As an alternative to using Mechanical's predefined sample materials for additive manufacturing, you may choose to use a material from the JAHM Curve Data database in Granta MI's material library. JAHM Curve Data provides temperature-dependent curve data for thousands of materials across 27,000+ records. It includes mechanical, thermal, physical, electrical, fatigue, creep, stress-strain, and magnetic properties for materials in a range of physical states (gas, liquid, solid) and covers temperatures ranging from -270°C to over 5,000°C.
When choosing a material from JAHM Curve Data, keep in mind that AM simulations in Mechanical are currently limited to metal materials. Furthermore, the metals included in the JAHM database are not additive specific. That is, the test specimens were not additively manufactured. However, there may be times when you want to use a material from this source. For this reason, we have provided the following procedure and guidance for using JAHM Temperature-Dependent Material Data in an AM simulation.
First let's review the material properties required to perform AM simulations in Mechanical. The following figure shows the required material properties, as depicted by screen captures from Workbench's Engineering Data. The selected material happens to be the Ansys Ti-6Al-4V sample material. The 12 properties are: Density; Coefficient of Thermal Expansion; Zero-Thermal-Strain Reference Temperature; Melting Temperature; Thermal Conductivity; Specific Heat; Young's Modulus, Poisson's Ratio, Bulk Modulus, and Shear Modulus for the Isotropic Elasticity model; and Yield Strength and Tangent Modulus for the Bilinear Isotropic Hardening model. Note that Isotropic Thermal Conductivity and Specific Heat are required only when performing simulations with thermal solves, such as AM LPBF Thermal-Structural.
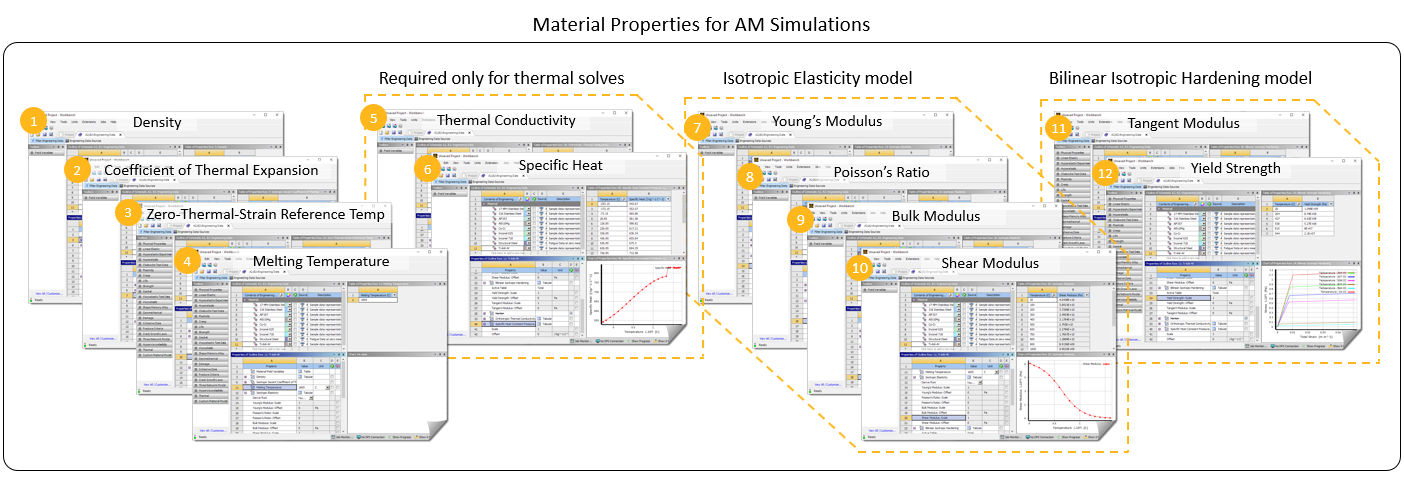
When using JAHM materials, most of the required data is available on a single material record reflecting "general properties" for a given material, which can be exported as a material card from Granta MI and imported directly into Engineering Data. However, a few pieces of data are usually missing from the general properties record and you must provide the missing data. In many cases, the Bilinear Isotropic Hardening model data, from true stress-strain (tension) tensile testing, is not included in a material record that includes all the other required mechanical and thermal properties. This is because true stress-strain is very dependent on the specific manufacturing and heat treatment processes, as well as on tensile test conditions, such as strain rate, hold time, and so on. To handle this, search for a record that contains true stress-strain (tension) data corresponding to your preferred scenario for your chosen material. From that data, you will derive the Yield Strength and Tangent Modulus for the Bilinear Isotropic Hardening model. You may need to refer to other sources to get the single data points of Zero-Thermal-Strain Reference Temperature and/or Melting Temperature.
The following table summarizes the required properties for AM simulation when using a JAHM temperature dependent material.
Material Properties Required for AM Simulation | |||
---|---|---|---|
Property | Form | Components | Source |
Density | Tabular | Temperature, Density | Direct import from Granta MI |
Isotropic Coefficient of Thermal Expansion (CTE) | Tabular | Temperature, CTE | Direct import from Granta MI |
Zero-Thermal-Strain Reference Temperature | Single data point | Temperature | Other source |
Melting Temperature | Single data point | Temperature | Other source |
Isotropic Elasticity model: | Tabular | Temperature, Young's Modulus, Poisson's Ratio, Bulk Modulus, Shear Modulus | |
Young's Modulus | Direct import from Granta MI | ||
Poisson's Ratio | Direct import from Granta MI | ||
Bulk Modulus | Direct import from Granta MI | ||
Shear Modulus | Direct import from Granta MI | ||
Bilinear Isotropic Hardening model: | Tabular | Temperature, Yield Strength, Tangent Modulus | |
Yield Strength | Direct import from Granta MI | ||
Tangent Modulus | Derived from true stress-strain curves | ||
Thermal Conductivity[a] | Tabular | Temperature, Thermal conductivity X, Y, Z | Direct import from Granta MI |
Specific Heat[a] | Tabular | Temperature, Specific heat | Direct import from Granta MI |
[a] Required only for Thermal-Structural simulations
The steps for using JAHM temperature-dependent material data in an additive manufacturing simulation are:
We'll use Ti-6Al-4V as an example material throughout this documentation and we'll use Granta MI Explore to search for the desired JAHM material in Granta MI. We will need more than one material record to get all the required properties.
Search for material record representing general properties
Important: Either a Granta Selector or a Granta MI license is required to get access to JAHM datasets. If you do not see the features used in this example on your system, check with your Granta MI Administrator, as many features are configurable, such as the Export to Excel feature.
Open Granta MI and, from the Explore menu drop-down, choose JAHM Curve Data and then JAHM All Curves.
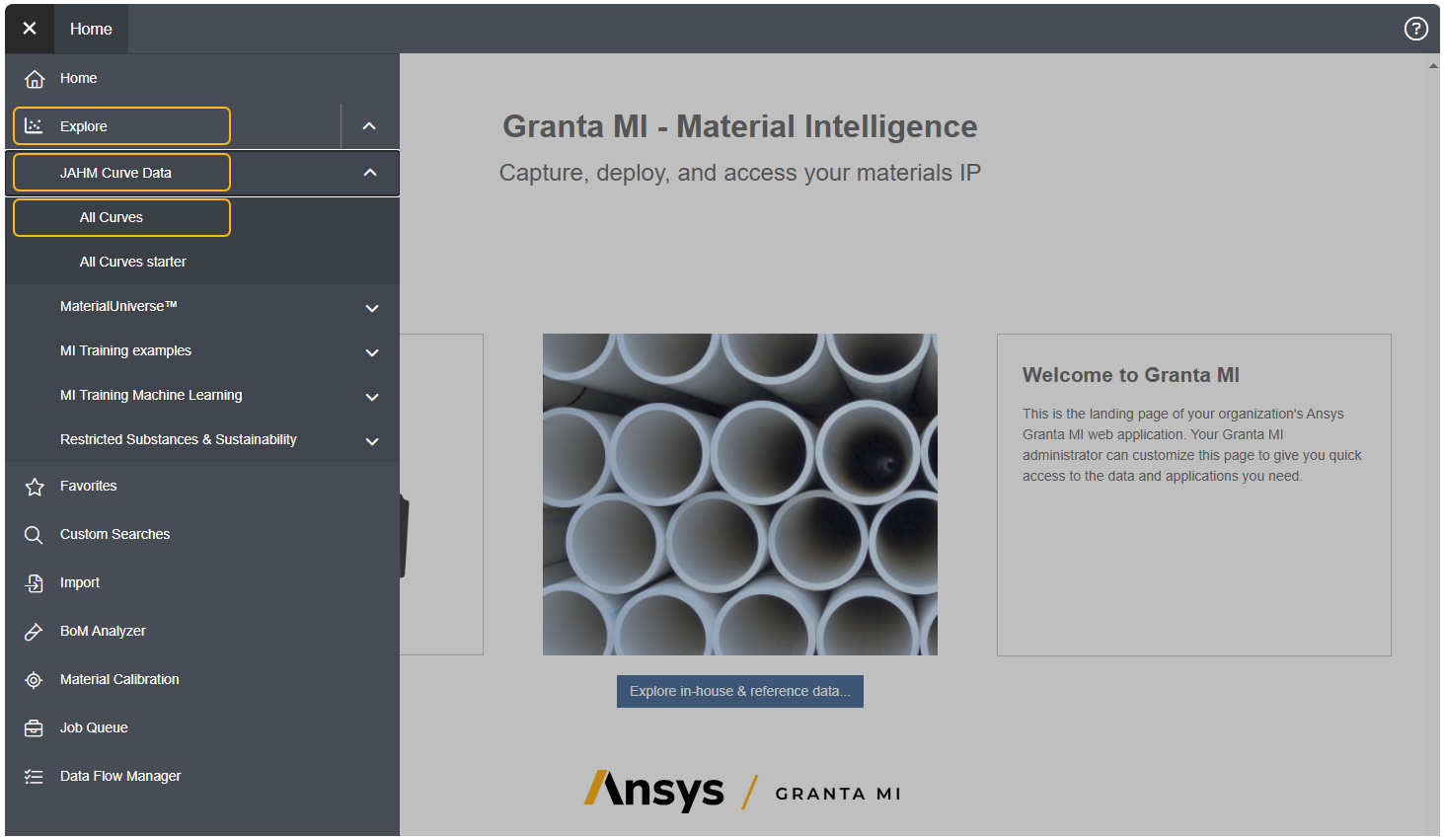
On the left side is a search panel where you enter filter criteria. Under Material information, Material family, choose Metals and alloys. After selecting the check box, hit Escape or click anywhere in the user interface outside of the check box window.
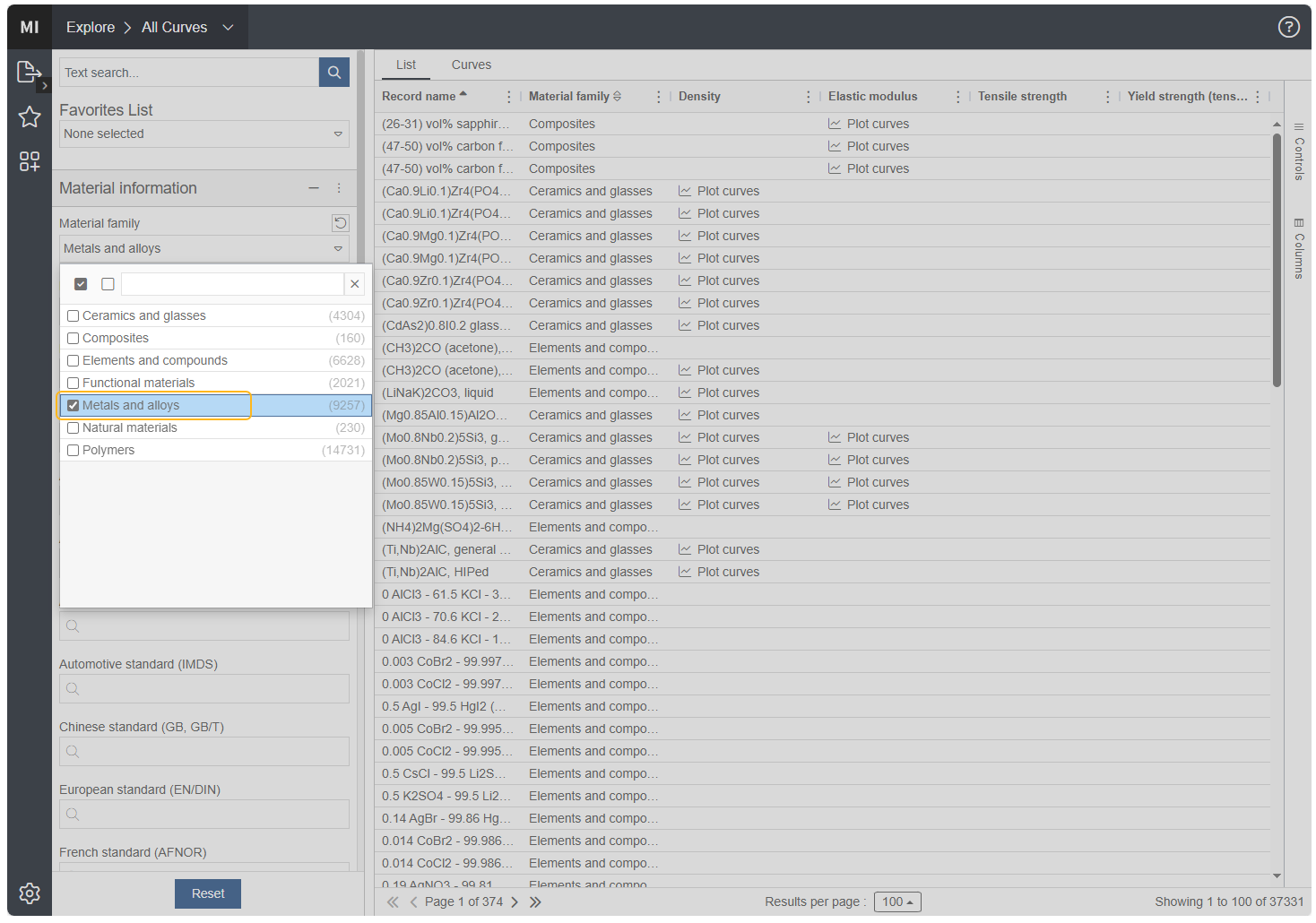
Under Material category, choose Titanium Alloys, followed by Escape.
Under Material, choose Ti - 6Al - 4V.
As you continue to narrow the scope of materials you will see the filter criteria listed at the top of the page. Adjust the column widths as needed to see the information.
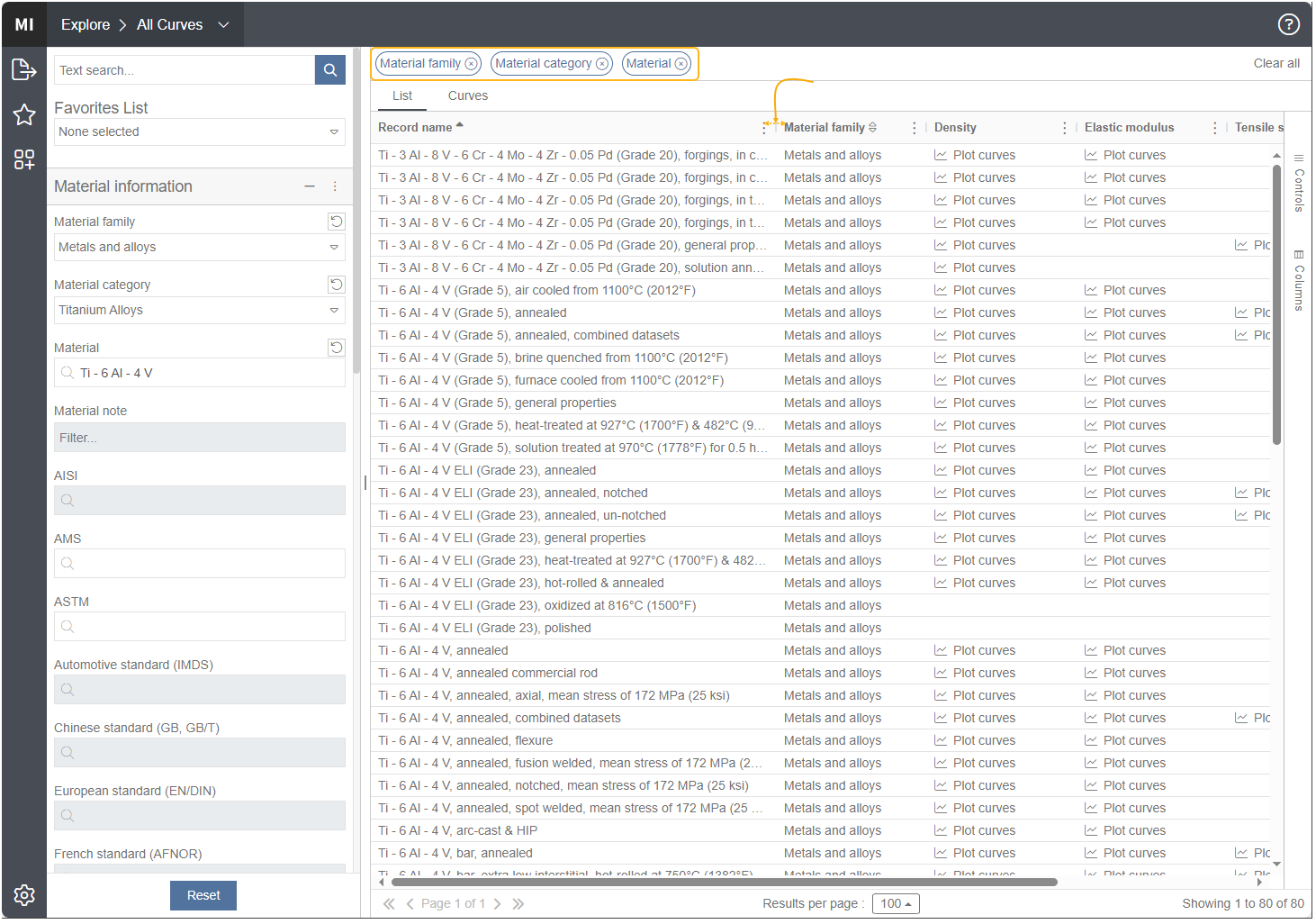
Now we need to narrow the list down to those Ti - 6Al - 4V materials that have density and the properties for the isotropic elasticity model. In the search panel, scroll down to the Physical properties check boxes and choose Density. Under Mechanical properties, choose Elastic modulus, Shear modulus, Bulk modulus, and Poisson's ratio. If you also try to select Yield strength (tension) and/or, under Stress-Strain, True stress-strain (tension), you will see the message: "No matches for this criteria in the current search results." There are no material records that contain all the data. This is because true stress-strain is very dependent on the specific manufacturing and heat treatment processes, as well as on test conditions, such as strain rate, hold time, and so on. To handle this, we will find a second material record later. For now, select only the five properties as shown here.
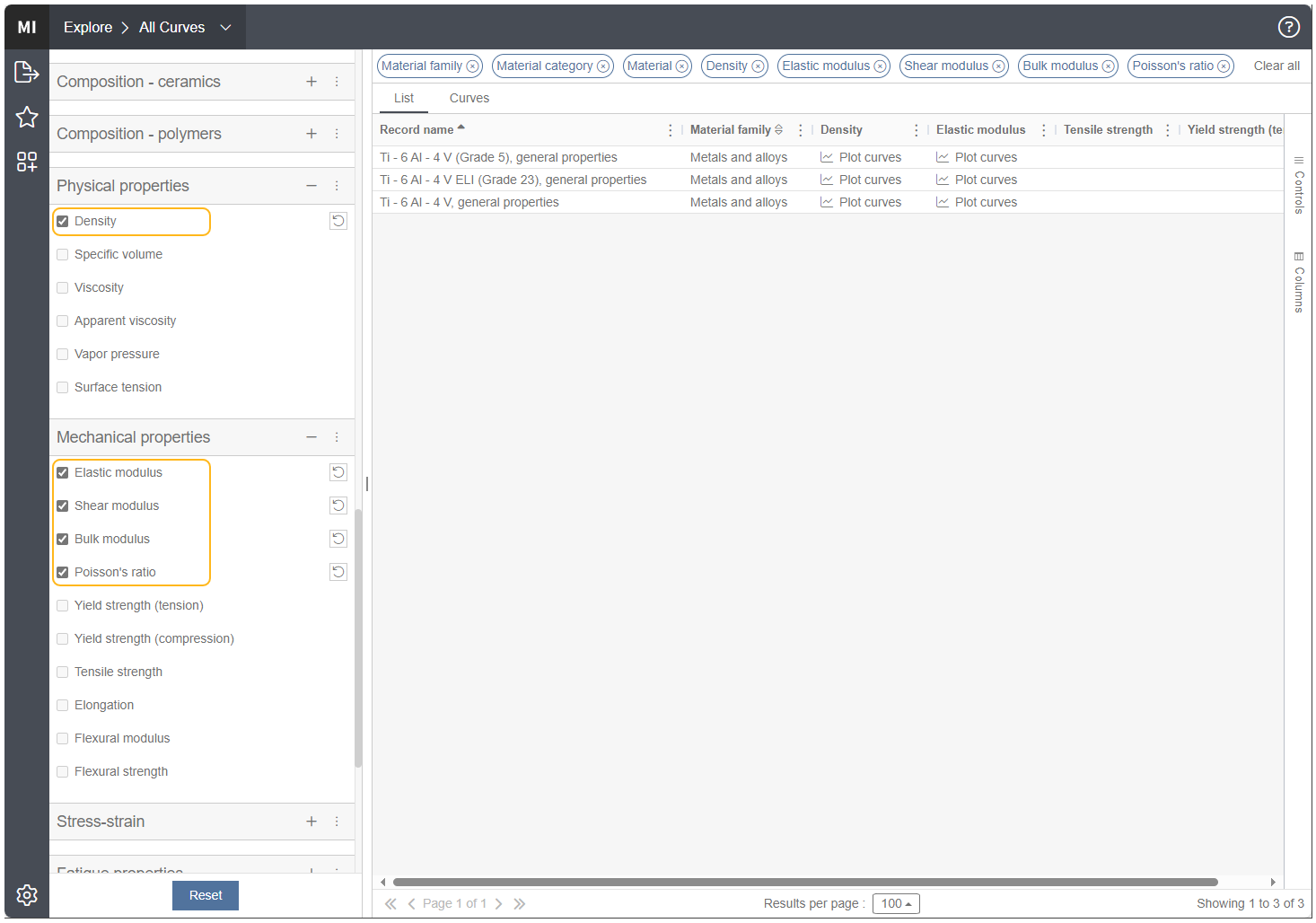
From the search results, we'll choose Ti - 6Al - 4V, general properties. You can view the specific properties, plot curves, and so on by double-clicking the record.
You can change the units system under Preferences, in the lower, left corner of the interface. Be sure to save the material data in Metric or SI units to be consistent with the default units used in Workbench's Engineering Data for AM simulations in Mechanical.
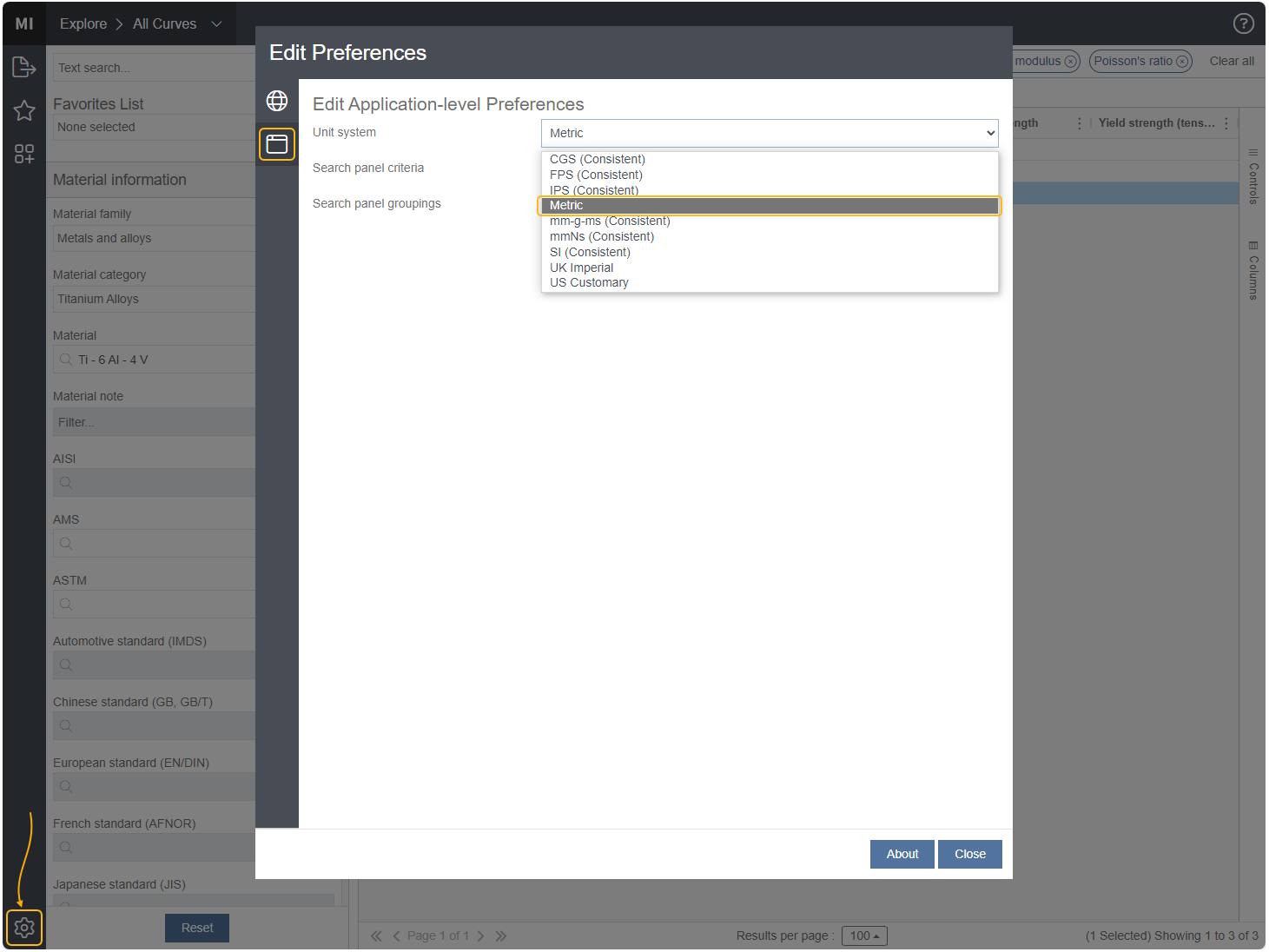
Export material card
A material card is an xml file that contains material data in a format useable by the Engineering Data module. On the left side of the page, click the Export icon, Export Material Cards, to export the Ti - 6Al - 4V, general properties material card.

Under Available packages, choose Ansys Workbench. Under Available exporters, choose Temperature-dependent properties. Then click Run. Save the xml file to a location on your computer.
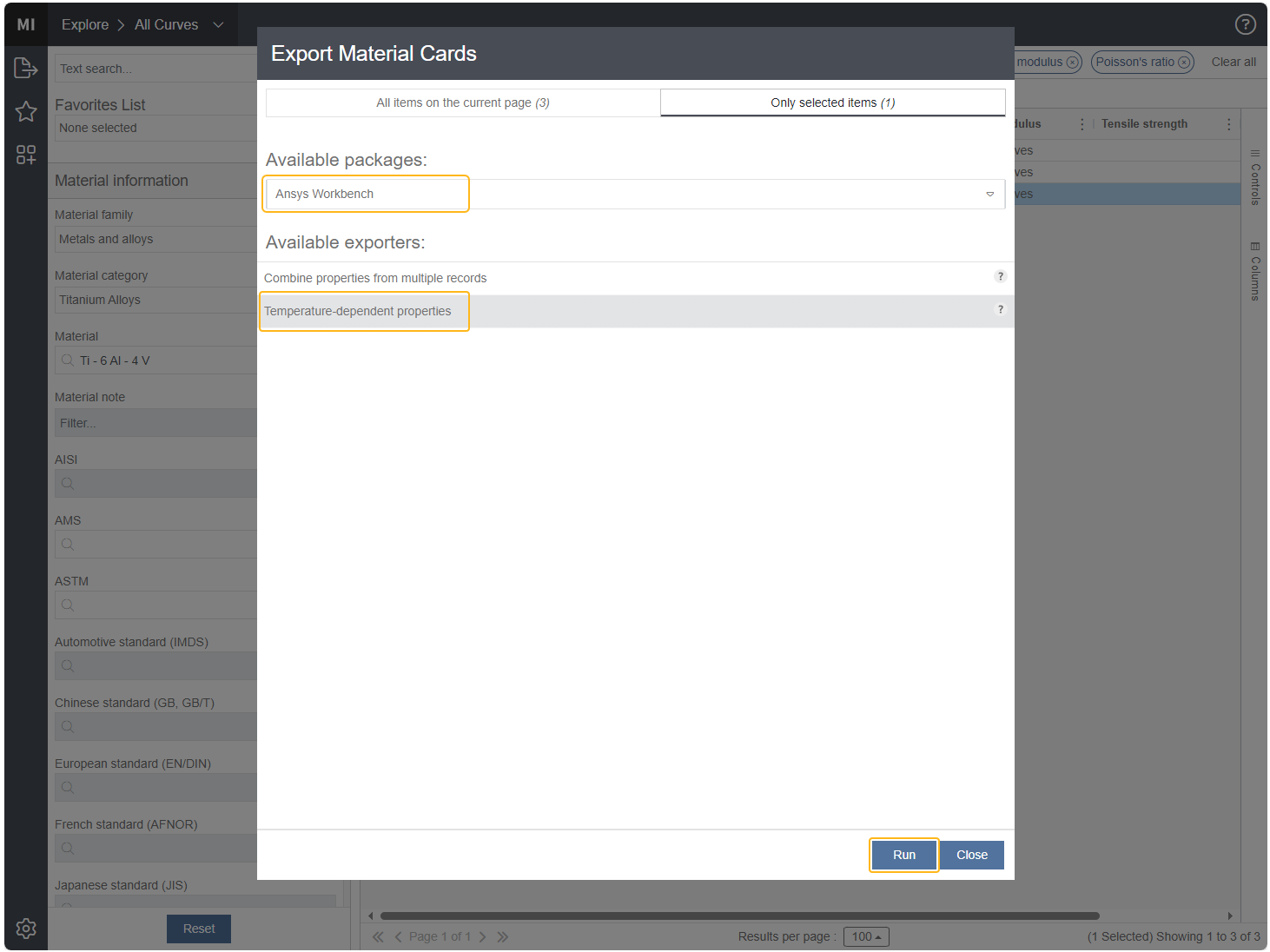
Search for material record for true stress-strain data
Now we need to obtain the information for the plastic portion of the stress-strain curve. Navigate back to the Explore page and click Reset to clear the form. Again search for Metals and alloys, Titanium Alloys, Ti - 6Al - 4V, and this time, scroll down to Stress-Strain and check the box for True stress-strain (tension).
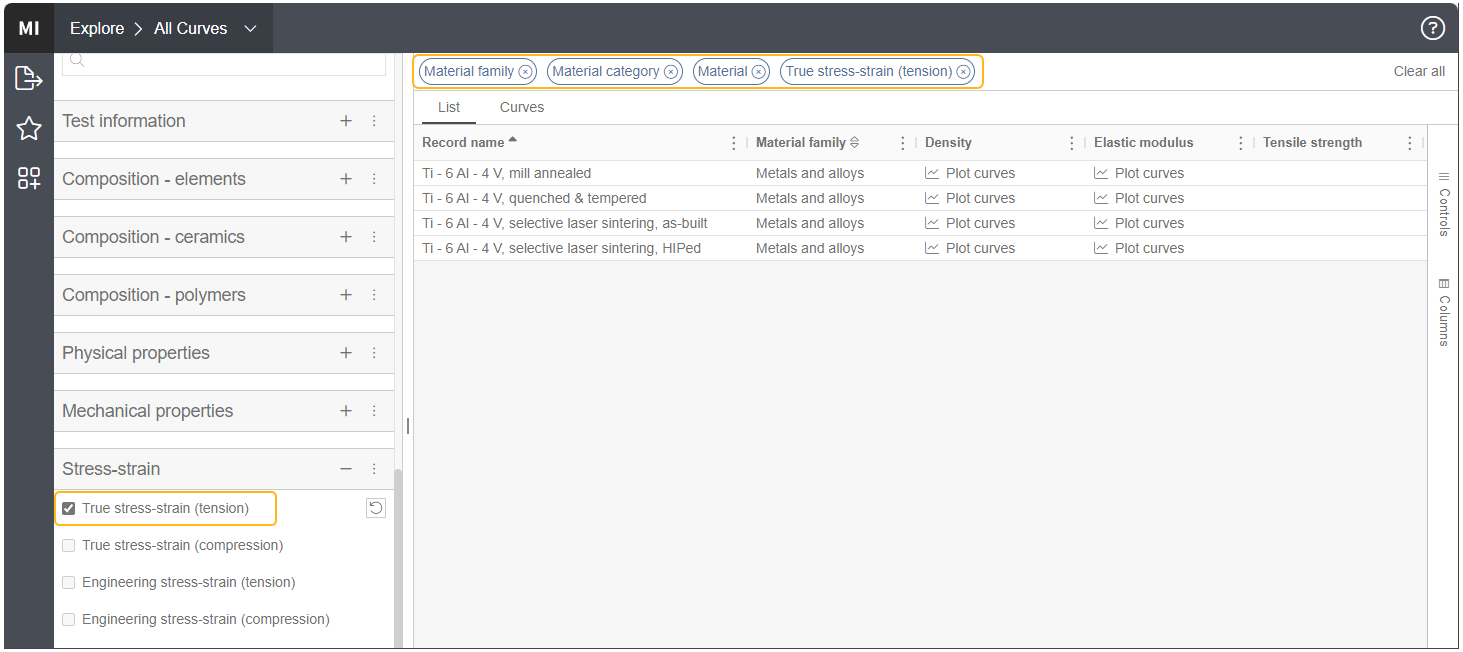
The search results show Ti-6Al-4V material records with various manufacturing processes. Double-click Ti - 6Al - 4V, quenched and tempered. In the right side panel that appears, click the arrows icon to Show full page datasheet.
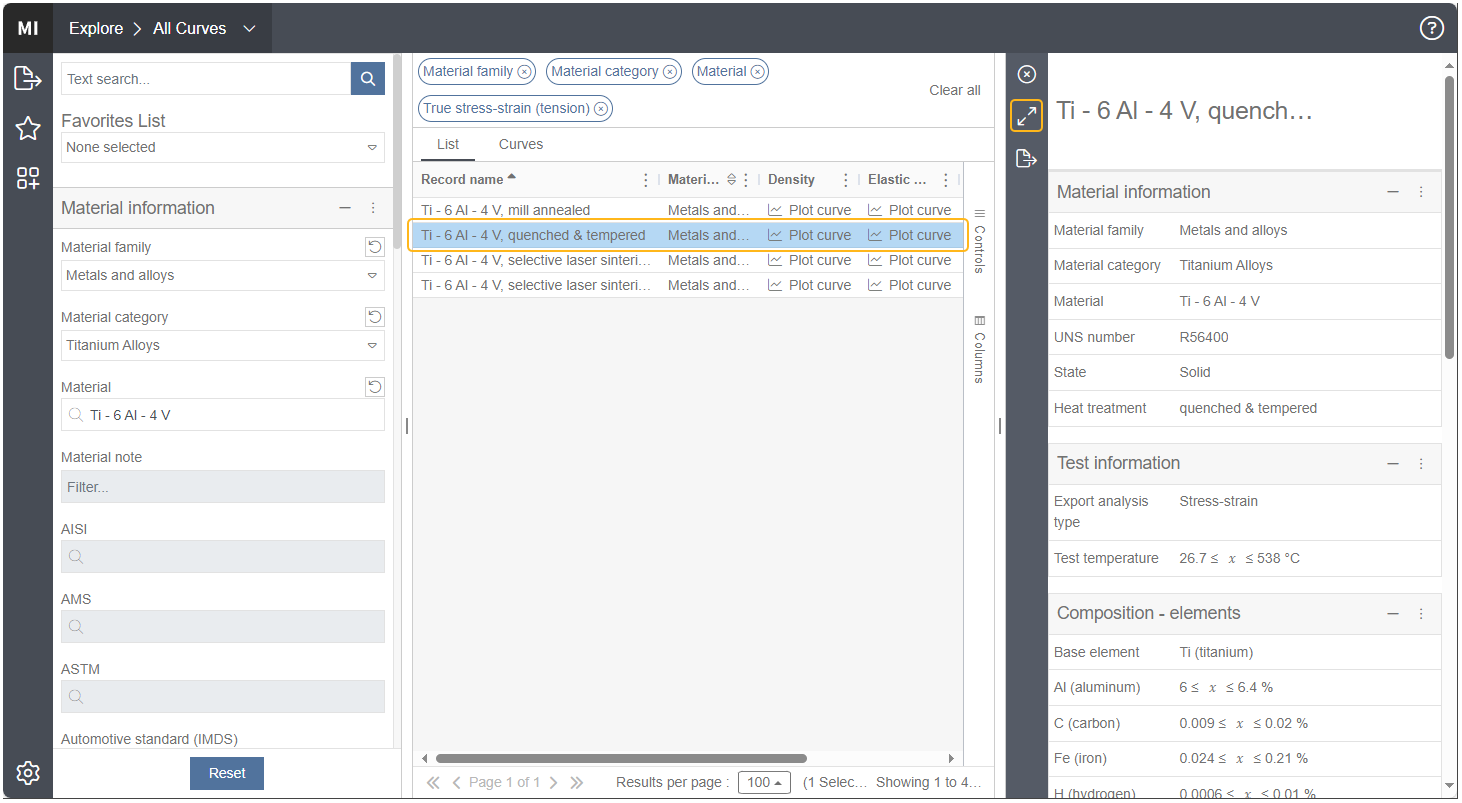
Scroll down to the Stress-strain section and click Plot curves.
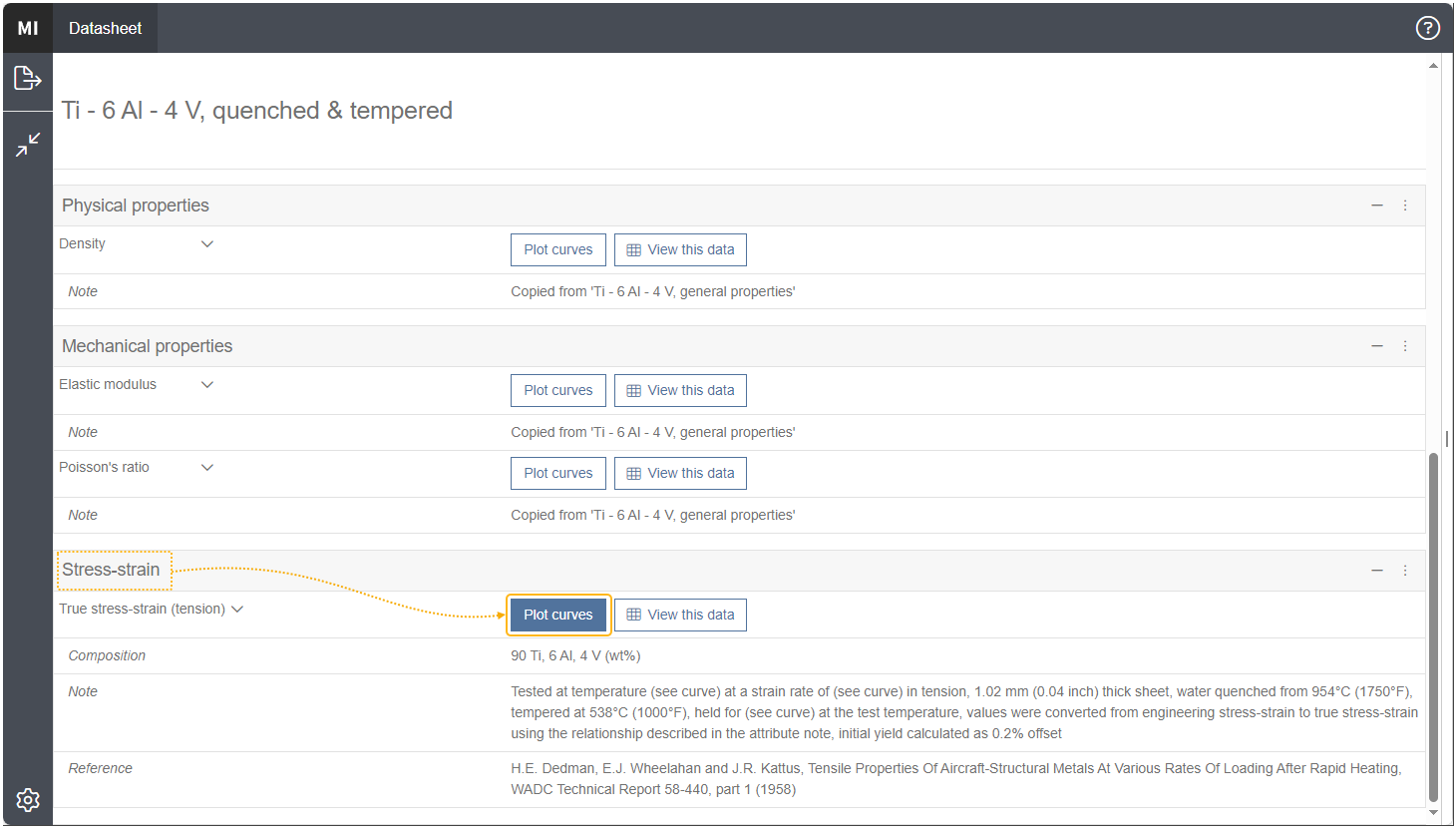
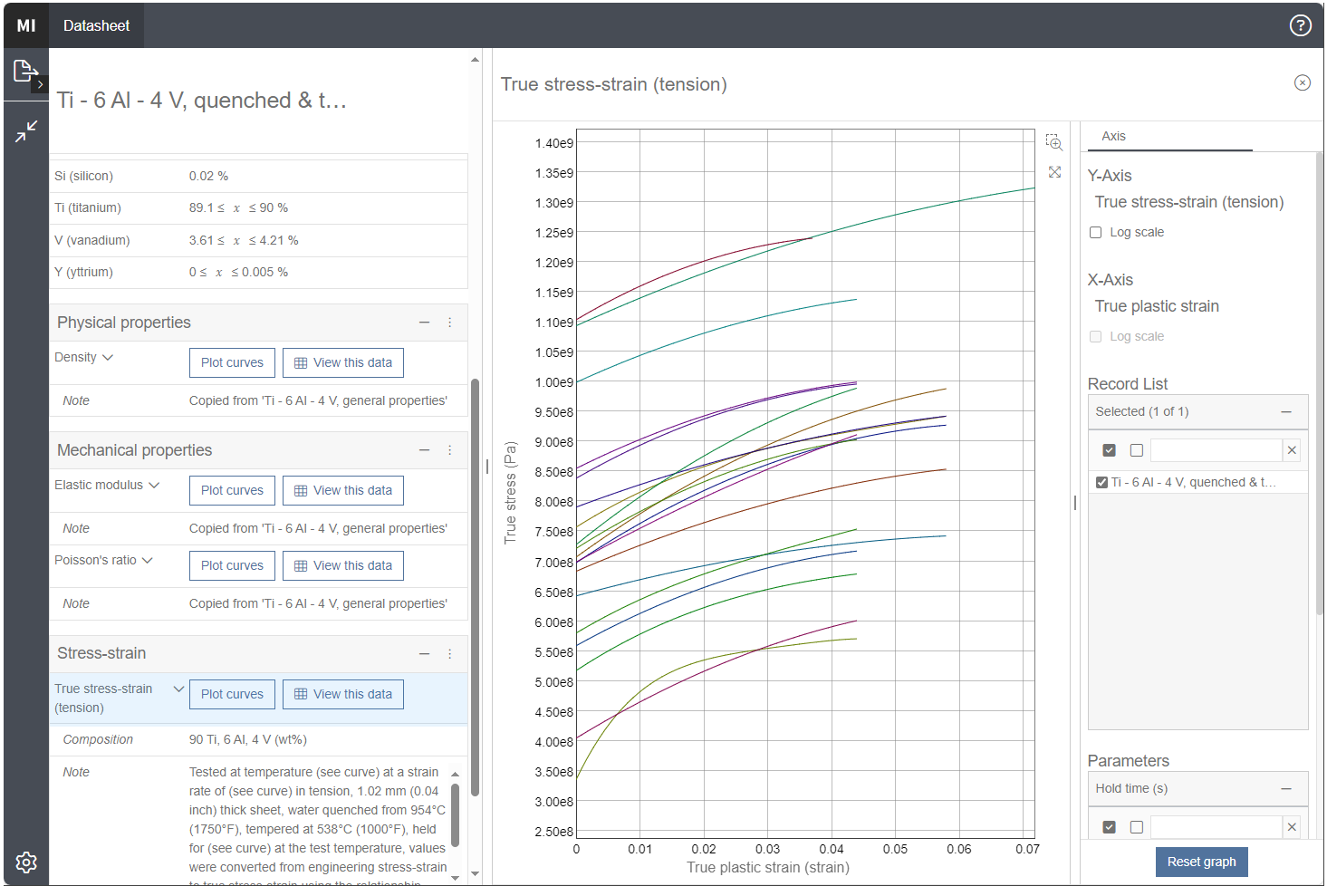
The many curves shown reflect the Ti - 6Al - 4V, quenched and tempered material record with various heat treatment processes and tensile test methods. We will need additional filters to select the conditions we want. We'll choose one that has a fairly slow strain rate and held for a long time. Generally, we would prefer a lower strain rate for a quasi-static tensile testing and a longer hold time for the temperature to homogenize at an elevated testing temperature. You should choose a record that is most appropriate for your situation.
On the right-hand side panel, scroll down to see the parameters of Hold time and Strain rate. Under Hold time, clear the first two check boxes and keep the box checked for 1800 seconds, reflecting a half hour hold time. Under Strain rate, clear the last two check boxes and keep the check box checked for 0.00005 strain/sec. This leaves three stress-strain curves representing three different temperatures, 204.44°C, 315.56°C, and 537.78°C. Hover over each curve to see the details.
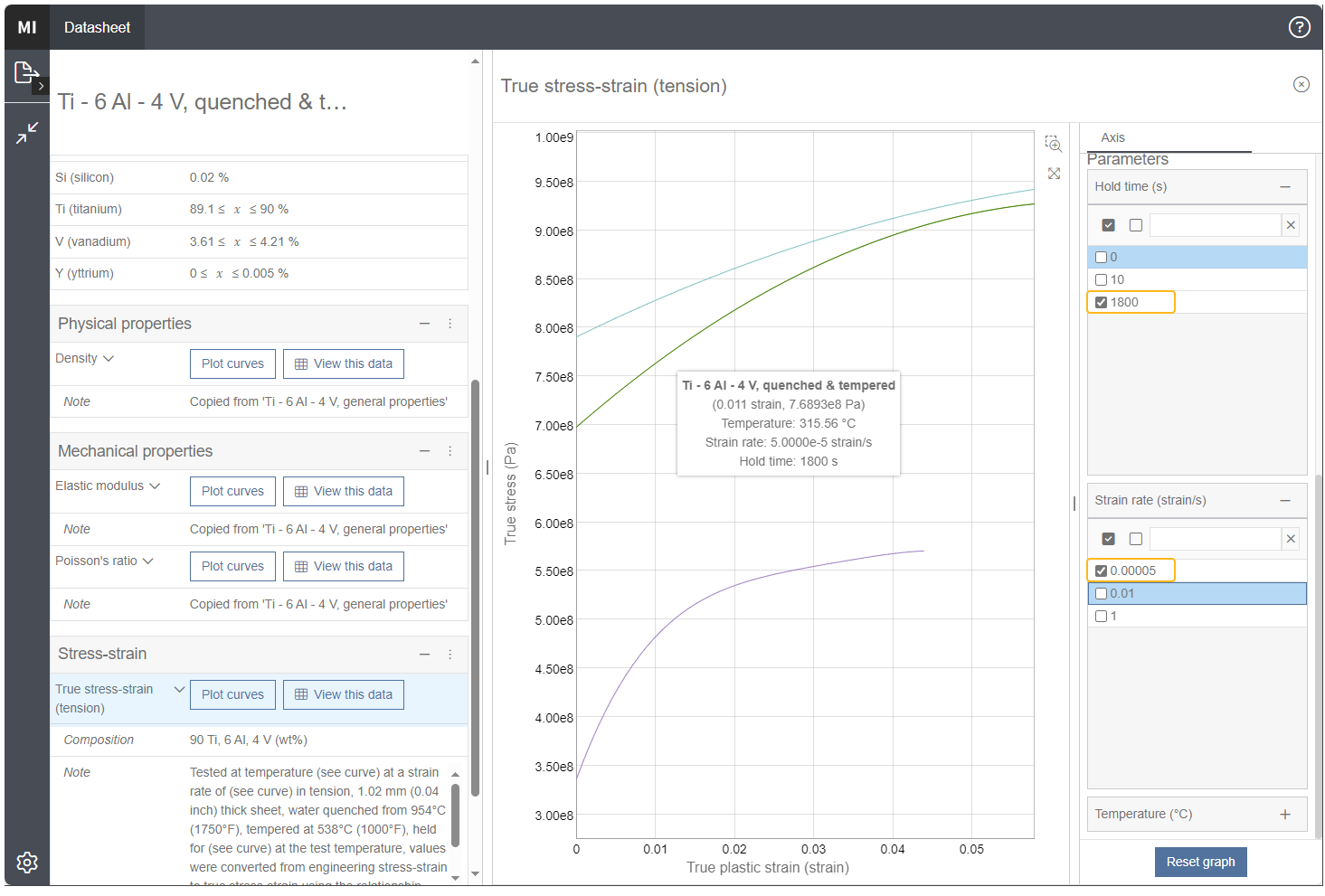
Remember that from the first material card we already have the data for the elastic portion of the material's overall stress-strain curve. By looking at the X-axis (True plastic strain) on these curves, we know the graph shows only the plastic portion of the material's overall stress-strain curve. For each temperature, the yield point is at the start of the curve, or at a true plastic strain = 0. We will calculate the slope of each curve, which is the tangent modulus.
To view the data raw numbers, on the left side panel, under Stress-strain, click View this data. Again, this data is from Ti - 6Al - 4V, quenched and tempered with all the processes and test methods. Collapse the data until you find our desired data for 0.00005 strain rate and 1800 hold time. The data for the three temperature curves corresponding to 315.56°C, 537.78°C, and 204.44°C are in Series 14, 15, and 16, respectively. This is the data we must extract.
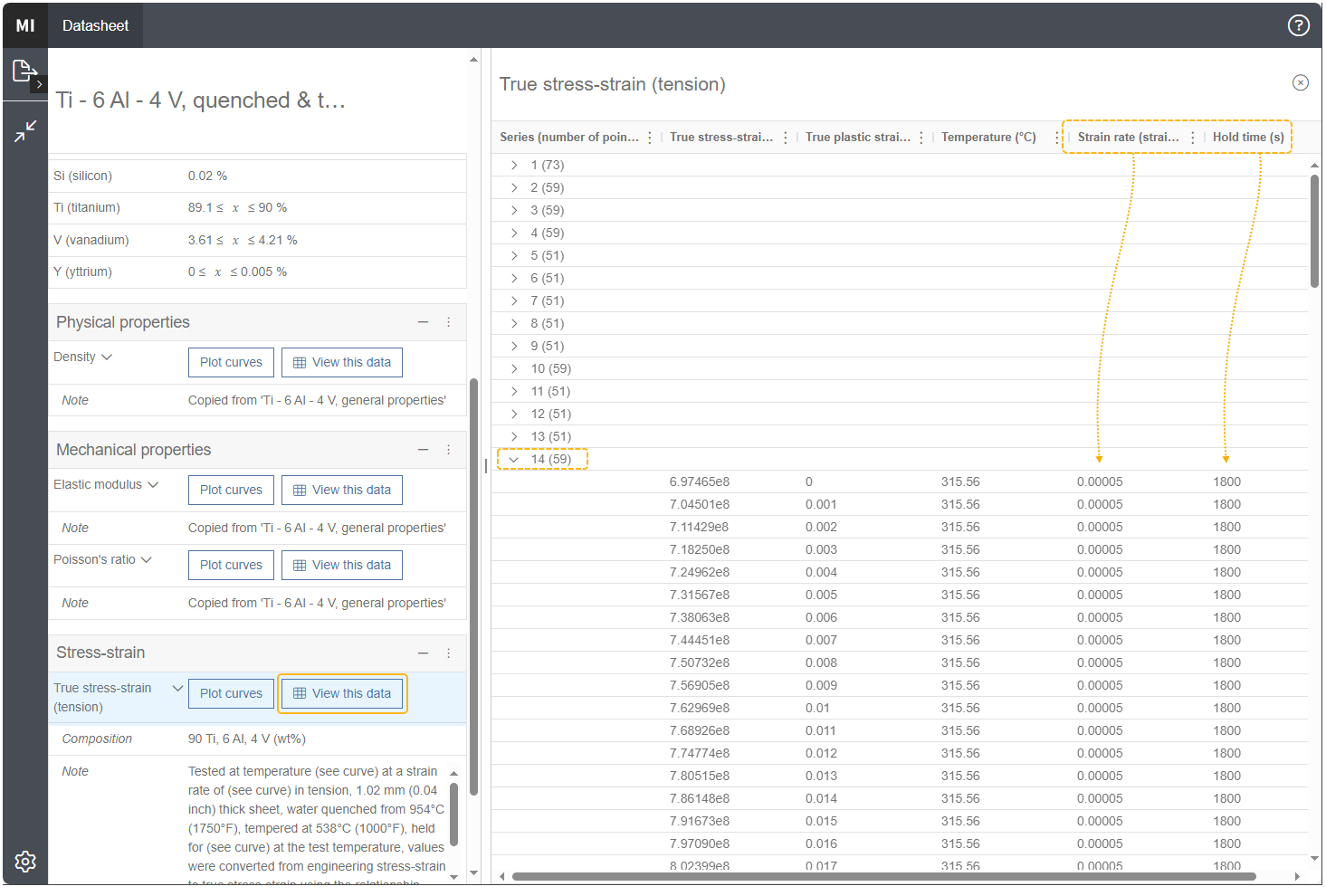
Save the true stress-strain curve data
On the left side of the interface, click the Export icon and then Export to Excel to save the data. On the next page, after the export is completed, click Download exported data. It is saved as Ti - 6AI - 4V, quenched and tempered.xlsx.
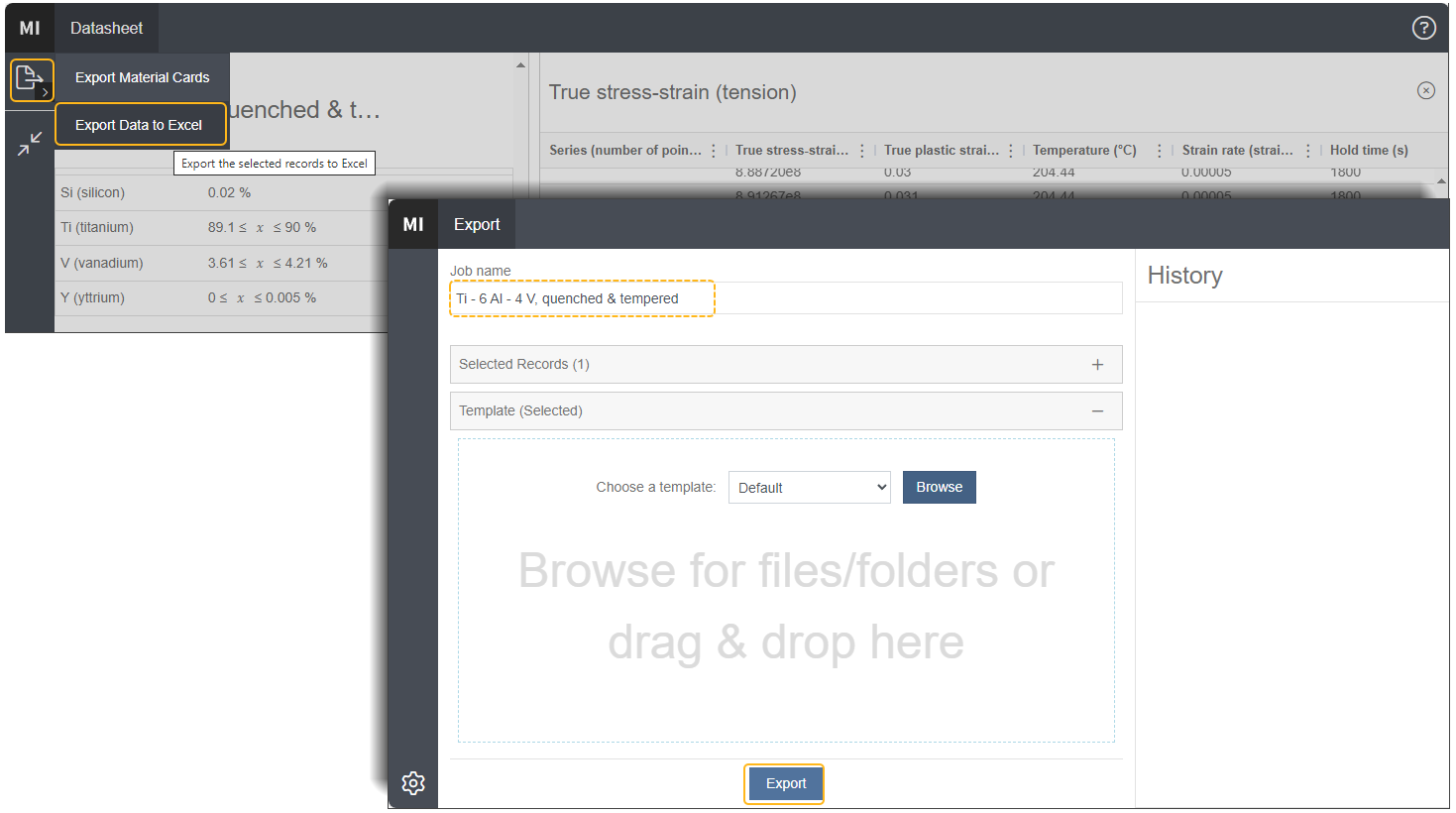
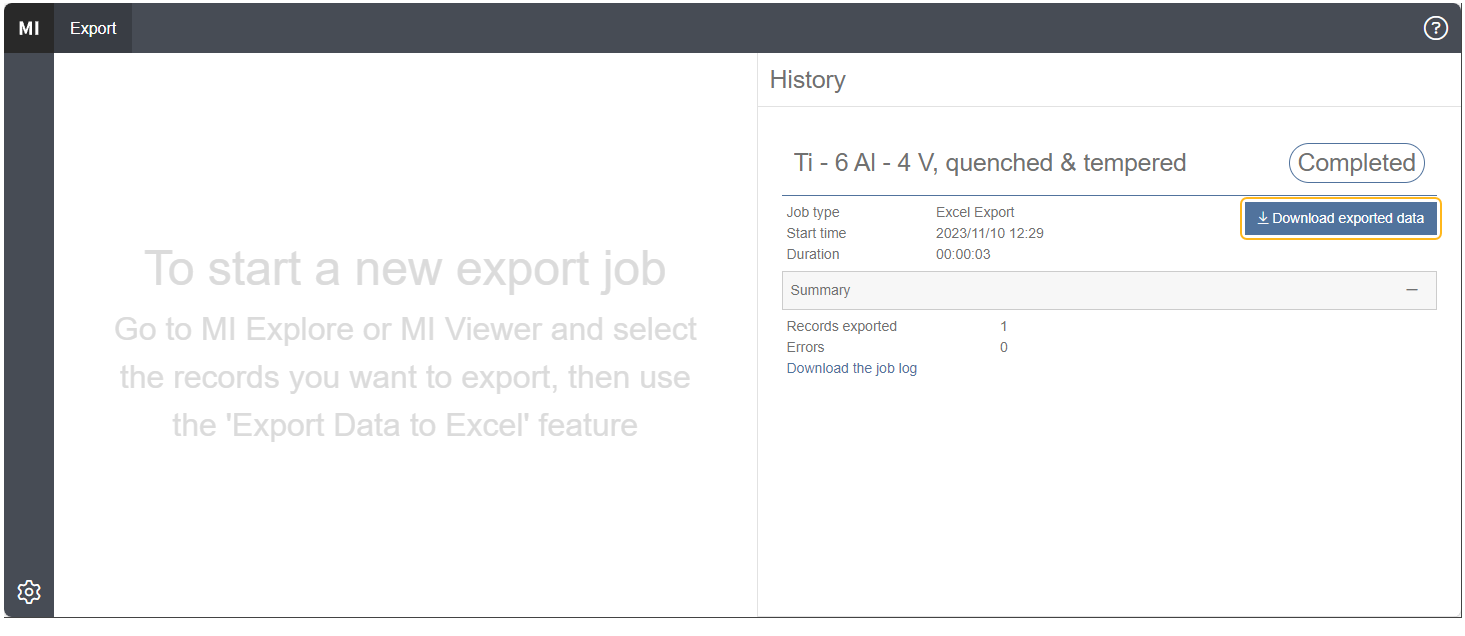
Use a spreadsheet to derive data for Bilinear Isotropic Hardening model
Open the Ti - 6 Al - 4 V, quenched & tempered.xlsx file. At the bottom of the page, navigate to the sheet called Truestress-s_ain(tension).
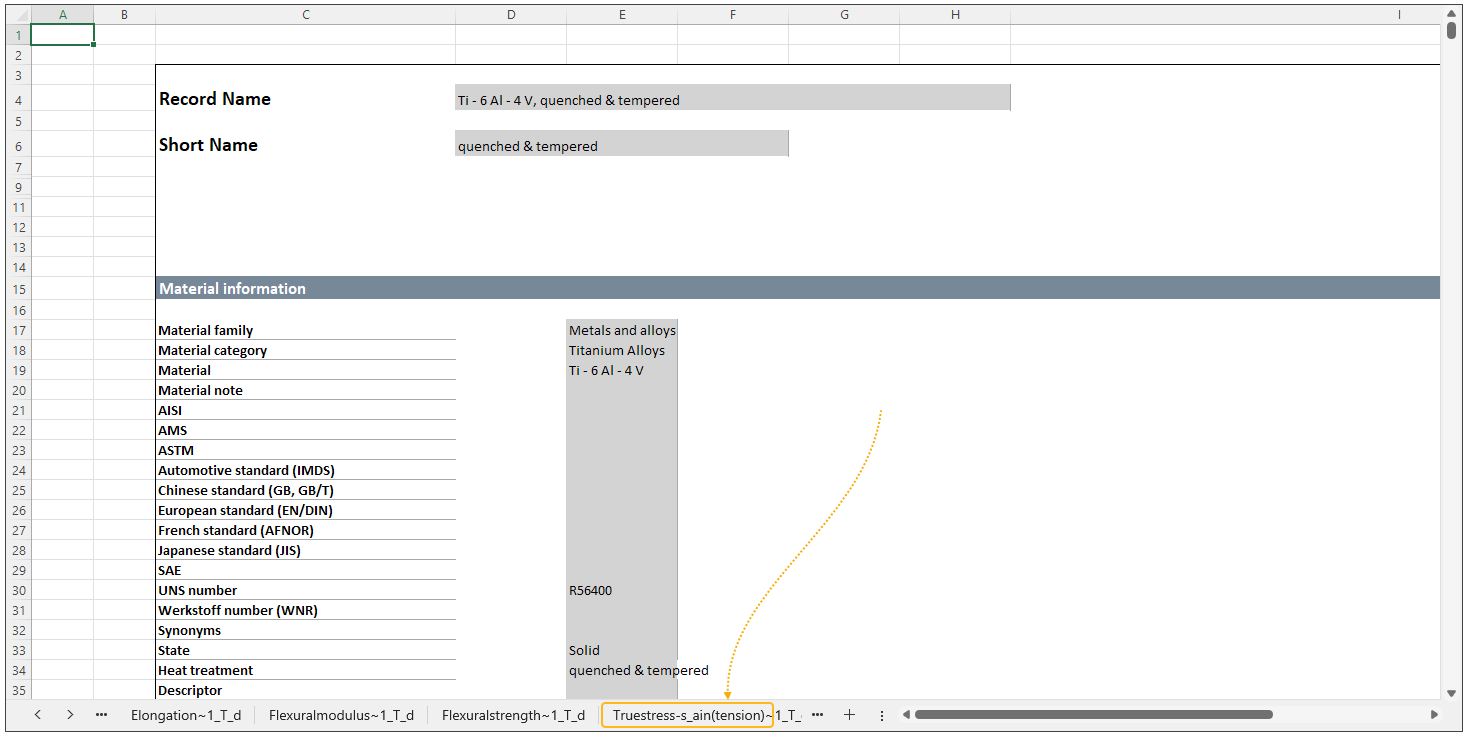
Scroll to the right to find the data in series 14: Temperature = 315.56°C, Hold time = 0.5 hr, and Strain rate = 0.00005 strain/s. Continue to scroll to the right to see the data in series 15: Temperature = 537.78°C, and in series 16: Temperature = 204.44°C.
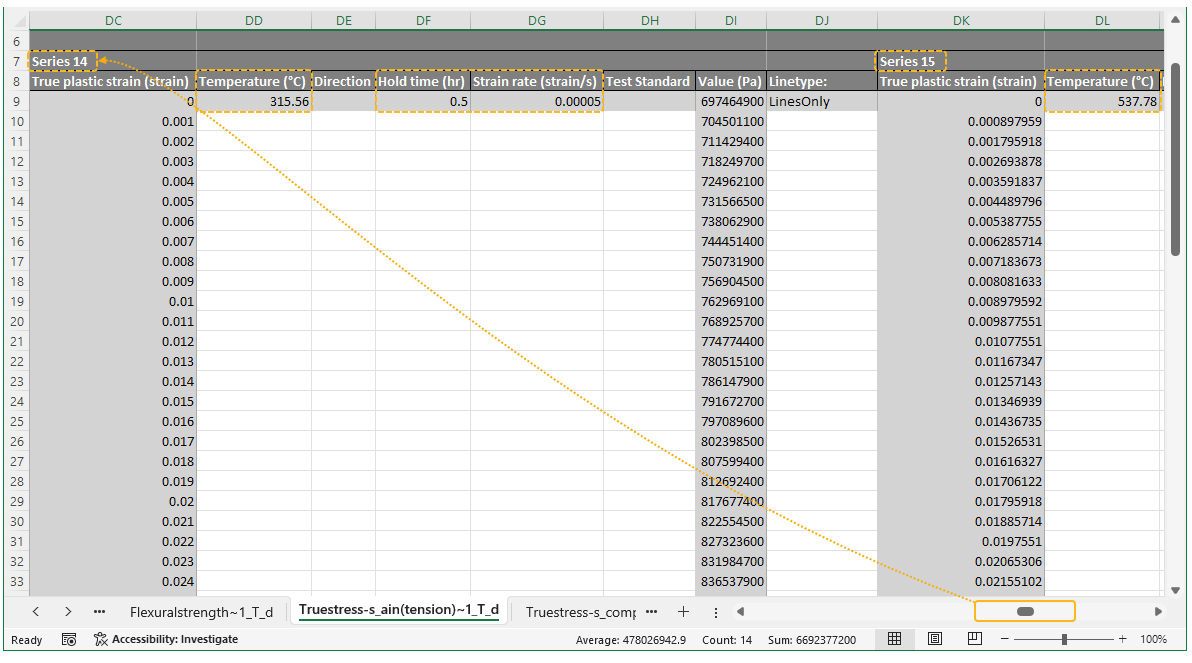
For each temperature, the true stress value at true plastic strain = 0 indicates the Yield Strength. We will enter these values into Engineering Data later.
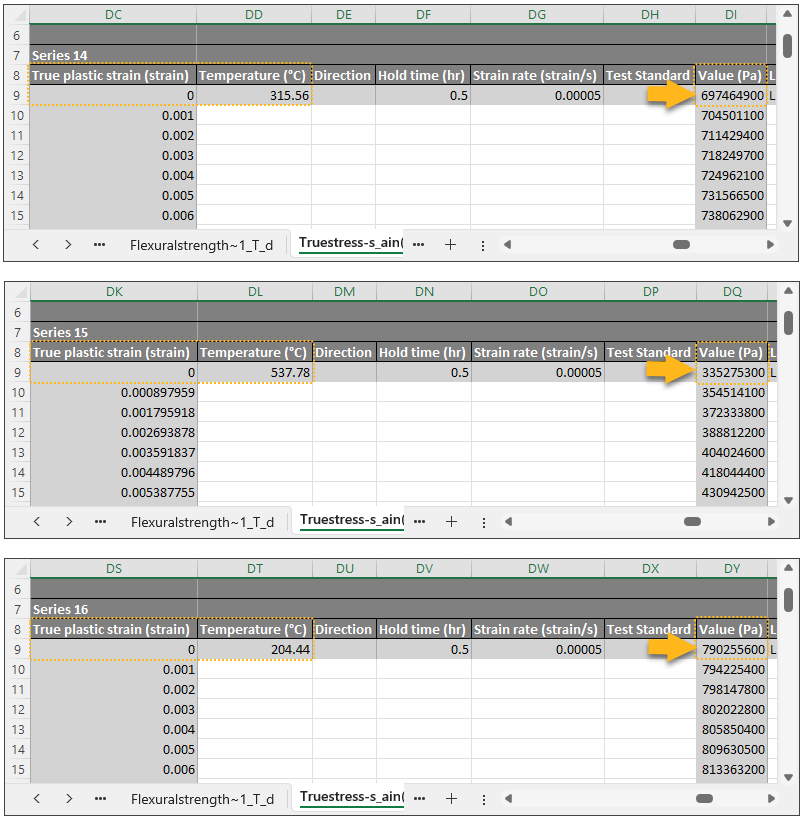
For simplicity, we assume the tangent modulus is the slope of the true plastic stress-strain curve. For full documentation on how to calculate the tangent modulus, refer to Bilinear Isotropic Hardening.
or
Calculate that in the spreadsheet using a formula as follows:
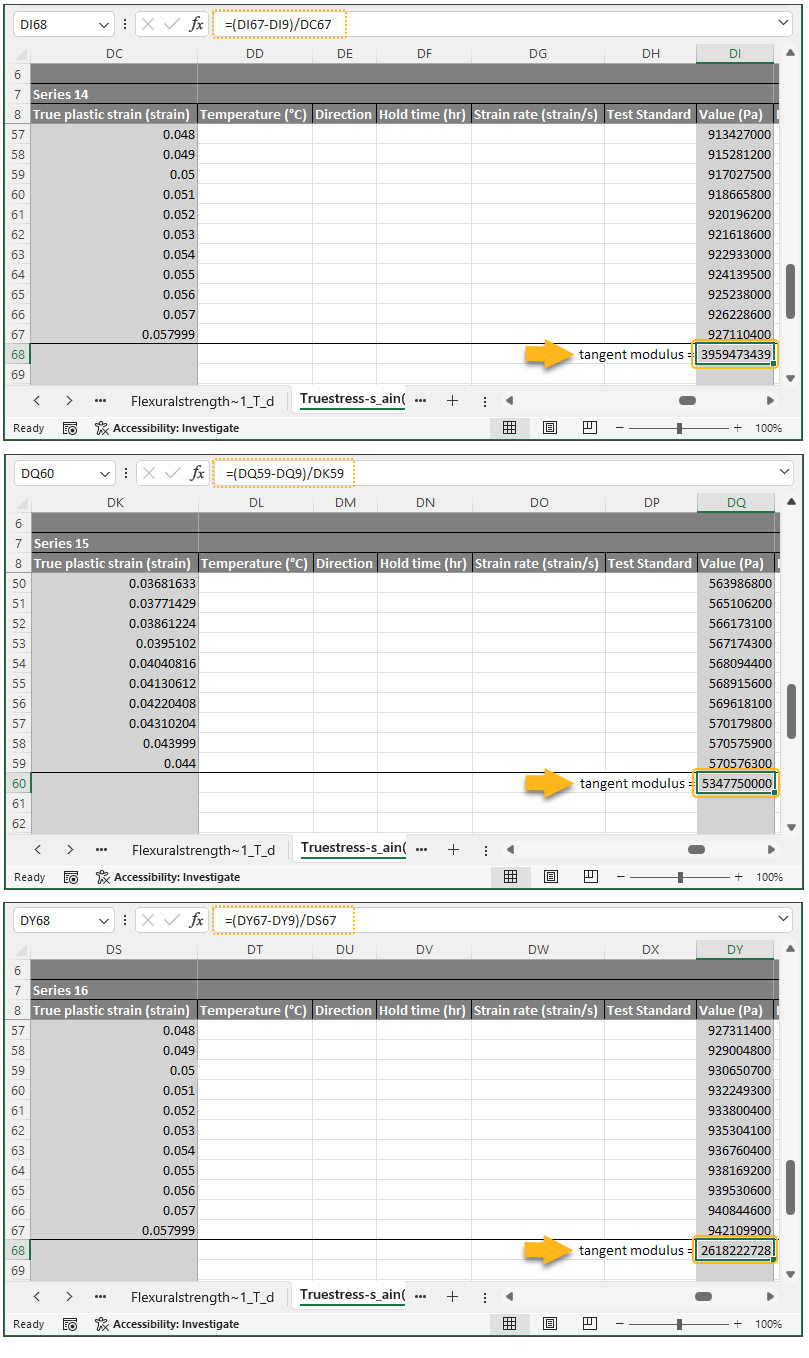
The Tangent Modulus for each temperature curve is highlighted. The following tables summarizes our results.
Series # in spreadsheet | Temperature °C | Yield Strength (Pa) | Tangent Modulus (Pa) |
---|---|---|---|
16 | 204.44 | 790255600 | 2618222728 |
14 | 315.56 | 697464900 | 3959473439 |
15 | 537.78 | 335275300 | 5347750000 |
These values will be entered into Engineering Data in the next step. The Yield Strength and Tangent Modulus together comprise the data for the Bilinear Isotropic Hardening model.
Open Workbench, and add an additive analysis system as you normally do to begin a simulation. Here we added an AM LPBF Thermal-Structural system. Double-click Engineering Data to open it.
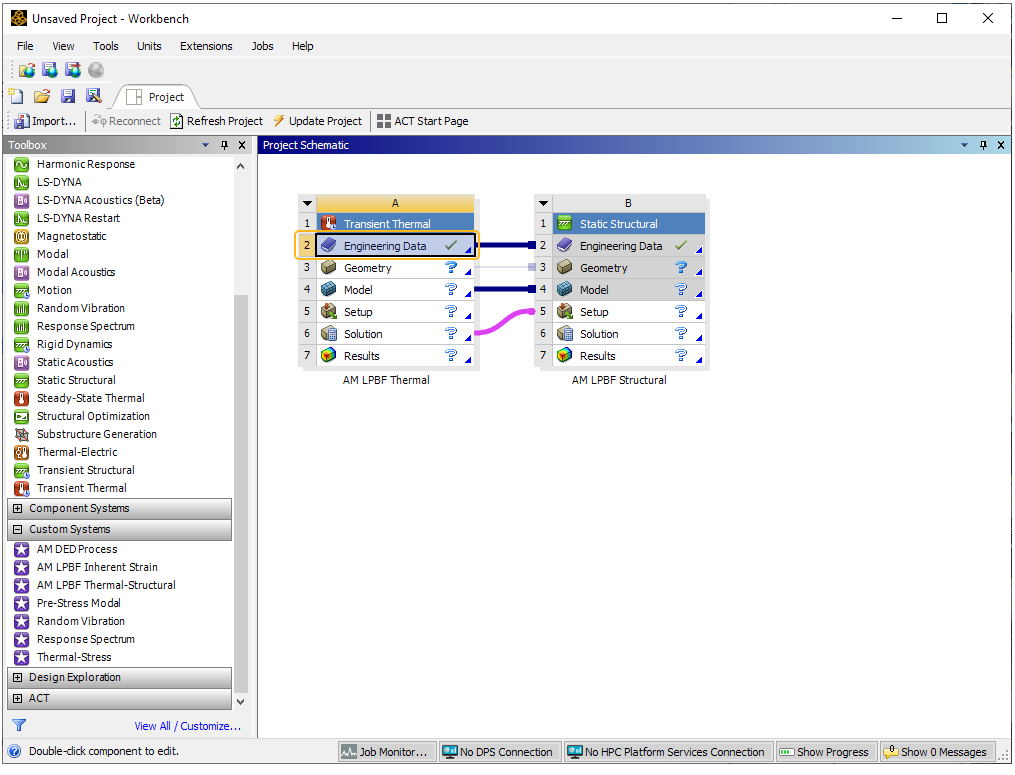
Import general properties material card
Click Engineering Data Sources and scroll down to the
button to add an existing data
source from a file. Navigate to your saved Ti - 6Al - 4V general properties xml file and click
Open.
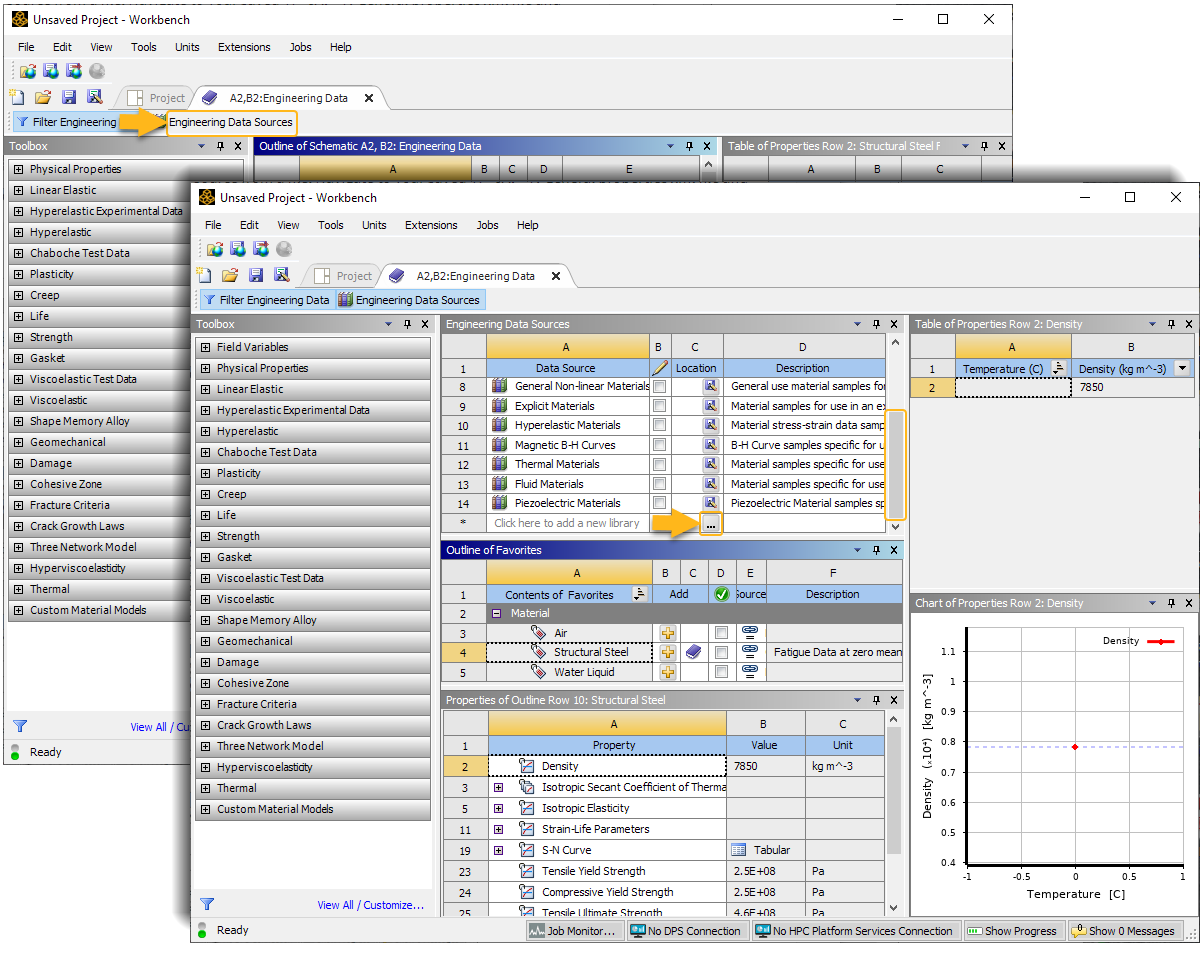
Click the check box in column B
to edit the material.
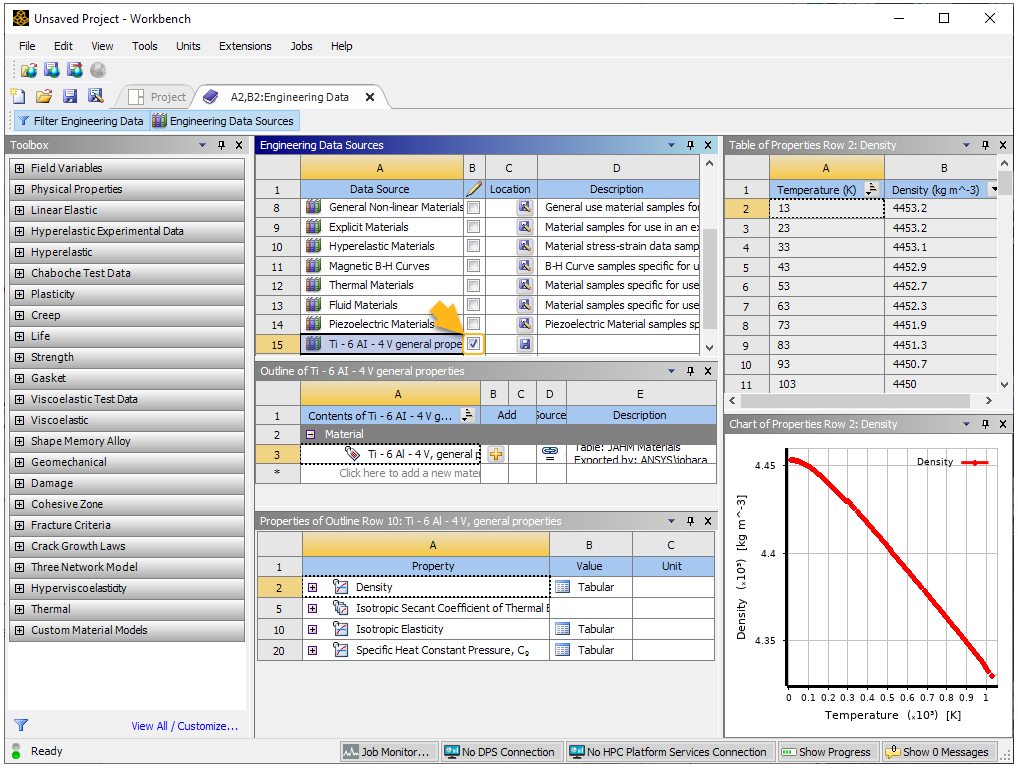
A review of the properties reveals that Melting Temperature and a Bilinear Isotropic Hardening model are missing.
Add missing properties
To add the missing Melting Temperature, in the Toolbox on the left side panel, open Physical Properties and double-click Melting Temperature. This adds the property to the material being edited and shows a yellow highlight for the missing value. Enter 1605 in the highlighted area next to Melting Temperature. The value of 1605°C is the Melting Temperature from the Ansys Ti-6Al-4V sample material.
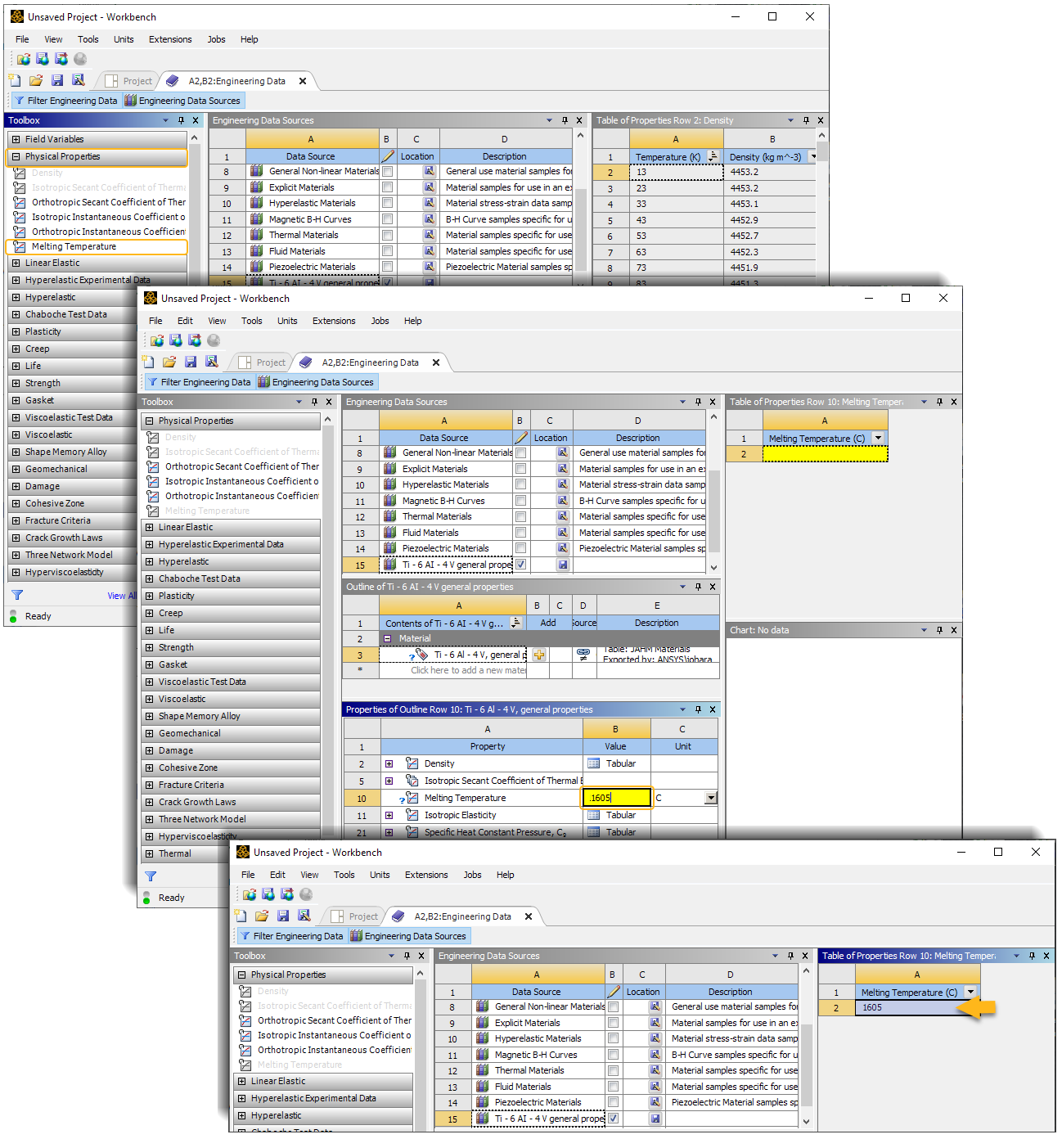
Do the same to add the Bilinear Isotropic Hardening model from the Plasticity options in the Toolbox panel. Next to the highlighted input fields, be sure to use the appropriate units; in our example we are using Pascals for both Yield Strength and Tangent Modulus.
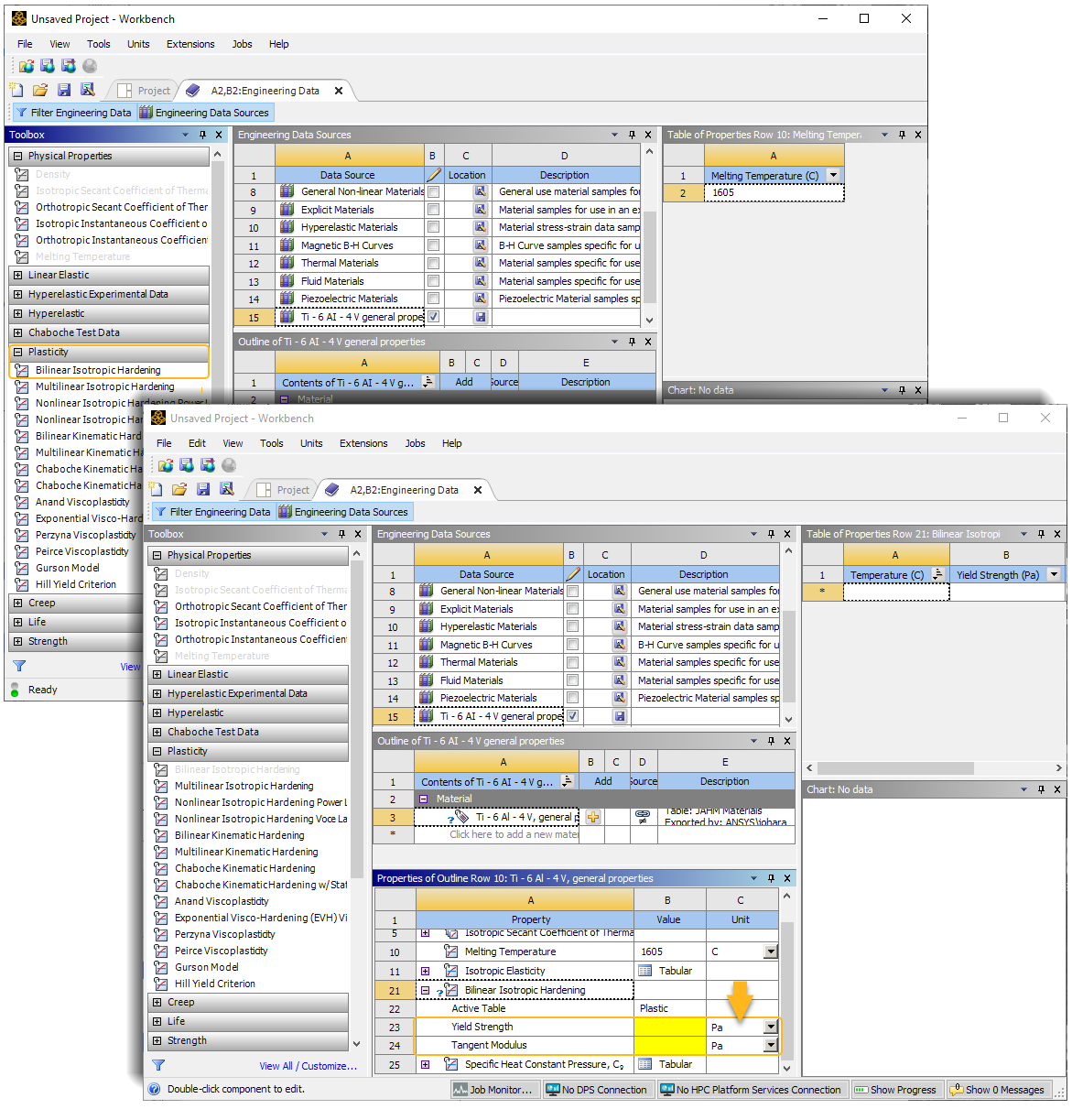
Double-click either highlighted field and then, in the upper right table, enter the values for Temperature, Yield Strength, and Tangent Modulus that you calculated from the spreadsheet.
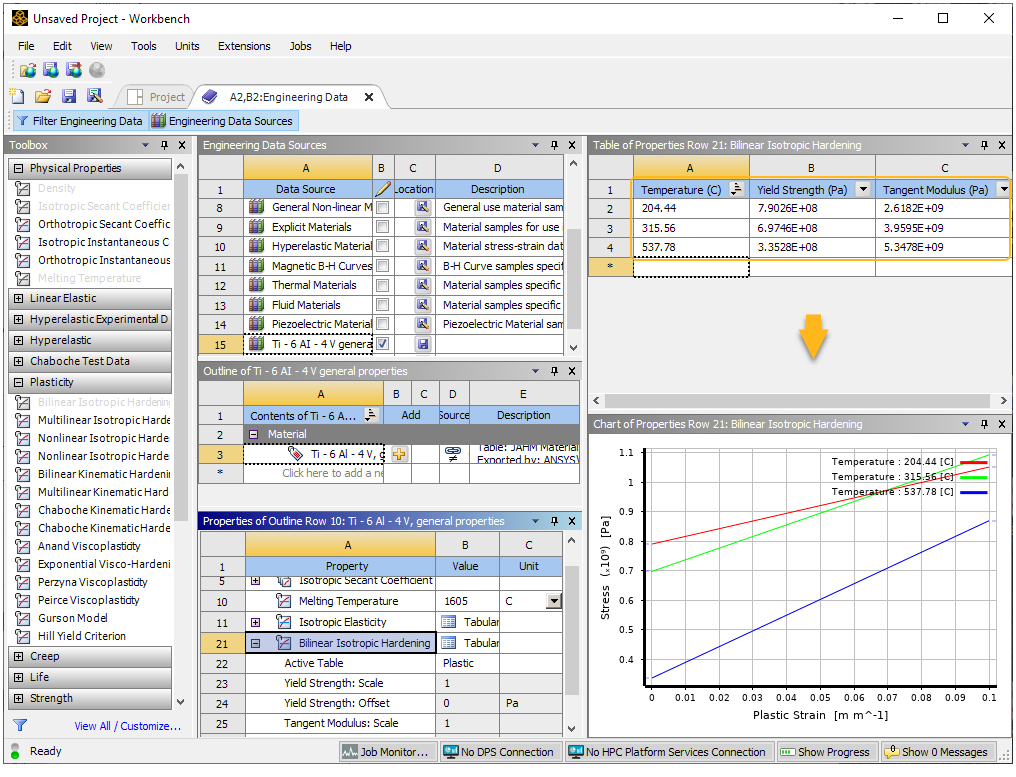
Rename and save the new material in Engineering Data
Now that all the missing data has been entered, the new material is complete and must be saved in Engineering Data for future use. First rename the material. In the Engineering Data Sources panel, click the material name field and enter a new name. We used Ti-6Al-4V JAHM.
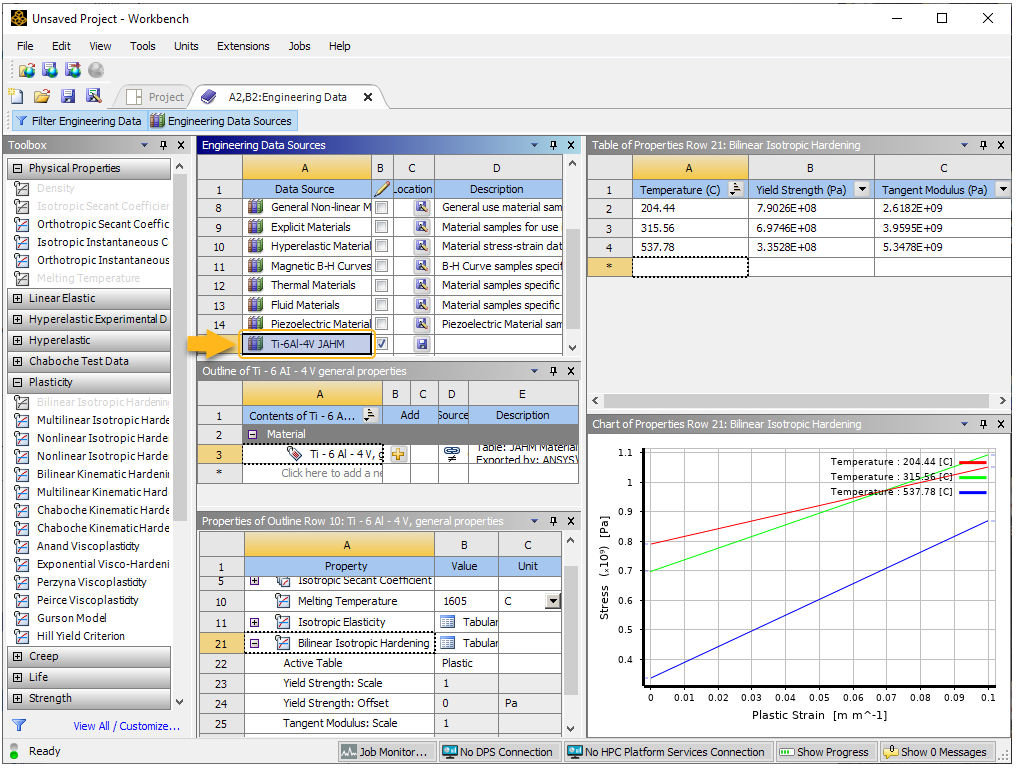
Clear the check box that allows editing of data and you will be prompted to save the material. Click Yes. The new material is saved in Engineering Data and to your original xml file.
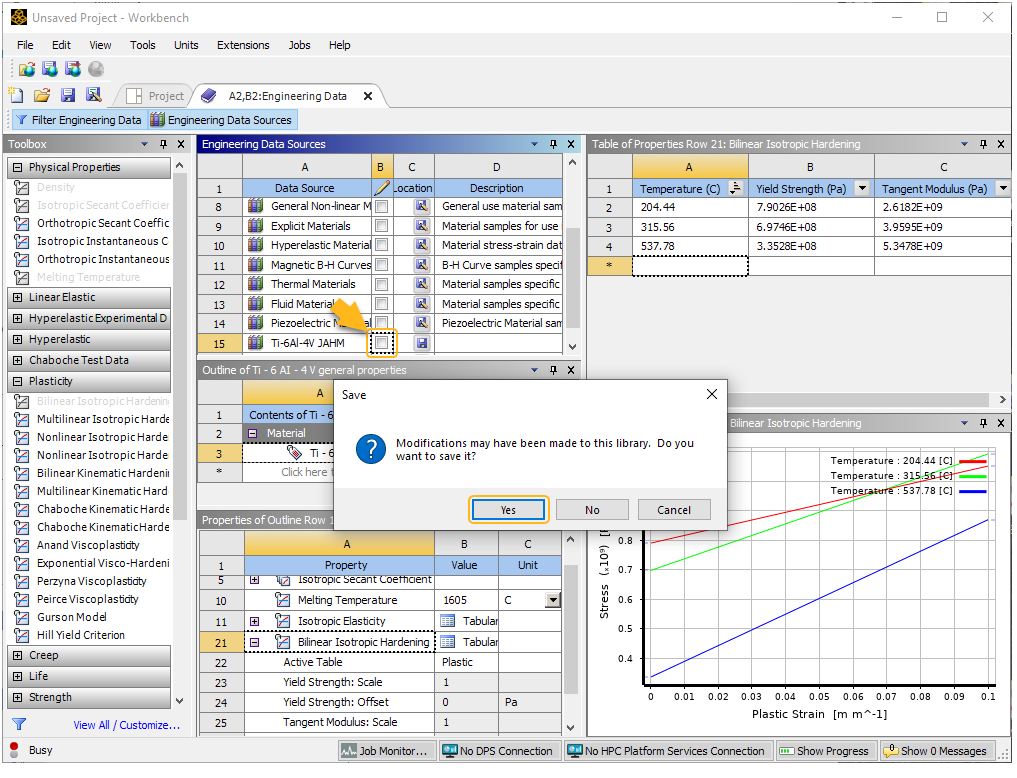
Any time you want to use the material in a simulation, you must first add it to the
project in Workbench's Engineering Data. Navigate to the new JAHM material in Engineering Data
Sources and click the plus icon . The
book icon
indicates it has been added
to the current project.
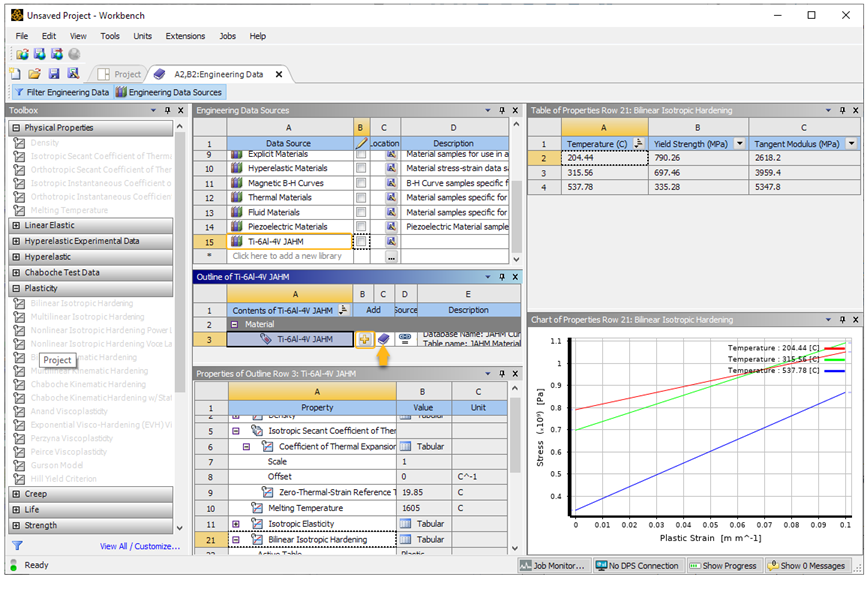
Work through the simulation as usual and then assign the new material for the appropriate geometry bodies.