Following are the equivalent stress and equivalent total strain plots from the inflation analysis on the 2D axisymmetric tire model:
With solid-shape display enabled (/ESHAPE,1), the following plot shows the equivalent stress on the 2D reinforcing elements (in the belt and body-ply regions) after the rim-mounting and inflation analyses on the 2D axisymmetric model:
As expected, the maximum equivalent stress is observed in the belts region.
Following is the equivalent stress plot on the reinforcing elements of the extruded 3D tire model (EEXTRUDE) after the mapping operation (MAP2DTO3D):
Following are the equivalent stress and total mechanical equivalent strain plots on the extruded 3D tire model after mapping:
As expected, the results closely match those of the corresponding 2D model.
Following is the contact-pressure distribution for the road-tire contact pair after the footprint analysis:
With the tire in a braking condition, following is the velocity vector sum plot (VSUM) after the first steady-state rolling analysis:
For the road-tire contact pair, most of the contact patch is in a sliding state:
In the free-rolling analysis with 0° camber, the variation of longitudinal reaction force (Fz) at the pilot node of the tire-rim contact pair is as follows:
Two steady-state rolling analyses follow the footprint analysis:
A steady-state rolling analysis is first performed with ω1= 50 rad/s and Vz = 20 m/s.
In the next steady-state rolling analysis, Vz is constant at 20 m/s while the rotational velocity is increased to ω2 = 70 rad/s.
Fz changes from positive to negative values during the second steady-state rolling analysis, meaning that the tire’s rolling state is transitioning from a braking state to traction state. Free-rolling occurs when Fz = 0.
Following are results plots for the road-tire contact pair at the free-rolling state:
Following the cornering analysis, the velocity plot in the lateral direction (Vy) is:
Figure 57.40: Velocity in the Lateral Direction (Vy) Following Cornering Analysis (Slip = 10°, Camber = 0°)
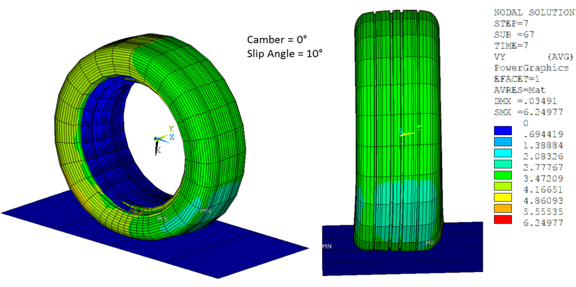
Following is the results plot for the road-tire contact pair after the cornering analysis:
At various camber angles, the cornering-force (Fy) variation with respect to the slip angle shows that the corning force is proportional to the slip angle at low slip angles: