This tutorial includes:
- 31.1. Tutorial Features
- 31.2. Overview of the Problem to Solve
- 31.3. Preparing the Working Directory
- 31.4. Defining a Steady-state Case in CFX-Pre
- 31.5. Obtaining a Solution to the Steady-state Case
- 31.6. Defining a Transient Blade Row Case in CFX-Pre
- 31.7. Obtaining a Solution to the Transient Blade Row Case
- 31.8. Viewing the Time Transformation Results in CFD-Post
In this tutorial you will learn about:
Component | Feature | Details |
---|---|---|
CFX-Pre | User Mode | Turbo Wizard |
General Mode | ||
Analysis Type | Transient Blade Row | |
Fluid Type | Air Ideal Gas | |
Domain Type | Single Domain | |
Stationary Frame | ||
Turbulence Model | k-Epsilon | |
Heat Transfer | Total Energy | |
Boundary Conditions | Inlet (Subsonic) | |
Outlet (Subsonic) | ||
CFD-Post | Plots | Contour |
Animation |
The goal of this tutorial is to set up a transient blade row calculation to model an inlet disturbance (frozen gust) using the Time Transformation model. The tutorial uses an axial turbine to illustrate the basic concepts of setting up, running, and monitoring a transient blade row problem in Ansys CFX.
In this tutorial, the full geometry of the axial rotor-stator stage contains 21 stator blades and 28 rotor blades. The schematic below shows three stator blades along with the profile boundary showing a disturbance in the total temperature of the flow:
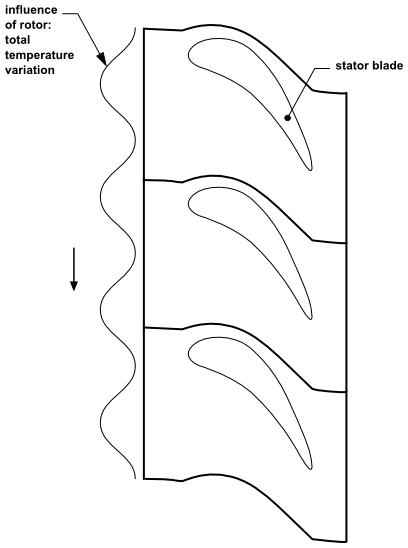
Rotational periodicity boundaries are used to enable only a small section of the full geometry to be modeled.
In your model, you should always try to obtain a pitch ratio as close to unity as possible to minimize approximations, but this must be weighted against computational resources. For this disturbance/passage geometry, 1/7 of the full wheel (4 disturbance pulses and 3 passages) would produce a pitch ratio of 1.0, but this would require a model about 3 times larger than in this tutorial example.
Using the Time Transformation method, you can work with pitch ratios near unity in order to minimize computational requirements, with little loss of accuracy. The acceptable range of pitch ratios varies, depending on the case. In this tutorial, the geometry that will be modeled consists of just a single blade passage from the stator, which is a 17.14° section (360°/21 blades). With only one stator blade, the rotor-stator pitch ratio is 4:3, which happens to fall within the acceptable range (as can be confirmed in the "Time Transformation stability limits" section of the CFX-Solver Output file for the second part of this tutorial).
The rotor is upstream of the stator, and creates a disturbance in the total temperature of the flow. The rotor will be modeled by applying a moving profile boundary condition at the inlet of the stator blade passage. In this case, the profile is of total temperature in a Gaussian distribution with a maximum that is 20% higher than the baseline value, and a pattern that repeats in the theta direction every 12.86° (360°/28 blades). To create a moving disturbance, the profile boundary is applied on a moving coordinate frame that rotates about the machine axis at 6300 rev/min. In this case, the machine axis is the Z axis. The rotation direction is positive using the right-hand rule as applied to the machine axis. The total temperature profile is implemented via CEL expressions that are provided in a .ccl file.
The outlet boundary condition is a static pressure profile, provided in a .csv file. It was obtained from a previous simulation of a downstream stage.
The flow is modeled as being turbulent and compressible.
The overall approach to solving this problem is:
Define the simulation using the Turbomachinery wizard in CFX-Pre.
Import the stator mesh, which was created in Ansys TurboGrid.
Enter the basic model definition.
Set the profile boundary conditions using CFX-Pre in General mode.
Run the steady-state simulation.
Modify the simulation to use the Time Transformation model.
Run the transient blade row simulation using the steady-state results as an initial guess.
Create contours of temperature and animate them in CFD-Post.
If this is the first tutorial you are running, it is important to review the following topics before beginning:
Create a working directory.
Ansys CFX uses a working directory as the default location for loading and saving files for a particular session or project.
Download the
time_inlet_disturbance.zip
file here .Unzip
time_inlet_disturbance.zip
to your working directory.Ensure that the following tutorial input files are in your working directory:
TBRInletDistCEL.ccl
TBRInletDistOutlet.csv
TBRInletDistStator.gtm
Set the working directory and start CFX-Pre.
For details, see Setting the Working Directory and Starting Ansys CFX in Stand-alone Mode.
This tutorial uses the Turbomachinery wizard in CFX-Pre. This preprocessing mode is designed to simplify the setup of turbomachinery simulations.
In CFX-Pre, select
> .Select TurboMachinery and click .
Select
> .Under File name, type
TimeInletDistIni
.Click
.If you are notified that the file already exists, click Overwrite.
In the Basic Settings panel, configure the following:
Setting
Value
Machine Type
Axial Turbine
Axes
> Rotation Axis
Z
Analysis Type
> Type
Steady State
Leave the other settings at their default values.
Click
.
As stated in the overview, this tutorial requires a single blade passage for the stator. You will define a single component and import its mesh.
Right-click in the blank area and select Add Component from the shortcut menu.
Create a new component of type
Stationary
, namedS1
and click .Configure the following setting(s):
Setting
Value
Mesh
> File
TBRInletDistStator.gtm[a]
Click
.
In this section, you will set properties of the fluid domain and some solver parameters.
In the Physics Definition panel, configure the following setting(s):
Setting
Value
Fluid
Air Ideal Gas
Model Data
> Reference Pressure
0 [atm] [a]
Model Data
> Heat Transfer
Total Energy
Model Data
> Turbulence
k-Epsilon
Inflow/Outflow Boundary Templates
> P-Total Inlet P-Static Outlet
(Selected)
Inflow/Outflow Boundary Templates
> Inflow
> P-Total
200000 [Pa]
Inflow/Outflow Boundary Templates
> Inflow
> T-Total
500 [K] [b]
Inflow/Outflow Boundary Templates
> Inflow
> Flow Direction
Cylindrical Components
Inflow/Outflow Boundary Templates
> Inflow Direction (a,r,t)
1, 0, –0.4
Inflow/Outflow Boundary Templates
> Outflow
> P-Static
175000 [Pa] [b]
Continue to click
until you reachFinal Operations
.Set Operation to
Enter General Mode
because you will continue to define the simulation through settings not available in the Turbomachinery wizard.Click Finish.
You will include additional settings to improve the accuracy of the simulation.
Edit
S1
.Configure the following setting(s):
Tab
Setting
Value
Fluid Models
Heat Transfer
> Incl. Viscous Work Term
(Selected)
Turbulence
> High Speed (compressible) Wall Heat Transfer Model
(Selected)
Click
.
The inlet and outlet boundary conditions are defined using profiles. Boundary profile data must be initialized before they can be used for boundary conditions.
Select
> > .Select Import Method > Append.
From your working directory, select TBRInletDistCEL.ccl.
Click
.Select
> .The Initialize Profile Data dialog box appears.
Beside Profile Data File, click Browse
.
The Select Profile Data File dialog box appears.
From your working directory, select TBRInletDistOutlet.csv.
Click
.Click
.The profile data is read into memory.
Note: After profile data has been initialized from a file, the profile data file should not be deleted or otherwise removed from its directory. By default, the full file path to the profile data file is stored in CFX-Pre, and the profile data file is read directly by CFX-Solver each time the solver is started or restarted.
Here, you will apply profiles to the inlet and outlet boundary conditions.
Edit
S1 Inlet
.Configure the following setting(s):
Tab
Setting
Value
Boundary Details
Heat Transfer
> Option
Total Temperature
Heat Transfer
> Total Temperature
TINLET [a]
Click
.Edit
S1 Outlet
.Configure the following setting(s):
Tab
Setting
Value
Basic Settings
Profile Boundary Conditions
> Use Profile Data
(Selected)
Profile Boundary Setup
> Profile Name
outlet
Click
.Click
.
At this point, CFX-Solver Manager is running.
Ensure that the Define Run dialog box is displayed.
Click Start Run.
CFX-Solver runs and attempts to obtain a solution. This may take a long time, depending on your system. Eventually a dialog box is displayed.
Clear the check box next to Post-Process Results when the completion message appears at the end of the run.
Click
.If using stand-alone mode, quit CFX-Solver Manager.
In this second part of the tutorial, you will modify the simulation from the first part of the tutorial in order to model the transient blade row.
This step involves opening the original simulation and saving it to a different location.
Ensure that the following tutorial input files are in your working directory:
TBRInletDistOutlet.csv
TimeInletDistIni.cfx
TimeInletDistIni_001.res
Set the working directory and start CFX-Pre if is it not already running.
For details, see Setting the Working Directory and Starting Ansys CFX in Stand-alone Mode.
If the original simulation is not already opened, then open
TimeInletDistIni.cfx
.Save the case as
TimeInletDist.cfx
in your working directory.
Modify the analysis type as follows:
Edit
Analysis Type
.Configure the following setting(s):
Setting
Value
Analysis Type
> Option
Transient Blade Row
Click
.
Create a local rotating coordinate frame that will be applied to the inlet boundary in order to cause the inlet boundary condition to rotate:
Select
> .Accept the default name and click
.Configure the following setting(s):
Setting
Value
Option
Axis Points
Coordinate Frame Type
Cartesian
Ref. Coord. Frame
Coord 0
Origin
0, 0, 0
Z Axis Point
0, 0, 1
X-Z Plane Pt
1, 0, 0
Frame Motion
(Selected)
Frame Motion
> Option
Rotating
Frame Motion
> Angular Velocity
VSignal [a]
Frame Motion
> Axis Definition
> Option
Coordinate Axis
Frame Motion
> Axis Definition
> Rotation Axis
Global Z
Click
.
You will set the simulation to be solved using the Time Transformation method.
Edit
Transient Blade Row Models
.Set Transient Blade Row Model > Option to
Time Transformation
.Under
Time Transformation
, click Add new item, accept the default name, and click .
Configure the following setting(s):
Setting
Value
Time Transformation
> Time Transformation 1
> Option
Rotational Flow Boundary Disturbance
Time Transformation
> Time Transformation 1
> Domain Name
S1
Time Transformation
> Time Transformation 1
> Signal Motion
> Option
Rotating
Time Transformation
> Time Transformation 1
> Signal Motion
> Coordinate Frame
Coord 1
Time Transformation
> Time Transformation 1
> External Passage Definition
> Passages in 360
28
Time Transformation
> Time Transformation 1
> External Passage Definition
> Pass. in Component
1
Transient Method
> Time Period
> Option
Passing Period[a]
Transient Method
> Time Steps
> Option
Number of Timesteps per Period
Transient Method
> Time Steps
> Timesteps/Period[b]
60[c]
Transient Method
> Time Duration
> Option
Number of Periods per Run
Transient Method
> Time Duration
> Periods per Run
9
The passing period is automatically calculated as: 2 * pi / (Passages in 360 * Signal Angular Velocity). The Passing Period setting cannot be edited.
The number of time steps per period should always be larger than 2 * Number of Fourier Coefficients + 1 to be used for postprocessing.
The time step size is also automatically calculated as: Passing Period / Number of Timesteps per Period. The Timestep setting cannot be edited.
Click
.
You can create a moving disturbance by applying a moving coordinate frame to a boundary.
Add rotational motion to the boundary condition values on the inlet by applying the local rotating coordinate frame that you made earlier:
Edit
S1 Inlet
.Configure the following setting(s):
Tab
Setting
Value
Basic Settings
Coordinate Frame
(Selected)
Coordinate Frame
> Coordinate Frame
Coord 1
Click
.
For transient blade row calculations, a minimal set of variables
are selected to be computed using Fourier coefficients. It is convenient
to postprocess total (stagnation) variables as well. Here, you will
add Total Pressure
and Total Temperature
variables to the default list.
In addition, monitor points can be used to effectively compare the Time Transformation results against a reference case. They provide useful information on the quality of the reference phase and frequency produced in the simulation. They should also be used to monitor convergence and, as the simulation converges, the user points should display a periodic pattern.
Note:
When comparing to a reference case, make sure monitor points are placed in the same relative locations with respect to the initial configuration in both cases.
It is important to check that the solver equations are being solved correctly. Monitoring pressure provides feedback on the momentum equations while monitoring temperature provides feedback on the energy equations.
Set up the output control and create monitor points as follows:
Click Output Control
.
Click the Trn Results tab.
Configure the following setting(s):
Setting
Value
Transient Blade Row Results
> Extra Output Variables List
(Selected)
Transient Blade Row Results
> Extra Output Variables List
> Extra Output Var. List
Total Pressure, Total Temperature[a]
Click
.Click the Monitor tab.
Configure the following setting(s):
Setting
Value
Monitor Objects
> Monitor Points and Expressions
Create a monitor point named
Monitor Point 1
[a]Monitor Objects
> Monitor Points and Expressions
> Monitor Point 1
> Output Variables List
Pressure, Temperature, Total Pressure, Total Temperature[b]
Monitor Objects
> Monitor Points and Expressions
> Monitor Point 1
> Cartesian Coordinates
(0.31878, 0.02789, 0.1)
Create additional monitor points with the same output variables. The names and Cartesian coordinates are listed below:
Name
Cartesian Coordinates
Monitor Point 2
(0.319220, 0.022322, 0.16)
Monitor Point 3
(0.312644, 0.064226, 0.162409)
Monitor Point 4
(0.316970, -0.0359315, 0.06)
Click
.
Click Define Run
.
Configure the following setting(s):
Setting
Value
File name
TimeInletDist.def
Click
.Ignore the error message (the initial values will be specified in CFX-Solver Manager) and click Yes to continue.
CFX-Solver Manager automatically starts and, on the Define Run dialog box, Solver Input File is set.
If using stand-alone mode, quit CFX-Pre, saving the simulation (.cfx) file at your discretion.
When CFX-Pre has shut down and the CFX-Solver Manager has started, obtain a solution to the CFD problem by following the instructions below. To reduce the simulation time, the simulation will be initialized using a steady-state case.
Ensure that the Define Run dialog box is displayed.
Ensure that Solver Input File is set to
TimeInletDist.def
.Under the Initial Values tab, select Initial Values Specification.
Under Initial Values Specification > Initial Values, select
Initial Values 1
.Under Initial Values Specification > Initial Values > Initial Values 1 Settings > File Name, click Browse
.
Select TimeInletDistIni_001.res from your working directory.
Click Open.
Under Initial Values Specification > Use Mesh From, select
Solver Input File
.Click
.CFX-Solver runs and attempts to obtain a solution. This can take a long time depending on your system. Eventually a dialog box is displayed.
Note:Before the simulation begins, the "Transient Blade Row Post-processing Information" summary in the CFX-Solver Output file will display the time step range over which the solver will accumulate the Fourier coefficients.
Similarly, the "Time Transformation Stability" summary in the CFX-Solver Output file displays whether the Passage/Signal pitch ratio is within the acceptable range.
After the CFX-Solver Manager has run for a short time, you can track the monitor points you created in CFX-Pre by clicking the Time Corrected User Points tab that appears at the top of the graphical interface of CFX-Solver Manager.
After the simulation has proceeded for some time, observe the periodic nature of the monitor point values.
When CFX-Solver is finished, select the check box next to Post-Process Results.
Click
.
In this section, you will work with the Fourier coefficients compressed data in transient blade row analysis. The solution variables are automatically set to the transient position corresponding to the end of the simulation.
You will see a dialog box named Transient Blade Row Post-processing. Click .
Click the Turbo tab.
A dialog box will ask if you want to auto-initialize all turbo components. Click Yes.
Select
> > .Change the name to
Span 50
.Click
.Click
.Turn off the visibility of
Span 50
.
Click Insert > Contour and accept the default name.
Configure the following setting(s):
Tab
Setting
Value
Geometry
Locations
Span 50
Variable
Temperature
Range
User Specified
Min
465 [K]
Max
605 [K]
# of Contours
21
Click
.