom component, no remeshing change occurs to the component.
Both options must be specified to perform an element-type-change remeshing and the subsequent continued remeshing (as needed) of the tetrahedral mesh.
The SHAPE criterion is applied to the 3D element
SOLID185 or SOLID186. Mesh
quality is defined by element shape
(NLADAPTIVE,,,MESH,SHAPE,VAL1
).
The mesh quality value is defined by the element's maximum corner angle; when
the angle equals or exceeds the specified threshold (set via
NLADAPTIVE), the element is identified as a seed element.
At this point, the entire component containing this element is remeshed to
SOLID187 elements.
The recommended maximum corner angle is 150 to 175, although any positive value between 90 and 180 is valid. A larger value results in a later triggering of the first NLAD-ETCHG remesh and can result in fewer total remeshings and can introduce mapping errors, leading to residual forces that cannot be balanced in later substeps. A limiting angle value that is too small results in a premature triggering of the first NLAD-ETCHG remesh, eliminating the advantage of NLAD-ETCHG to better model hex-dom mesh deformation with tetrahedrons.
To prevent excess deformation of the hex-dom mesh, especially for SOLID186 with hyperelastic material models (leading to inaccurate solution mapping to tetrahedral meshes), two more criteria are invoked automatically (in addition to the SHAPE criterion) at the checking frequency: the warp factor (maximum limiting value = 0.3) and the nodal Jacobian Ratio (minimum limiting value = 0.02). Remeshing is triggered if either criterion is violated by any element in the component.
The SKEWNESS criterion applies to structural 3D solid elements SOLID187 (a quadratic tetrahedral element) after the NLAD-ETCHG procedure has remeshed the hex-dom component to a SOLID187 component.
Mesh quality for SOLID187 is defined by element
skewness and the maximum Jacobian ratio at Gaussian points
(NLADAPTIVE,,,MESH,SKEWNESS,VAL1
,VAL2
).
For more information, see Mesh-Quality-Based Criterion.
Example 4.5: Specifying Mesh-Quality-Based Criterion in NLAD-ETCHG
NLAD-ETCHG for mesh-quality-based criteria at the first two checking frequencies (N and N + M):
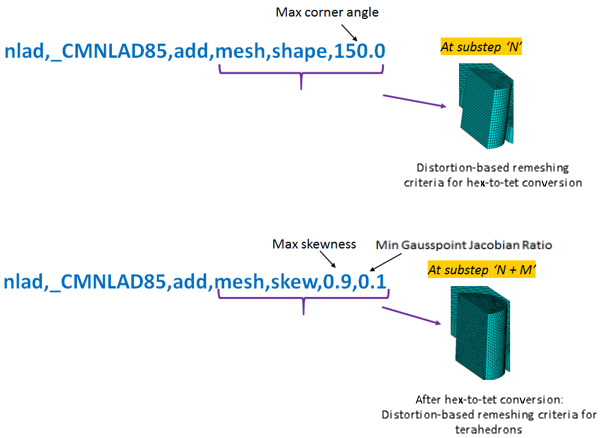
Initial hex-dom meshes with SOLID186 from Ansys Mechanical use SOLID187 elements instead of degenerate SOLID186 tetrahedrons. A typical NLAD-ETCHG component, therefore, has two element types.
The component's SOLID187 elements may deform faster that the SOLID186 elements. Therefore, when using the mesh-quality-based criterion, NLAD-ETCHG may trigger the SKEWNESS option first and convert all elements in the component to SOLID187 (even though the SOLID186 elements may still be acceptable with respect to their own mesh-quality based acceptance threshold).
You can prevent such behavior by controlling the remeshing frequency and
checking-time ranges for both SHAPE and SKEWNESS criteria
(NLADAPTIVE). Try to avoid overlap in the starting
and ending mesh-checking time limits (VAL2
and
VAL3
when Action
=
ON) between the SHAPE and the SKEWNESS criteria.