This summary describes the work carried out by the Ernst-Mach-Institute (EMI), Century Dynamics Ltd (CDL) and TNO Prins Maurits Laboratorium (TNO) under ESA research contract No. 12400/97/NL/PA(SC) [1]. The aim of this project, termed AMMHIS, was to develop and define advanced material models and data for Nextel and Kevlar/Epoxy under hypervelocity impact conditions. The AMMHIS project was particularly concerned with the materials for the spacecraft shielding configuration used to protect the European Columbus module of the ISS. Due to the experimentally observed behavior of Nextel and Kevlar-epoxy, a new orthotropic hydrocode model was developed. This was necessary because pressure inside these materials depends on deviatoric strain components as well as volumetric strain. Nonlinear effects, such as shock effects, can be incorporated through the volumetric straining in the material. The developed model includes orthotropic material stiffness and a nonlinear equation of state and is described in Equations of State.
The hypervelocity impact of aluminum projectiles up to 15mm in diameter and normal velocities in the range of 3 km/s to 15 km/s were considered. The quality of the model has been demonstrated by comparison of simulations with tests to characterize the involved materials as well as with impact tests on the complete shielding configuration.
The developed material model is able to predict the main aspects of the shielding material response. Calculated shielding damage in the first bumper and in the Nextel and Kevlar-epoxy layers correlates well with experimental results. In terms of the back wall damage; for the 3km/s impact the simulation predicts a small hole that was not observed in the experiment, for the 6km/s impact the predicted back wall damage is consistent with the experimental observations (Figure 7.2: Alenia/EMI Test A8611 – Material Status During Impact on Reference Shielding, 15mm Diameter Projectile, 6.5km/s and Figure 7.3: Alenia/EMI Test A8611- Key Features of Material Response During Impact on Reference Shielding, 15mm Diameter Projectile, 6.5km/s). The simulation sensitivity studies carried out at both these velocities suggest that these are marginal cases in terms of back wall penetration.
Figure 7.2: Alenia/EMI Test A8611 – Material Status During Impact on Reference Shielding, 15mm Diameter Projectile, 6.5km/s
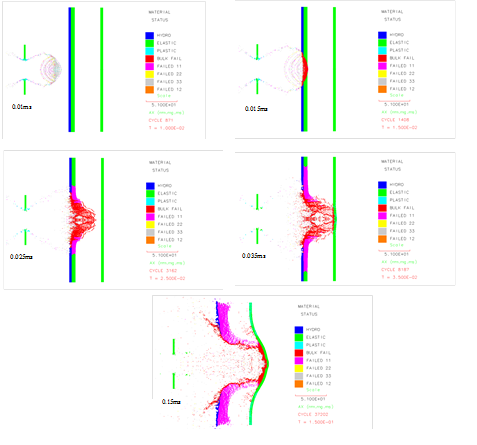
Figure 7.3: Alenia/EMI Test A8611- Key Features of Material Response During Impact on Reference Shielding, 15mm Diameter Projectile, 6.5km/s
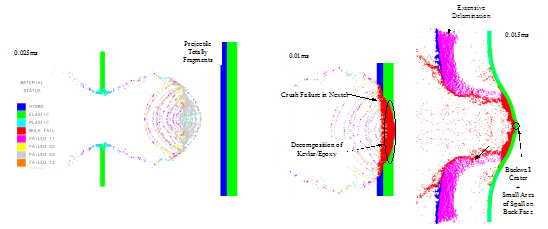