The Dhole, Chhabra & Eswaran Drag Law [6] module enables you to use a drag correlation proposed by Dhole, Chhabra & Eswaran in CFD Coupling simulations that specifically include non-Newtonian fluids that obey the Ostwald?de Waele (power-law) relationship. This module works by applying the power-law model which uses two fitting constants.
Non-Newtonian fluids can be found in multiple industries such as chemical, oil and gas, food and beverage, pharmaceutical, paints, and cosmetics. Therefore, having a model that allows the modeling of particle flow in such fluids is crucial.
This module works only if the Rocky project is CFD-coupled with one of the following modes:
1-Way Fluent Steady State
2-Way Fluent
1-Way Constant
This module does not work with the 2-Way Fluent Semi-Resolved nor the 1-Way LBM CFD Coupling methods. This correlation is best suited for spherical particles in dilute flows.
Note: The correlation implemented in this module includes a factor correction that accounts for the non-Newtonian behavior of the fluid in the drag force, it does not account for the particle shape nor the local volume fraction.
In addition, because drag laws must be specified per particle group in Rocky, after enabling this module you will therefore need to select it when defining your CFD Coupling Particle Interactions (Figure 8.1: Interactions tab options for the 1-Way Constant CFD Coupling mode when the Dhole, Chhabra & Eswaran Drag Law module is enabled.).
Figure 8.1: Interactions tab options for the 1-Way Constant CFD Coupling mode when the Dhole, Chhabra & Eswaran Drag Law module is enabled.
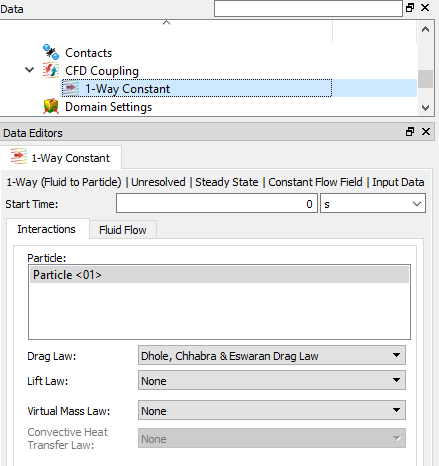
This module has two parameters that you can set, which are explained below and shown in Figure 8.2: Dhole, Chhabra & Eswaran Drag Law module options..
Dhole, Chhabra & Eswaran Drag Law module options.
Flow Behavior Index: This defines the power-law behavior index of the non-Newtonian drag law.
Range: [Positive values.]
Flow Consistency Index: This defines the power-law consistency index of the non-Newtonian drag law.
Range: [Positive values.]
In addition to defining the parameters on the module itself, there is an additional option you must set for your CFD Coupling mode. As shown in Figure 8.1: Interactions tab options for the 1-Way Constant CFD Coupling mode when the Dhole, Chhabra & Eswaran Drag Law module is enabled., you must define for at least one Particle in your project the Drag Law as Dhole, Chhabra & Eswaran Drag Law.
After processing your simulation, you are able to analyze your results using the same particle-related properties that are available by default in Rocky.
In addition, it is possible to collect additional fluid-particle statistics for later post-processing, such as drag or pressure gradient forces, by first enabling the CFD Coupling Particle Statistics module before you process your simulation.
Note: Properties generated by this module will only appear if the Upscaling is disabled.Refer to Rocky User Manual (5.1.7. About Meshed Particles Upscaling) for more details.
Ensure that the module is enabled. (From the Data panel, select Modules and then from the Data Editors panel, ensure the Dhole, Chhabra & Eswaran Drag Law checkbox is enabled.)
Tip: If you want to collect particle-fluid statistics, ensure you also enable the CFD Coupling Particle Statistics module, and choose what kind of statistics you want to collect. (Refer to the About Fluid- Related Statistics for Particles topic in the Rocky User Manual for details.)
From the Data panel, under Modules, select the new Dhole, Chhabra & Eswaran Drag Law entry.
From the Data Editors panel, on the Dhole, Chhabra & Eswaran Drag Law tab, enter the values you want.
Continue setting up the simulation as you normally would, with the following exceptions:
When setting up your CFD Coupling options, ensure the following:
You have selected a supported CFD Coupling mode. (Either 1-Way Constant, 1-Way Fluent Steady State, or 2-Way Fluent).
For the CFD Coupling mode you have enabled, on the Interactions tab for at least one Particle, you have defined the Drag Law as Dhole, Chhabra & Eswaran Drag Law.
Process the simulation as you normally would.
When you are ready to analyze your simulation results, you may choose to make use of any particle-related Property. Or if you chose to enable the CFD Coupling Particle Statistics module, you may also make use of those additional fluid-particle properties.
When using Rocky with CFD Coupling for modeling fluid-particulate systems, drag correlations are used to compute the drag force acting on each particle, based on local fluid properties and the relative velocity between the fluid flow and the particles.
The Dhole, Chhabra & Eswaran Drag Law module must be applied in
simulations including non-Newtonian fluids whose behavior is adequately described by the power
law, also known as Ostwald-de Waele relationship. In this relationship, the shear stress,
, relates to the shear rate,
, according to [7]:
(8–1) |
where:
is the power-law behavior index. This dimensionless parameter is defined by the user in the Dhole, Chhabra & Eswaran Drag Law module.
is the power-law consistency index, measured in
, which is defined by the user in the Dhole, Chhabra & Eswaran Drag Law module.
According to the power-law behavior index, fluids that obey are classified into three types:
Newtonian fluids: Power-law fluids with n=1, where the shear stress is directly proportional to the shear rate. The majority of the common fluids have this constant viscosity across all shear rates, including water, oils, and gases.
Pseudoplastic, or shear-thinning fluids: Power-law fluids with n<1, whose apparent viscosity decreases with increasing shear rates. This behavior is commonly encountered in solutions or suspensions, particularly when polymer solutions are used. Examples of pseudoplastic fluids are blood, milk, paints, and drilling fluids.
Dilatant, or shear-thickening fluids: Power-law fluids with n>1, and which shows a proportional increase in the shear stress as a function of shear rate. One example is the mixture of cornstarch and water, which hardens upon application of high enough forces, allowing people to run across large pools filled with the mixture. Potential applications of dilatant fluids are liquid armor and smart speed bumps.
When considering these types of fluids, the Reynolds number definition has to be modified
to account for the power-law index and the consistency index. The modified particle Reynolds
number is defined as follows [8]:
(8–2) |
where:
is the fluid density, measured in [kg/m3], which is defined by the user on the CFD Coupling setup.
is the particle velocity vector, measured in [m/s].
is the fluid velocity vector, measured in [m/s], which is defined by the user on the CFD Coupling setup when CFD Coupling mode is 1-Way Constant.
is the equivalent diameter of the particle, measured in [m], which is defined as the diameter of a sphere whose volume is equal to the particle's volume.
Based on numerical simulations of the flow of a power-law fluid past a sphere, Dhole,
Chhabra & Eswaran [6] obtained the following correlation for the
drag coefficient, :
(8–3) |
This correlation for the drag coefficient is valid for the following ranges:
(8–4) |