While there are many problems which can be calculated using only a hydrodynamic equation of state, there are many applications where material strength effects (i.e. its resistance to shearing forces) cannot be ignored and indeed may even dominate.
If the material is a solid and has finite shear strength then in addition to the calculation of the hydrostatic pressure it is necessary to define relations between shear stress and strain.
We also require relations to define the transition between elastic and plastic strain, both in compression and release, and a relation to define the onset of fracture.
The yield criterion governing the transition from elastic to plastic behavior may involve only a constant yield strength, or this strength may itself be a function of the degree of strain (work hardening), the rate of strain and/or the temperature of the material (energy dependency).
Even in hypervelocity impact problems, where traditionally strength effects could be ignored because of the extremely high stress levels produced, there exist two regimes - far field and late times - where strength effects may be important.
As the impact-created stress levels decay away from the area of impact there may be regions in the target where the local levels become of the order or less than the material strength. If this should be the case the diverging wave would separate out into a two-wave structure, an elastic wave followed by a plastic deforming wave, with consequent differences in material response.
As the projectile is slowed within the target the impact-produced stresses will also decrease and if the target is sufficiently thick a later point in time may be reached when material strength effects cannot be ignored.
It is clear that, unless you can be certain from the outset that material strength effects are not important (because the materials of interest are gases, fluids with no shear strength, or the stress levels in the system under study will always be so high that the strength of the materials could only produce a minor perturbation and may be discounted), the problem should be calculated as one with materials of finite shear strength in order to obtain a realistic solution.
The methodology followed in Autodyn is that first formulated by Wilkins (Wilkins, 1964 [11]) to extend conventional numerical hydrodynamic codes to include the effects of material strength and resistance to shear distortion.
The technique adopted was to work with the stress deviators which are the differences between the total stress and a uniform hydrostatic pressure.
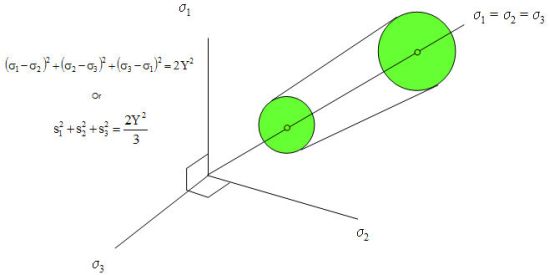
This model uses the original von-Mises premise that the yield stress has a constant value. Consequently, the von-Mises cylinder has a fixed radius. States lying inside the cylinder are elastic. States on the surface of the cylinder are plastic.
This model does not generally take into account the effect of strain hardening, strain rate sensitivity or thermal softening. However, these effects can be included to some extent by specifying, for example, an average dynamic value for the yield stress. A dynamic enhancement factor of 2 was used very successfully by Wilkins for simulating cylinder tests.
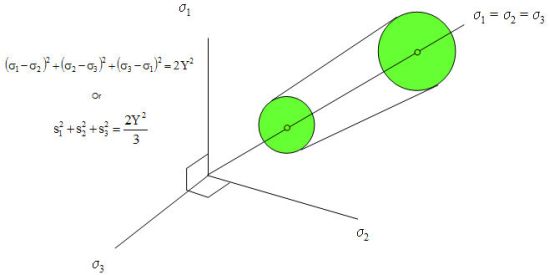
This model is a modification to the Johnson-Cook model, where the dependence on effective plastic strain represented by the term (A + Bεpn) is replaced by a piecewise linear function of yield stress Y versus effective plastic strain εp.
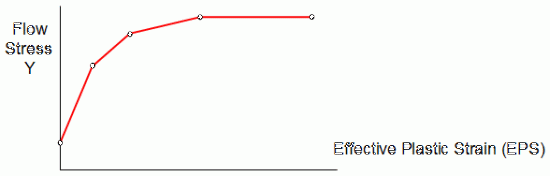
The strain rate dependence and thermal softening terms remain the same as in the Johnson-Cook model.
The beam resistance strength model lets you define the load-deflection, curvature-moment relationship for beam elements explicitly via input curves. The material data for the beam-resistance model is defined using four 10 point piecewise linear curves.
Axial Force vs. Axial Strain along axis 11 Moment vs. Curvature about axis 11 Moment vs. Curvature about axis 22 Moment vs. Curvature about axis 33 |
![]() |
There is no coupling between the different modes of deformation.
The model allows load-deflection data obtained from experiments on structural beams to be fed directly into the software.
The model was developed to allow representation of the global response of reinforced concrete beams/columns subjected to extreme dynamic loading.