The default relationship is the generalized Navier’s law:
(7–1) |
where is the tangential velocity of the fluid,
is the tangential velocity of the wall, and
and
are material parameters.
is assumed to be zero, by default.
Note that full slip is obtained when . Equation 7–1
is either linear, with
, or of the full power law type with
.
For generalized Newtonian flow, the linear or nonlinear character of the flow
problem is not affected when the parameter . When
, a nonlinearity is introduced, which is comparable to that
generated by the power index of a power law or Bird-Carreau viscosity. In 2.5D and
in 3D, the
subscript stands for both tangential directions, as it would be
unphysical to allow different slip laws in different directions of the tangent
subspace.
Another relationship is the threshold law:
(7–2) |
where and
are two different slip coefficients, and
is the critical force density at which slip starts to occur.
The third relationship is the asymptotic law:
(7–3) |
where is a scaling factor with the dimensions of the velocity.
affects the slope of the slip-velocity curve.
A fourth relationship is a
generalized threshold slipping law that relates the tangential force to the tangential relative velocity
as follows:
(7–4) |
In this expression, is the tangential velocity under the application of a tangential
force
(
), while
is the tangential force below which there is no reported slipping.
For preventing a discontinuity in the expression, the velocity will be less than a
critical velocity
when the tangential force is less than
. Eventually b is the exponent which is larger
or equal to 1.
The reciprocal expression is considered in the implementation, and is written as follows:
(7–5) |
When the exponent b is set to 1,
Ansys Polyflow Classic identifies an affine relationship between and
, with a threshold whose amplitude is
. When the exponent b is larger than 1, the
tangential force
will increase less rapidly than the slipping velocity
. The expression has been made continuous in such a way that the
slipping velocity will be less than the critical velocity
when the tangential force is less than the threshold
. A very low, but non-vanishing value for
will lead to a slipping behaviour that mimics Equation 7–5. Typically, in an extrusion
process involving typical velocities of the order of 0.1 m/s,
can be of the order of
m/s.
The following figure illustrates how the expression mimics
the expected behaviour (black) for two different values of : 0.001 m/s (blue) and 0.003 m/s (green). The departure
occurs only for low velocities.
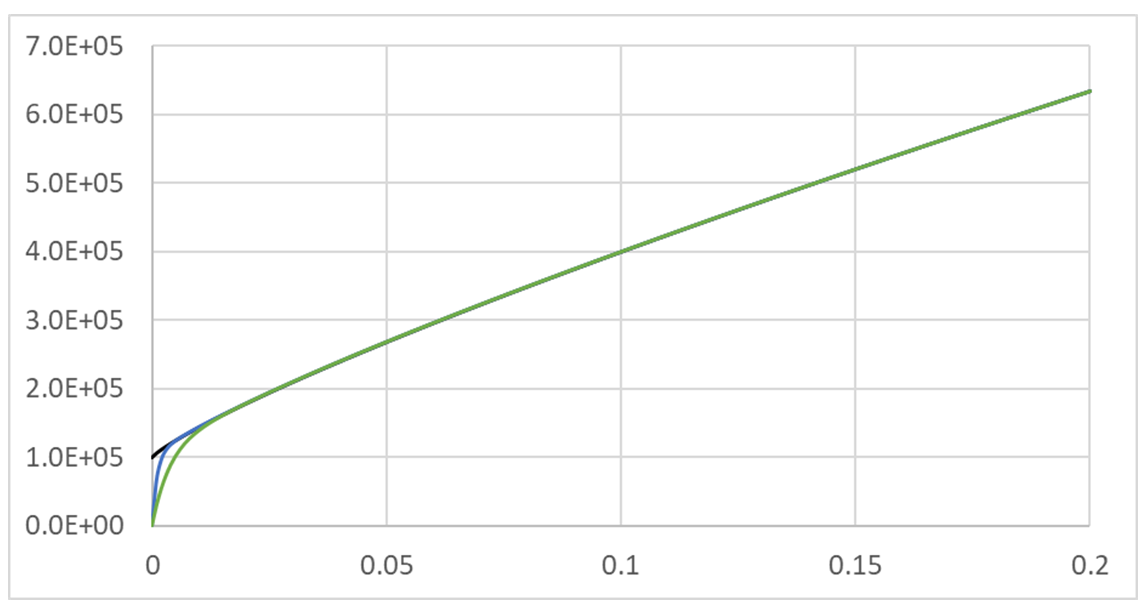
The four relationships describe the dependence of the
slipping with respect to the velocity, and involve important parameters referred to
as and
, or to
and
. In a general expression, these parameters can be made temperature
and/or pressure dependent. Note that temperature dependence is available only for
nonisothermal flows.
When it comes to temperature dependence, you can specify that the slipping coefficient is constant, obeys a first-order approximation of the Arrhenius law, or obeys the Arrhenius law, as shown in Equation 7–6, Equation 7–7, and Equation 7–8, respectively.
(7–6) |
(7–7) |
(7–8) |
In these expressions, denotes the temperature, while the other quantities have
definitions similar to those applicable for the temperature dependence of the
viscosity (see Arrhenius Law and Approximate Arrhenius Law).
When it comes to pressure dependence, you can specify that the slipping coefficient is constant, increases exponentially with the pressure, or increases linearly for positive pressure values, as shown in Equation 7–9, Equation 7–10, and Equation 7–11, respectively.
(7–9) |
(7–10) |
(7–11) |
In the previous equations, is the actual force density applied in the direction perpendicular
to the wall,
is a (usually positive) coefficient that is typically on the order
of 10-8 Pa-1, and
is a coefficient ranging from 0 to 1. Note that if Equation 7–11 is used in combination with the asymptotic
law (Equation 7–3), the slipping law will be quite
similar to the Coulomb law if
and
is small enough.