VM-LSDYNA-EMAG-006
VM-LSDYNA-EMAG-006
Voltage Driven Coil
Overview
Reference: | Leonard, P. J. & Rodger, D. (1988). Voltage forced coils for 3D finite-element electromagnetic models. IEEE Transactions on Magnetics, 24(6). |
Analysis Type(s): | Electromagnetism |
Element Type(s): | Solid Elements |
Input Files: | Link to Input Files Download Page |
Test Case
In this test case, a stranded coil is voltage driven rather than having an imposed current. The current is deduced from the specified voltage, the number of windings, and the coil's total resistance. Properties for both coil and plates are given in the table below. The goal of the test is to predict the coil's current under the influence of the conducting plates and compare it with the experimental results.
Coil Properties | Plate Properties |
Inner radius = 0.087 m Outer radius = 0.116 m Height = 0.028 m Resistance = 12.4 Ω Voltage = 20 volts/step |
Length = 0.24 m Width = 0.24 m Thickness = 0.0127 m Conductivity = 3.28∙107 m-1 Separation = 0.03435 m |
Analysis Assumptions and Modeling Notes
The LS-DYNA model is shown below. The plates are depicted as blue and green. The coil is red.
LS-DYNA *EM_CONTROL card is set to 1 to activate the Eddy Current solver.
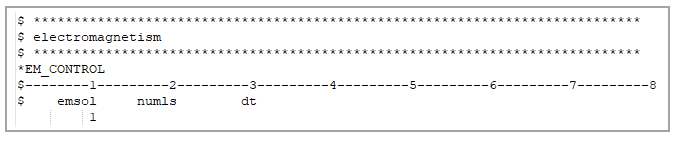
Coil properties, such as the number of turns, are given via *EM_CIRCUIT_SOURCE card.
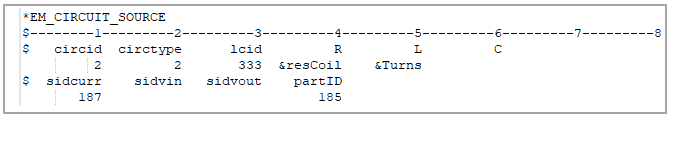
Rigid materials definition is used via MAT_RIGID for all the components.
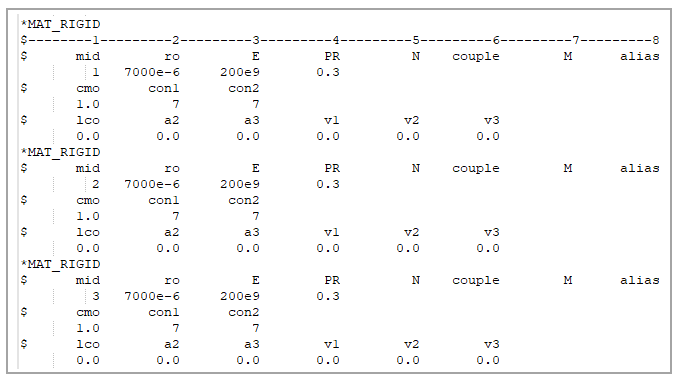
Electromagnetic properties are given to the plates and coil using EM_MAT_002 and EM_MAT_001.
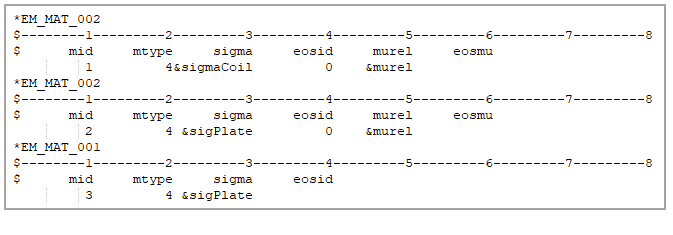
Finally, some properties are given parametrically and stored as parameters.
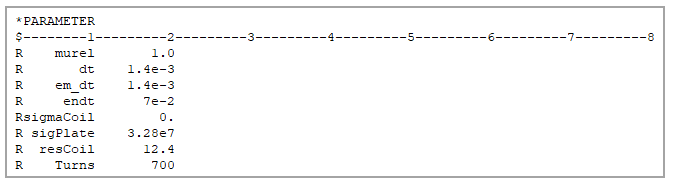
The mesh is formed by solid elements with Formulation 1, which is a constant stress solid element. Four elements are generated across the plate’s thickness for better accuracy. Two Elements are used for the coil.
Results Comparison
Experimental and simulation results are compared in Figure 193. Simulation results are extracted from output file em_circuitSource_002.dat.
In the table below, the error is given for several time increments. The discrepancy is below 3% which is a good correlation between the solver and the experiment. Figure 194 shows the relative error across the simulation.
Result | Target | LS-DYNA | Error (%) |
current [A] at t = 0.0104 s | 1.172 | 1.196 | 2.007 |
current [A] at t = 0.019533 s | 1.326 | 1.347 | 1.509 |
current [A] at t = 0.028 s | 1.419 | 1.433 | 1.023 |
current [A] at t = 0.0378 s | 1.483 | 1.496 | 0.843 |
current [A] at t = 0.0462 s | 1.520 | 1.536 | 0.993 |
current [A] at t = 0.0546 s | 1.547 | 1.561 | 0.932 |
current [A] at t = 0.063 s | 1.566 | 1.583 | 1.072 |
current [A] at t = 0.0698 s | 1.577 | 1.594 | 1.073 |