Internal FEM Acoustics workflow creates acoustic domain for internal cavity acoustic wave propagation and transmission. The workflow contains steps to close the openings (holes) on the external surface and create a watertight acoustic cavity. Internal FEM Acoustics workflow meshes the surface cavity with triangular elements followed by volumetric meshing adjacent to the surface of the cavity. You can generate hybrid mesh using hexcore for volumetric meshing. This helps to reduce the total mesh count if needed.
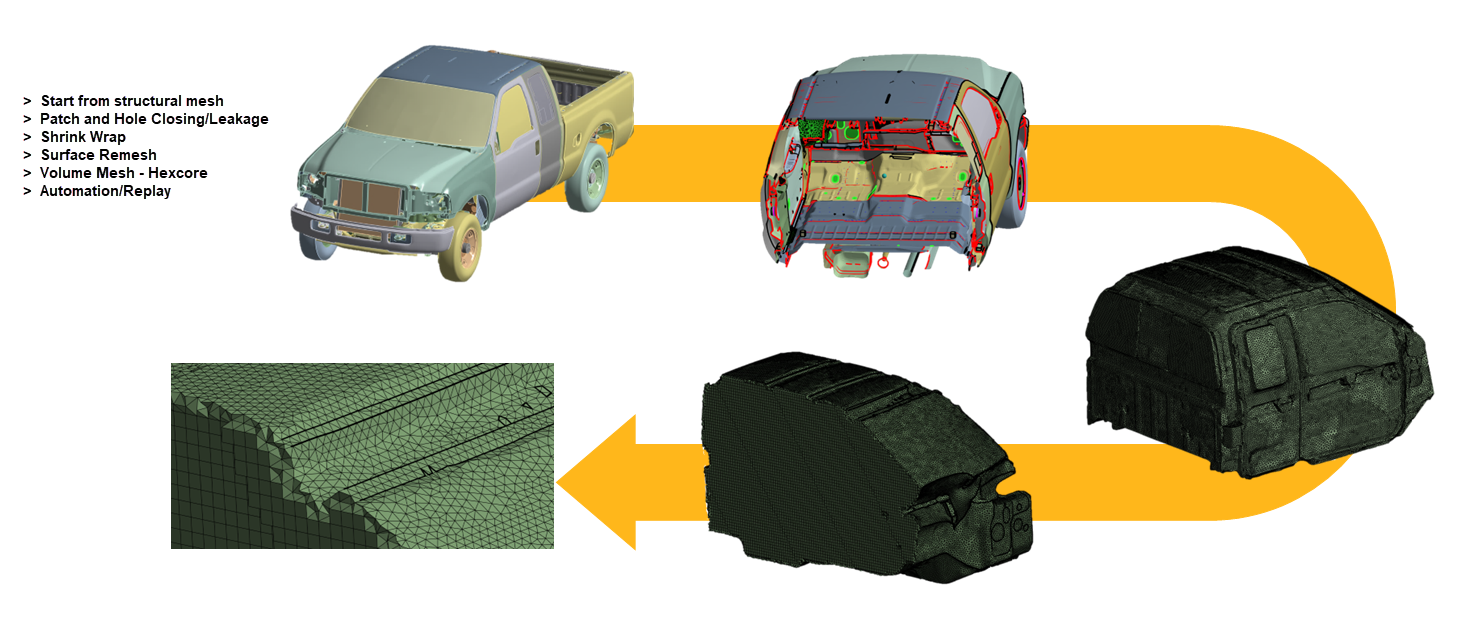
Note: Internal FEM Acoustics recommends a minimum of 12 elements per wavelength for FEM mesh having linear elements and a minimum 6 elements per wavelength of sonic speed of medium for quadratic elements.
When you select Mesh Workflows as Internal FEM Acoustics, Mesh Workflow loads a predefined template with Steps and Outcomes. Mesh Workflow performs these Steps through Controls and Outcomes to achieve the desired mesh for the Internal FEM Acoustics.
Internal FEM Acoustics workflow has the following steps:
Fill Holes: Fill the holes defined in the Hole Filling step. The operation type available for Fill Holes is Fill Holes.
Wrap Parts: Wraps the selected parts. The operation type available for Wrap Parts is Wrap.
Improve Wrap Mesh: Improves the surface mesh. The operation type available for Improve Wrap Mesh is Mesh Surface.
Mesh Volume: Creates the volumetric mesh. The operation type available for Mesh Volume is Mesh Volume.
Improve Volume Mesh:Improves the volumetric mesh generated in the Mesh Volume step. The operation type available for Improve Volume Mesh is Improve Volume Mesh.
Create Acoustic Regions: Creates the topology from the mesh only model. The operation type available for Create Acoustic Regions is Create Topology.
Assign Physics Properties: Defines material properties and thickness on the scoped parts or zones. The operation type available for Assign Physics Properties is Manage Zone Properties.