The simulation of a short fiber reinforced composite requires the mechanical and thermal properties of the constituent materials, that is, the polymer and fibers. The structural analysis requires the properties of elasticity and possibly the secant coefficients of thermal expansion- in cases where thermal loads will be applied. For the thermal analysis, the thermal conductivity is required.
You will find the following popular materials provided as samples in the Composite Materials library within Engineering Data:
Carbon Fiber (230 GPa)
Carbon Fiber (290 GPa)
Carbon Fiber (395 GPa)
E-Glass
Resin Epoxy
Resin Polyester
Resin Polyamide/Nylon 66
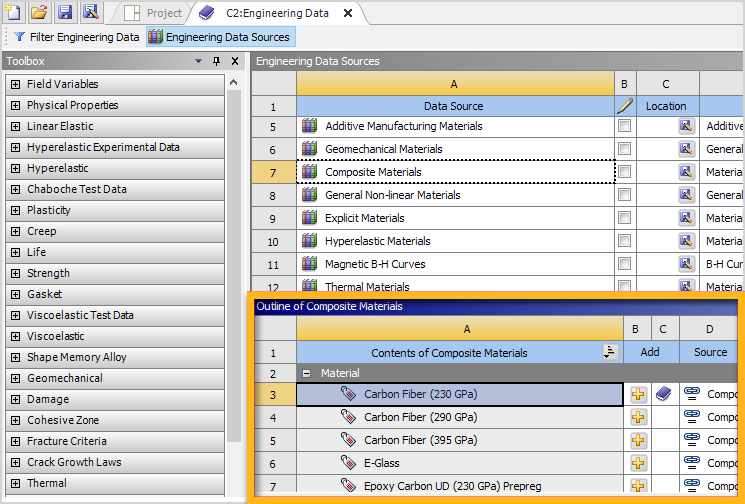
You can access additional materials typically used through the Ansys GRANTA Selector and import them into Engineering Data. For instance, the Material Universe library already offers a wide range of thermoplastics as well as several fiber types, such as glass, ceramic, metal, and others.
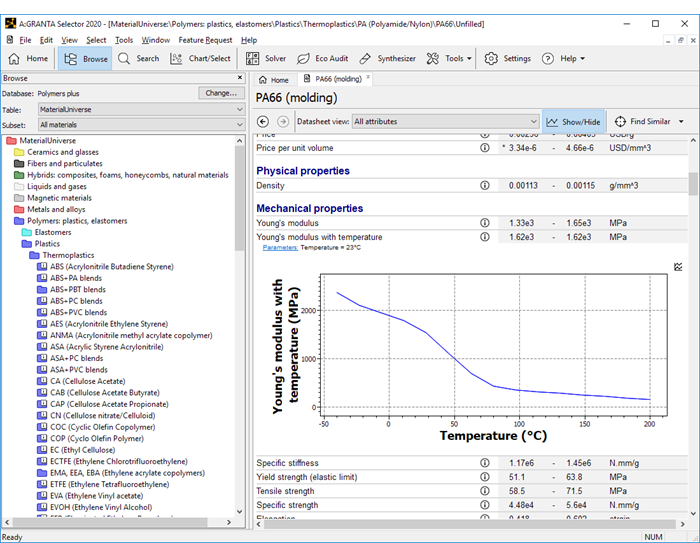
Use the following procedure to create a Short Fiber Composite Model in Material Designer and assign constituent materials:
In Ansys Workbench, drag a Material Designer Component System to the Project Schematic, define the constituents' material data in the Engineering Data cell, and then launch Material Designer.
Select a Short Fiber Composite Model, either an Analytical or an RVE Model (see Homogenization of Linear Elastic and Thermal Properties for more details).
Click Constituent Materials in the Ribbon Bar and assign the Matrix and Fiber materials.
If you chose an Analytical Model, specify details about the micro-structure (such as the Fiber Weight Fraction and the Aspect Ratio) in the Setup tool. Or, if you chose an RVE Model, define the composite microstructure in the Geometry tool.