As discussed in Introduction, the general form for the viscosity can be written as the product of functions of shear rate and
temperature. There are actually three ways in which this relationship can be
expressed:
(6–18) |
(6–19) |
(6–20) |
where and
represent the shear-rate and temperature dependence of the
viscosity, respectively.
In Equation 6–18, the
temperature scales the viscosity so there is only a vertical shift on the model
curves vs. temperature. Four of the temperature-dependent viscosity
laws follow this format:
Arrhenius approximate law
Arrhenius law
Fulcher law
WLF law
In Equation 6–19, the
time-temperature equivalence is introduced by also scaling the shear rate by
temperature. Therefore, there is a horizontal shift in addition to the vertical
shift on the model curves vs. temperature. Three of the temperature-dependent viscosity
laws follow this format:
Arrhenius approximate shear-stress law
Arrhenius shear-stress law
WLF shear-stress law
The final form of the viscosity definition, Equation 6–20, corresponds to the mixed-dependence law.
By default, there is no temperature dependence of the viscosity (that is,
).
The Arrhenius law is given as
(6–21) |
where is the ratio of the activation energy to the perfect gas
constant and
is a reference temperature for which
. The temperature shift
must be specified when a non-absolute temperature scale is
used. It corresponds to the lowest temperature that is thermodynamically
acceptable, given with respect to the current temperature scale. Typically, if
you use Kelvin as the temperature unit,
. If you use Celsius,
.
The units for the parameters and their names in the Ansys Polymat interface are as follows:
Parameter | Name in Ansys Polymat | Mass | Length | Time | Temperature |
---|---|---|---|---|---|
| alfa | – | – | – | 1 |
| talfa | – | – | – | 1 |
| t0 | – | – | – | 1 |
Important: Note that for the Arrhenius model is not the
same as
for the approximate Arrhenius law; they have different
units.
By default, ,
, and
are equal to 0. Figure 6.14: Arrhenius Law for Viscosity shows a plot of
for the Arrhenius law.
The approximate Arrhenius law is obtained as the first-order Taylor expansion of the Arrhenius law (Equation 6–21):
(6–22) |
where is the first-order coefficient of the Taylor expansion and
is a reference temperature. The behavior described by Equation 6–22 is similar
to that described by Equation 6–21 in the neighborhood of
. Equation 6–22 is valid as long as the temperature difference
is not too large.
The units for the parameters and their names in the Ansys Polymat interface are as follows:
Parameter | Name in Ansys Polymat | Mass | Length | Time | Temperature |
---|---|---|---|---|---|
| alfa | – | – | – | –1 |
| talfa | – | – | – | 1 |
Important: Note that for the approximate Arrhenius model is
not the same as
for the Arrhenius law; they have different units.
By default, and
are equal to 0. Figure 6.15: Approximate Arrhenius Law for Viscosity shows a
plot of
(
) for the approximate Arrhenius law.
The Arrhenius shear-stress law is defined by the same equation as the Arrhenius law (Equation 6–21), but differs in that a time-temperature equivalence has been introduced, as indicated by Equation 6–19. When the temperature increases, the viscosity curve shifts downward and to the right. Figure 6.16: Arrhenius Shear-Stress Law for Viscosity demonstrates this by showing the Bird- Carreau viscosity curve at several temperatures using the Arrhenius shear-stress law for temperature dependence.
The units, default values, and names for the parameters in the Ansys Polymat interface are the same as for the Arrhenius law, described above.
The approximate Arrhenius shear-stress law is defined by the same equation as the approximate Arrhenius law (Equation 6–22), but differs in that a time-temperature equivalence has been introduced, as indicated by Equation 6–19. When the temperature increases, the viscosity curve shifts downward and to the right. Figure 6.17: Approximate Arrhenius Shear-Stress Law for Viscosity demonstrates this by showing the Bird-Carreau viscosity curve at several temperatures using the approximate Arrhenius shear-stress law for temperature dependence.
The units, default values, and names for the parameters in the Ansys Polymat interface are the same as for the approximate Arrhenius law, described above.
Another definition for comes from the Fulcher law [5]:
(6–23) |
where ,
, and
are the Fulcher constants. The Fulcher law is used mainly for
glass.
The units for the parameters and their names in the Ansys Polymat interface are as follows:
Parameter | Name in Ansys Polymat | Mass | Length | Time | Temperature |
---|---|---|---|---|---|
| F1 | – | – | – | – |
| F2 | – | – | – | 1 |
| F3 | – | – | – | 1 |
By default, ,
, and
are equal to 0. Figure 6.18: Effect of Increasing f1 on the Fulcher Law for Viscosity how the impact of each parameter on the viscosity
curves. The viscosity drops if
increases, and increases if
increases. For
, the behavior is more complex: if
is below the fixed temperature, the viscosity increases with
an increase in
; if
is greater than the fixed temperature, the viscosity decreases
with an increase in
.
Figure 6.21: Effect of Increasing f3 (Greater Than Fixed Temperature) on the Fulcher Law for Viscosity
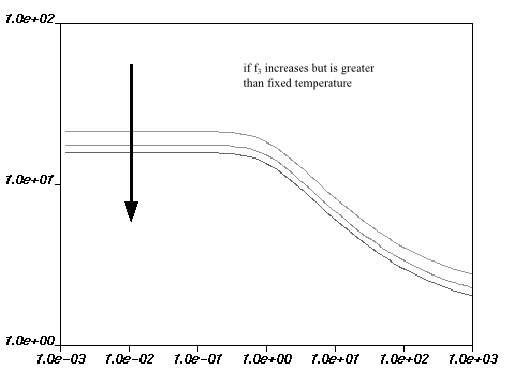
The Williams-Landel-Ferry (WLF) equation is a temperature-dependent viscosity law that fits experimental data better than the Arrhenius law for a wide range of temperatures, especially close to the glass transition temperature:
(6–24) |
where and
are the WLF constants, and
and
are reference temperatures.
The units for the parameters and their names in the Ansys Polymat interface are as follows:
Parameter | Name in Ansys Polymat | Mass | Length | Time | Temperature |
---|---|---|---|---|---|
| c1 | – | – | – | –1 |
| c2 | – | – | – | 1 |
| Ta | – | – | – | 1 |
| Tr-Ta | – | – | – | 1 |
Figure 6.22: Effect of Increasing c2 on the WLF Law for Viscosity and Figure 6.23: Effect of Increasing c1 or Ta on the WLF Law for Viscosity show the impact of
each parameter on the viscosity curves. The viscosity drops if increases; the opposite occurs if
,
, or
increases.
The WLF law described above is based on shear rate. As for the Arrhenius law,
there is also a version of the WLF law based on shear stress. In this version,
the viscosity is computed from Equation 6–19, with
computed from the WLF law, Equation 6–24. As for the Arrhenius shear-stress law, an increase
in temperature will result in a shifting of the viscosity curve downward and to
the right. This is illustrated in Figure 6.24: WLF Law for Viscosity and Figure 6.25: WLF Shear-Stress Law for Viscosity.
The units, default values, and names for the parameters in the Ansys Polymat interface are the same as for the WLF law, described above.
For the mixed-dependence law (which can be used only in conjunction with the
log-log law for shear-rate dependence, described in Log-Log Law), the
function η is written in the form of Equation 6–20, where
is computed from the log-log law (Equation 6–16) and
(6–25) |
In this equation, ,
, and
are the coefficients of the polynomial expression, and
is the temperature shift; it must be specified when a
non-absolute temperature scale is used. It corresponds to the lowest temperature
that is thermodynamically acceptable, given with respect to the current
temperature scale. Typically, if the units for temperature are Kelvin,
will be 0; if the units for temperature are Celsius,
will be –273.15.
The units for the parameters and their names in the Ansys Polymat interface are as follows:
Parameter | Name in Ansys Polymat | Mass | Length | Time | Temperature |
---|---|---|---|---|---|
| a2 | – | – | – | –1 |
| a22 | – | – | – | –2 |
| a12 | – | – | – | –1 |
| T0 | – | – | – | 1 |
By default, ,
, and
are equal to 0. Figure 6.26: Effect of Increasing a2 or a22 on the Mixed-Dependence Law for
Viscosity and Figure 6.27: Effect of Increasing a12 on the Mixed-Dependence Law for
Viscosity show the
impact of each parameter on the viscosity curves. The viscosity increases when
either
or
increases. For
, there is a rotation of the viscosity curves around a point
when the value is changed.
Depending on the values of the parameters, there may be a decrease in viscosity when the shear rate approaches zero (as shown in Figure 6.27: Effect of Increasing a12 on the Mixed-Dependence Law for Viscosity). This does not reflect physical behavior. Moreover, for high shear rates, the slope of the curve may be less than –1, which is also not physical. For the mixed-dependence law to be valid, the range of useful shear rates must lie between these two intervals.