This tutorial is divided into the following sections:
This tutorial demonstrates the process to set up perforated wall model and its capability for effusion cooling in a model combustor.
A slice of cylindrical combustor burning liquid fuel with methane () as the evaporated gas in hot air is studied using the FGM model
in Ansys Fluent.
This tutorial demonstrates how to do the following:
Enable physical models, select material properties, and define boundary conditions for a turbulent combustion flow with FGM model.
Set up perforated wall to model effusion cooling effects.
Initiate and solve the combustion simulation using the pressure-based solver.
Examine the reacting flow results using graphics.
This tutorial is written with the assumption that you have completed the introductory tutorials found in this manual and that you are familiar with the Ansys Fluent outline view and ribbon structure. Some steps in the setup and solution procedure will not be shown explicitly.
To learn more about turbulent combustion modeling and perforated walls, see the Fluent User's Guide and the Fluent Theory Guide.
The 3D model gas turbine combustor considered in this tutorial is shown in Figure 19.1: 3D model gas turbine combustor with liquid fuel Combustion of Methane. The flame considered is a turbulent diffusion flame with fuel supplied by liquid droplets. The air is introduced from the inlet with mass flow rate 0.10962 kg/s. Air flow is split into two streams, one goes through a swirl after which air and evaporated fuel mixed, and the other goes into the shroud. The fuel droplets are injected after the swirl and evaporation will occur. The evaporated fuel is set to be methane. After air and fuel are mixed, the flame is established in the main combustion chamber.
In this tutorial, you will use the FGM turbulent combustion model and DPM model to simulate analyze the methane-air combustion system. The effusion cooling effects are modeled with perforated wall capability. The effusion cooling mass flow rate are determined by the pressure difference between the shroud and the main combustion chamber.
The following sections describe the setup and solution steps for this tutorial:
To prepare for running this tutorial:
Download the
effusion_cooling.zip
file here .Unzip
effusion_cooling.zip
to your working directory.The SpaceClaim CAD file
combustor_effusion.scdoc
can be found in the folder.Use the Fluent Launcher to start Ansys Fluent.
Select Meshing in the top-left selection list to start Fluent in Meshing Mode.
Select 3D under Dimension.
Enable Double Precision under Options.
Set Meshing Processes and Solver Processes to
4
under Parallel (Local Machine).
Start the meshing workflow.
In the Workflow tab, select the Watertight Geometry workflow.
Review the tasks of the workflow.
Each task is designated with an icon indicating its state (for example, as complete, incomplete, etc. For more information, see Understanding Task States in the Fluent User's Guide). All tasks are initially incomplete and you proceed through the workflow completing all tasks. Additional tasks are also available for the workflow. For more information, see Customizing Workflows in the Fluent User's Guide.
Import the CAD geometry (
combustor_effusion.scdoc
).Select the Import Geometry task.
For Units, select mm.
For File Name, enter the path and file name for the CAD geometry that you want to import (
combustor_effusion.scdoc
).Note: The workflow only supports
*.scdoc
(SpaceClaim), Workbench (.agdb
), and the intermediary*.pmdb
file formats.Click
.This will update the task, display the geometry in the graphics window and allow you to proceed onto the next task in the workflow.
The combustor geometry has been enclosed in a suitable flow domain, which should provide distinct regions of inflow and outflow for a range of angles of attack, and avoids having the bow shock that forms in such flows from contacting the inflow surfaces..
Note: Alternatively, the ... button next to File Name can be used to locate the CAD geometry file, after which, the Import Geometry task automatically updates, displaying the geometry in the graphics window, and the workflow automatically progresses to the next task.
Throughout the workflow, you are able to return to a task and change its settings using either the Edit button, or the Revert and Edit button.
Add local sizing.
Local mesh sizing controls are added on the liner surfaces using face sizing.
In the Add Local Sizing task, add local sizing controls to the faceted geometry by selecting yes:
In this tutorial, we will add local sizing around the surfaces of the liner, since they are areas where we require a more refined mesh.
At the prompt for adding local sizing, select yes.
Retain the default
facesize_1
for the Name of the size control.Specify
1.2
for the Growth Rate.Retain Face Size for the Size Control Type.
Specify
1
for the Target Mesh Size.Select Label for the Select By.
Select
wall-liner
andwall-liner-cold
.Click
.
Generate the surface mesh.
With the local sizing set as described above, the global surface mesh sizing only defines the largest elements on other surfaces.
In the Generate the Surface Mesh task, you can set various properties of the surface mesh for the faceted geometry.
Specify
1
for the Minimum Size.Specify
10
for the Maximum Size.Note: The red boxes displayed on the geometry in the graphics window are a graphical representation of size settings. These boxes change size as the values change, and they can be hidden by using the Clear Preview button.
Specify
1.2
for the Growth Rate.Click Generate the Surface Mesh to complete this task and proceed to the next task in the workflow.
Describe the geometry.
When you select the Describe Geometry task, you are prompted with questions relating to the nature of the imported geometry.
Select The geometry consists of only fluid regions with no voids option under Geometry Type, since this model contains only the fluid region.
Keep the rest of the default settings for this task.
Click Describe Geometry to complete this task and proceed to the next task in the workflow.
Confirm and update the boundaries.
Select the Update Boundaries task, where you can inspect the mesh boundaries and confirm and change any designated boundaries accordingly. Ansys Fluent attempts to determine the correct arrangement of boundaries automatically.
Rename wall-internal to wall-int for the boundary name.
Rename Inlet-fuel to wall-fuel for the boundary name.
Select wall for the wall-fuel boundary type.
Select mass-flow-inlet for the inlet boundary type.
Click Update Boundaries and proceed to the next task.
Insert a new task and create the periodic boundaries.
Right click on the Update Boundaries task, Insert New Task and select Set Up Periodic Boundaries.
Retain the default Select the Update Boundaries task, where you can inspect the mesh boundaries and confirm and change any designated boundaries accordingly. Ansys Fluent attempts to determine the correct arrangement of boundaries automatically.
Retain the default
Rotational
for the Type of periodic boundary,Automatic - pick both sides
for the Method andLabel
for Select By:.Select periodic_1 and periodic_2 for the two sides of the periodic boundary.
Click Set Up Periodic Boundaries and proceed to the next task.
Update your regions.
Select the Update Regions task, where you can review and change the tabulated names and types of the various regions that have been generated from your imported geometry and change them as needed.
The proposed region type is correct, so click Update Regions to update your settings.
Add boundary layers.
Select the Add Boundary Layers task, where you can set properties of the boundary layer mesh.
For the Add Boundary Layers task, ensure yes is selected at the prompt as to define boundary layer settings. In this task, you can define specific details for capturing the boundary layer in and around your geometry.
Click Add Boundary Layers.
Generating the volume mesh.
With the local sizing set as described above, including bodies of influence, the global volume mesh sizing only defines the largest elements in the flow domain. In this case, the maximum is set to be consistent with the specified global surface mesh sizing.
Select the Generate the Volume Mesh task, to set properties of the volume mesh.
Select the polyhedra for Fill With.
Specify
10
for Max Cell Length.Retain the default selection of Enable Parallel Meshing.
Click Generate the Volume Mesh.
Ansys Fluent will apply your settings and proceed to generate a volume mesh for the geometry.. The mesh is displayed in the graphics window and a clipping plane is automatically inserted with a layer of cells drawn so that you can quickly see the details of the volume mesh.
Check the mesh.
Mesh → Check → Perform Mesh Check
Save the mesh file (
combustor_effusion.msh.h5
).File → Write → Mesh...
Switch to Solution mode.
Now that a mesh has been generated using Ansys Fluent in meshing mode, you can now switch to solver mode to complete the set up of the simulation. Note that to obtain more accurate solutions a higher quality mesh should be used.
We have just checked the mesh, so select Yes when prompted to switch to solution mode.
Examine the mesh.
Domain → Mesh → Display...
Enable Edges in the Options group box.
Ensure All is selected in the Edge Type group box.
Select Wall from the Surfaces selection list.
Click Display and close the Mesh Display dialog box.
In the Solver group box of the Physics ribbon tab, retain the default selection of the steady pressure-based solver.
Setup
→
General
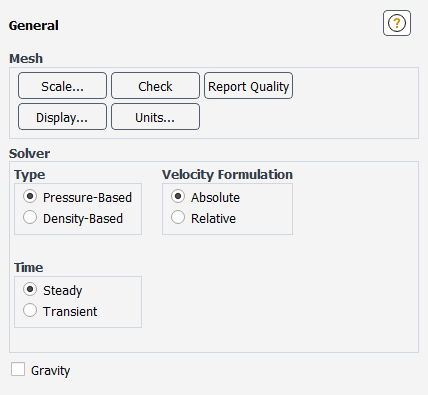
Enable heat transfer by enabling the energy equation.
Physics → Models → Energy
Retain the default k-ω SST turbulence model.
Physics → Models → Viscous...
Retain the default settings for the k-omega model.
Click Viscous Model dialog box.
to close the
Enable chemical species transport and reaction.
Physics → Models → Species...
Select Partially Premixed Combustion in the Model list.
The Species Model dialog box will expand to provide further options for the Partially Premixed Combustion model.
In the Chemistry Tab,
Select the Flamelet Generated Manifold in the State Relation group box.
Select Non-Adiabatic in the Energy Treatment group box.
Enable Compressibility Effects in the PDF Options group box.
Select Diffusion Flamelet in the Flamelet Type group box.
Set the Equilibrium Operating Pressure (Pa) to
1519875
under Model Settings.Click Import CHEMKIN Format Mechanism dialog box.
to open theSelect
drm19.inp
for the Kinetics Input File.Select
thermo30.dat
for the Thermodynamic Database.Click Import CHEMKIN Format Mechanism dialog box.
and close the
In the
tabSet ch4 to
1.0
.Set the Fuel to be
755.37
K and the Oxid to be422.04
K under TemperatureSelect Mole Fraction under Specify Species In.
In the
tab, retain the existing settings.In the
tab,Enable Automated Grid Refinement.
Set the Initial Number of Grid Points in Flamelet to
16
.Click the Calculate Flamelets button.
Then answer Yes and save the flamelet solution into a file named
combustor_effusion.fla.gz
.
In the
tabClick the Calculate PDF Table button.
Click Species Model dialog box.
to close theSave the PDF output file (
combustor_effusion.pdf.gz
).File → Write → PDF...
Enter
combustor_effusion.pdf.gz
for PDF File name.Click
to write the file.
Enable Discrete Phase Model
Physics → Models → Discrete Phase...
Enable the Interaction with Continuous Phase in the Interaction group box.
Set the DPM Iteration Interval to
50
.In the Numerics Tab
Enable Linearize Source Terms in the Source Terms group box.
Click the Injections button.
Click the Create button.
Select Cone as the injection type and set the Number of Streams to
300
.Select Droplet as the Particle Type.
Select kerosene-liquid as the Material and choose ch4 as the Evaporating Species.
Enable the Uniform Massflow Distribution option.
Set the X-Position [m] to
0.015
m, Y-Position [m] to0.002
m, and the Z-Position [m] to-0.08
m.Set the Diameter [m] to
3.0E-5
m.Set the Temperature [K] to
340
K.Set the Velocity Magnitude [m/s] to
50
m//s.Set the Cone Angle to
12
degrees.Set the Outer Radius [m] to
0.002
m.Set the Total Flow Rate [Kg/s] to
0.003815
Kg/s
In the
tabEnable Discrete Random Walk Model and Random Eddy Lifetime.
Click Set Injection Properties panel.
to close theClick Injections panel.
to close theClick Discrete Phase Model panel.
to close the
In this step, you will examine the default settings for the droplet material. This tutorial uses droplet properties copied from theFluent Database. In general, you can modify these or create your own droplet properties for your specific problem as necessary .
Confirm the properties for the mixture materials.
Setup → Materials → Droplet Particle → kerosene-liquid
Edit...
Retain the droplet particle properties. In this case, the default properties settings are used so no changes are needed.
Close the Create/Edit Materials dialog box.
Set the operating pressure.
Setup →
Boundary Conditions → Operating Conditions...
The Operating Conditions dialog box can also be accessed from the Cell Zone Conditions task page.
Enter
1519875
Pa for Operating Pressure.Click Operating Conditions dialog box.
to close the
Set the boundary conditions for the air inlet.
Setup → Boundary Conditions → Inlet → inlet
Edit...
Enter
inlet
for Zone Name.Enter
0.1096181560833
kg/s for Mass Flow Rate.Select Normal to the Boundary from the Direction Specification Method drop-down list.
Select Intensity and Viscosity Ratio from the Specification Method drop-down list in the Turbulence group box.
Enter
1
for Turbulent Intensity.
Enter
2
for Viscosity Ratio.Click the Thermal tab and retain the default value of
755.37222
for Temperature.
Click the DPM tab and select escape for the Discrete Phase BC Type.
Click Inlet dialog box.
and close the
Setup the perforated walls to model the liner effusion, by reading an input file. .
Setup →
Boundary Conditions → Perforated Walls...
Click
dialog box.Select the file named
input.txt
.Click
to check the model settings.The Number of injection Walls is set to
1
.The Injection Explicit Relaxation Factor is set to
0.1
.Click Injection Holes Geometry... button to view the detailed setup for Injection Holes.
Click Injection Holes dialog box.
to close theClick Dynamic Conditions... button to view the detailed setup for dynamic injection conditions for all the holes.
Click Dynamic Setup dialog box.
to close the
Click Perforated Walls dialog box.
to close the
First solve the cold flow through the combustor.
Solution → Solution → Methods...
Select Second Order for Pressure, Second Order Upwind for Density and First Order Upwind for the other equations in the Spatial Discretization group box.
Set the solution control parameters. This model combustor is relatively sensitive to the numerical settings, thus to be conservative, low pseudo time explicit relaxation factors are used. Set all the pseudo time explicit relaxation factors to be 0.1, except Body Forces (since there is no body force considered in this case) and Discrete Phase Sources (using the default value of 0.5 since a smaller value may not be able to recover the actual source item). With 0.1 as the relaxation factors, the case may need a greater number of iterations to converge.
Solution → Solution → Controls...
Enter
0.1
for all the Pseudo Time Explicit Relaxation Factors, except for Body Forces and Discrete Phase Sources.Set the reference pressure method in the TUI.
Press
Enter
in the console to get the command prompt (>
).Enter the text commands as shown in the box:
define operating-conditions reference-pressure-method 1
Ensure the plotting of residuals during the calculation.
Solution → Reports → Residuals...
Ensure that Plot is enabled in the Options group box.
Click Residual Monitors dialog box.
to close the
Initialize the field variables.
Solution → Initialization
Retain the default Hybrid initialization method and click to initialize the variables.
Save the case file (
combustor_effusion.cas.h5
).File → Write → Case...
Enter
combustor_effusion.cas.h5
for Case File.Ensure that Write Binary Files is enabled to produce a smaller, unformatted binary file.
Click Select File dialog box.
to close the
Run the calculation.
Solution → Run Calculation → Run Calculation...
Enter
300
for Number of Iterations.Click
.
Save the case and data files (
combustor_effusion.cas.h5
andcombustor_effusion.dat.h5
).File → Write → Case & Data...
Note: If you choose a file name that already exists in the current folder, Ansys Fluent will ask you to confirm that the previous file is to be overwritten.
Now model cooling flow with combustion.
Initialize the Progress Variable variable used for the ignition model.
Solution → Initialization
Click
to initialize the variables.Select Progress Variable from the Variable list.
Enter
1
for the Value.Select newgeom-combustor from the Zones to Patch list.
Click Patch and close the Patch dialog box..
Run the calculation.
Enter
400
for Number of Iterations.Click
.
Save the case and data files (
combustor_effusion.cas.h5
andcombustor_effusion.dat.h5
).File → Write → Case & Data...
Note: If you choose a file name that already exists in the current folder, Ansys Fluent will ask you to confirm that the previous file is to be overwritten.
Review the solution by examining graphical displays of the results.
Display effusion hole locations.
Results → Graphics → Contours → New...
Enter
contour-taggedface
for Contour Name.Ensure that Filled is enabled in the Options group box.
Select Smooth in the Coloring group box.
Select Perforated... and Tagged Face in the Contours of drop-down lists.
Select wall-liner and wall-heatsheild from the Surfaces lists.
Click Contours dialog box.
and close the
Display filled contours of wall temperature.
Results → Graphics → Contours → New...
Enter
contour-temp-wall
for Contour Name.Ensure that Filled is enabled in the Options group box.
Disable Global Range in the Options group box.
Select Smooth in the Coloring group box.
Select Temperature... and Static Temperature in the Contours of drop-down lists.
Select wall-liner and wall-heatsheild from the Surfaces lists.
Click Contours dialog box.
and close the
Create an iso-surface through the combustor geometry.
Results → Surface → Create → Iso-Surface...
Enter
mid-plane
for Name.Select Mesh... and Y-Coordinate from the Surface of Constant drop-down lists.
Click
.The Min and Max fields display the Y extents of the domain.
Enter
0
for the Iso-Values.Click Iso-Surface dialog box.
and close the
Display filled contours of temperature on a plane.
Results → Graphics → Contours → New...
Enter
contour-temp
for Contour Name.Ensure that Filled is enabled in the Options group box.
Select Smooth in the Coloring group box.
Select Temperature... and Static Temperature in the Contours of drop-down lists.
Select mid-plane from the Surfaces lists.
Click Contours dialog box.
and close the
Display filled contours of mean mixture fraction.
Results → Graphics → Contours → New...
Enter
contour-mf
for Contour Name.Ensure that Filled is enabled in the Options group box.
Select Smooth in the Coloring group box.
Select Pdf... and Mean Mixture Fraction in the Contours of drop-down lists.
Select mid-plane from the Surfaces lists.
Click Contours dialog box.
and close the
Save the case file (
combustor_effusion.cas.h5
).File → Write → Case...
In this tutorial you used Ansys Fluent to model the effusion cooling effects with perforated wall model in a 3D model combustor. Discrete injection type is used here for the effusion cooling injections. The procedures used here for simulation of effusion cooling can be applied to other combustors.