This tutorial allows you to complete a reliability analysis of a single degree-of-freedom system excited with initial kinetic energy.
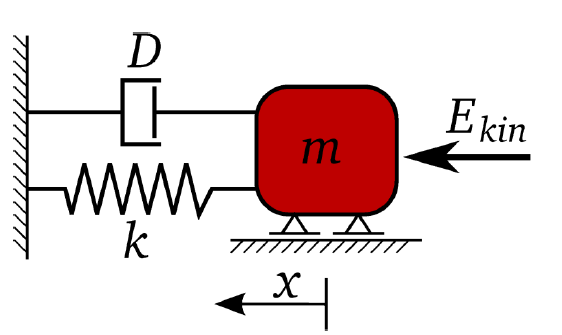
This tutorial uses the robust optimum found in the iterative robust design optimization procedure in the previous tutorial.
The reliability criterion for omega_damped will be evaluated.
Mass m, damping ratio D, stiffness k and initial kinetic energy Ekin are taken as normally distributed random variables.
In this tutorial, you complete the reliability evaluation using the optiSLang extension in Workbench.
This tutorial demonstrates how to do the following:
Incorporate the results of the robust design optimization
Define the limit state for damped eigen frequency
Compute the probability of failure (the probability of exceeding the limit) by Adaptive Response Surface Method and Importance Sampling
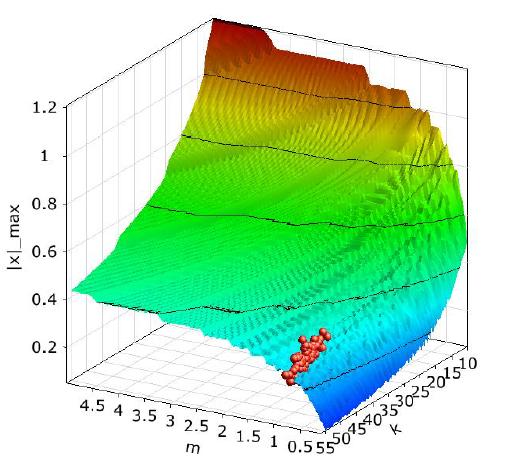
You must complete the Robustness Evaluation of a Damped Oscillator in Ansys Workbench tutorial before starting this one.
The best design of the iterative robust design optimization is used as the reference for the reliability analysis.
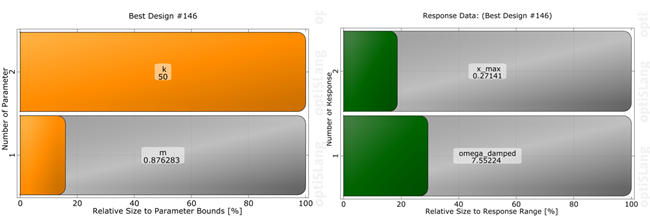
To set up and run the tutorial, perform the following steps:
Start Workbench.
From the menu bar, select
> .Browse to the location of the damped oscillator optimization Workbench project used in the previous tutorial
Click
.
Drag the Robustness wizard from the Toolbar and drop it onto the Robustness_Step2 system.
Do not adjust the values in the Parametrize Inputs table.
Click
.To delete the existing criteria, select all the values in the Criteria list then right-click the selection and select from the context menu.
At the prompt, click Yes.
Drag omega_damped to the Limit State Less icon.
Change the omega_damped Limit field to
8.5
.Click
.From the Uncertainty knowledge list, select .
The Adaptive Response Surface Method (ARSM-DS) is automatically selected.
Move the Desired sigma level slider to
4.5σ
Click
.A new Robustness system is added to the Project Schematic.
Double-click the new Robustness system name or right-click the system header and select
from the context menu.Type
ARSM_DS
.Press Enter.
To save the current project, from the menu bar, select
> or from the main toolbar, click.
Right-click the Results cell of the ARSM_DS system and select from the context menu.
The results of the ARSM-DS reliability evaluation are displayed. You can observe:
Failure probability is smaller than10-6
Corresponding reliability index is about 4.8 which fulfills the robustness requirements
In the m-k-anthill plot, a clearly separated unsafe domain can be observed
Drag the Robustness wizard from the Toolbar and drop it onto the ARSM_DS system.
From the Uncertainty knowledge list, select .
Move the Desired sigma level slider to
4.5σ
Select
.Click
.A new Robustness system is added to the Project Schematic.
Double-click the new Robustness system name or right-click the system header and select
from the context menu.Type
ISPUD
.Press Enter.
To save the current project, from the menu bar, select
> or from the main toolbar, click.
Right-click the Results cell of the ISPUD system and select from the context menu.
The results of the ISPUD reliability evaluation are displayed. You can observe:
The design point search converges within five iteration
Failure probability is about 10-6
Corresponding reliability index is about 4.7 which fulfills the robustness requirements
The ARSM-DS results are verified