For explicit analyses (LS-DYNA), the workflow consists of three parts as shown below:
Using Material Designer's homogenization technology, characterize the macroscopic response of the composite material (represented in system A below).
Using the Injection Molding Data system (system B below), import injection molding simulation results from other software tools.
In Ansys Mechanical, set up an LS-DYNA analysis system for simulating the part (system C).
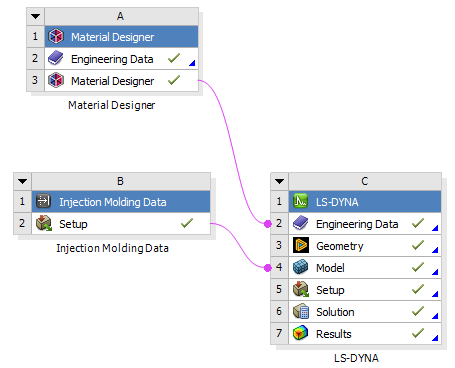
Notes and Limitations
Short fiber composite workflows have the following limitations in Workbench LS-DYNA:
As is the case for implicit analyses, only solid bodies are supported.
Imported Material Fields can only be scoped to bodies. Scoping to element Named Selections is not supported.
The nonlinear isotropic hardening of Voce type is not supported. In Material Designer, you should instead select the Inverse Polynomial or Multilinear Hardening Models.
LS-DYNA systems do not support the Material Assignment. Therefore, assigning a dedicated material to weld regions is not supported.
The short fiber composite material cannot depend on the fiber volume fraction.
The LS-DYNA system does not support the Imported Initial Stress object from the Injection Molding Data system.
The CFL Time Step Tool is not supported for short fiber composite materials. (See Additional LS-DYNA Analysis Tools in the LS-DYNA User's Guide.)
If material properties are temperature dependent, they are always evaluated at the environment temperature defined in Mechanical. Body temperature and imported temperature fields are ignored.
If the short fiber material includes Orthotropic Stress Limits (as described in Short Fiber Composites: Stress Limits Computation in Material Designer (Beta)), Tsai-Hill failure and element erosion are automatically enabled in the solver. To turn it off, you must delete the Orthotropic Stress Limits property in Engineering Data.