In Robust Design Optimization (RDO) a CAE model is optimized under consideration of robustness criteria. In optiSLang an iterative variance-based RDO procedure is available. In this procedure deterministic optimization is utilized by considering safety factors within the constraint conditions. These safety factors should be chosen in that way, that the robustness requirements are fulfilled.
Figure 4.8: Statistical Properties of the Oscillator Responses and Input Sensitivities Obtained with Variance-Based Robustness Analysis
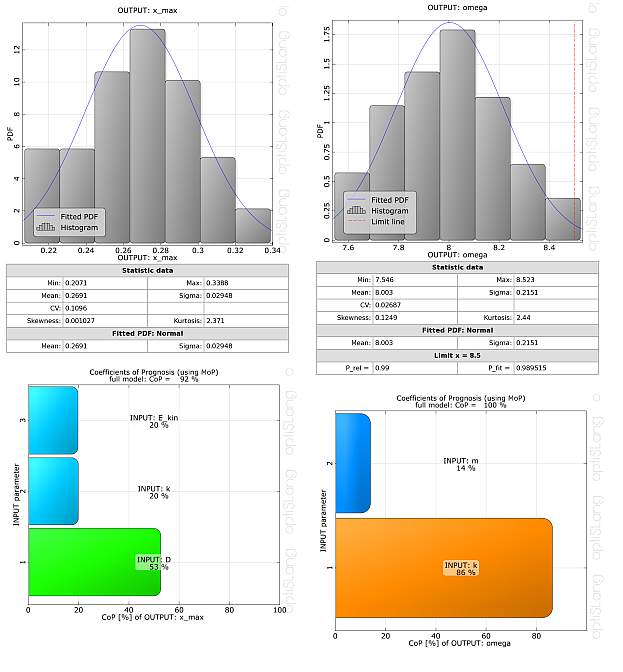
Generally the safety factors are not known a priori. In this case the user specifies a suitable initial guess and the initial deterministic optimization is performed. Additionally the robustness criteria are evaluated at the optimal design found by the optimizers. If the robustness requirements are not fulfilled, the optimization constraints are adjusted in a next step and the deterministic optimization procedure and the corresponding robustness analysis are performed again. This procedure is repeated until the robustness requirements are fulfilled. In Figure 4.9: Flowchart of Iterative Variance-Based Robustness Design Optimization with optiSLang, the flowchart of the iterative RDO procedure is shown.
The iterative RDO procedure is illustrated by means of the oscillator example. Within the initial robustness analysis discussed in Variance-Based Robustness Analysis a safety margin of 2.3σ has been reached. In a next step the optimization constraint is adapted as
(4–11) |
which leads to the optimal design shown in Figure 4.10: Iterative Robust Design Optimization. By means of the second robustness analysis using 100 samples the required safety margin of 4.5σ was proven. In case, that two iteration steps are not sufficient, in the third and following steps the constraints values can be linearly interpolated between the values of the previous steps by considering the obtained and the required safety margins. Generally, this procedure ends with an acceptably design within three or four iteration steps. If small failure probabilities are required, the estimate using the safety margin may be very inaccurate. In such a case, a final reliability analysis shall be performed to prove the required probability.
Optimization (ARSM) | Robustness Analysis (100 LHS) | |||||||
Constraint | m | k | ω | |X|max | Mean ω | Sigma ω | Safety Margin | |
Step1 | ω≤ 8.0 | 0.78 | 50.0 | 7.99 | 0.250 | 8.00 | 0.21 | 2.33σ |
Step2 | ω ≤ 7.6 | 0.87 | 49.7 | 7.55 | 0.269 | 7.54 | 0.20 | 4.75σ |
Iterative Robust Design Optimization of the damped oscillator using 2 steps to obtain 4.5σ safety margin.