The following example NLAD-ETCHG problems are available:
This example NLAD-ETCHG analysis features a plate with notches meshed with SOLID185 elements undergoing small deformation (NLGEOM,OFF).
The model uses a linear elastic material:

Pressure loads are applied.
NLADAPTIVE and other commands are shown in the following figures. For more information, see Understanding the NLAD-ETCHG Process.)
The first remeshing converts the hexahedral SOLID185 mesh to tetrahedral SOLID187. Subsequent remeshings refine the tetrahedral SOLID187 mesh via an energy-based criterion (as specified via NLADAPTIVE).
The following figure shows the equivalent stress plots corresponding to the substeps just prior to the hex-to-tet conversion (2), immediately after hex-to-tet conversion (3), and the last substep (5) (following two standard nonlinear mesh adaptivity remeshings using the specified criterion for refinement).
This example NLAD-ETCHG analysis features an offset punch of a block meshed with SOLID186 elements undergoing large (NLGEOM,ON).
The model is a deformable elastoplastic block with a rigid indenter punch through which vertical displacement loads are applied.
The material type is elastoplastic (TB,PLASTIC,,,,BISO):
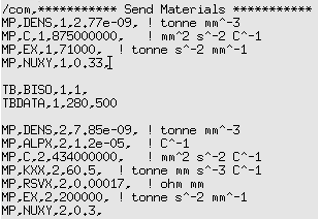
Loading occurs via an applied displacement through the pilot node on a rigid target.
NLADAPTIVE and other commands are shown in the following figures. For more information, see Understanding the NLAD-ETCHG Process.)
The first remeshing converts the hexahedral SOLID185 mesh to tetrahedral SOLID187. Subsequent remeshings refine the tetrahedral SOLID187 mesh via the energy-based and skewness criteria (as specified via NLADAPTIVE).
The following figure shows equivalent plastic strain plots corresponding to the substeps just prior to NLAD-ETYPE (9), immediately following NLAD-ETYPE (10), and at the last substep (28) (following three conventional nonlinear mesh adaptivity remeshings using the specified criteria for refinement).