VM-AM-MECH-001
VM-AM-MECH-001
Additive Manufacture of Five-Post Beam Using Inconel 718
Overview
Reference: | Model and experimental results from America Makes, Project #4026, March 2017 | |
Material: | Inconel 718 | |
Supports Included: | No | |
Solver(s): | Additive in Mechanical | Additive Print |
Physics/Modes: | Linked Transient Thermal - Static Structural | Assumed Strain |
Platform: | Windows only |
Test Case
Perform a simulation of a Laser Powder Bed Fusion (L-PBF) additive manufacturing process of a beam with five posts printed with Inconel 718 nickel chromium alloy.
Find the distortion in the X direction along an edge of the part and compare results to measurements taken of the built part.
Analysis Assumptions and Modeling Notes
Additive in Mechanical
The simulation includes a build step and a cooldown step. Heat is applied at a constant temperature (80°C) to the underside of the base plate during the build step. Room-temperature convection is applied to that same surface during the cooldown step. Throughout the simulation the base plate is anchored by a fixed boundary condition on the underside of the plate. Ansys predefined material properties are used for Inconel 718 from the Additive Manufacturing Materials library. Deflection results from the vertical centerline of an end post are verified by comparing to experimental data. The analysis is performed using a Cartesian mesh.
Build Settings | Build Conditions | Cooldown Conditions |
---|---|---|
Deposition/Powder Layer Thickness = 0.03 mm | Preheat Temperature = 80°C | Room Temperature = 22°C |
Hatch Spacing = 0.1 mm | Gas Temperature = 80°C | Gas Temperature = 22°C |
Scan Speed = 1000 mm/sec | Powder Temperature = 80°C | Powder Temperature = 22°C |
Dwell Time = 10 sec | Gas Convection Coeff = 0.00001 W/mm2°C | Gas Convection Coeff = 0.00001 W/mm2°C |
Dwell Time Multiple = 1 | Powder Convection Coeff = 0.00001 W/mm2°C | Powder Convection Coeff = 0.00001 W/mm2°C |
Number of heat sources = 1 | Powder Property Factor = 0.01 | Powder Property factor = 0.01 |
Mesh and Material Settings |
---|
Element size = 0.1 mm Cartesian mesh |
Stretch factor in x = 2 |
Stretch factor in y = 2 |
Projection Factor = 0.8 |
Additive Print
The Assumed Strain simulation uses linear elastic material behavior.
Mesh and Material Settings |
---|
Voxel size = 0.1 mm |
Strain Scaling Factor = 2.079 |
Yield Strength = 726 MPa |
Elastic Modulus = 161 GPa |
Results Comparison
The distortion in the X direction as calculated by both solvers confirms the measured results which show that the joining of the posts causes significant distortion toward the center of the model.
Additive in Mechanical
Results | Target | Mechanical | Error (%) |
---|---|---|---|
X Deformation at Z = 5.5 mm | 0.359 | 0.34713 | -3.3064 |
X Deformation Maximum | 0.694 | 0.68183 | -1.7540 |
Figure 181: Comparison of Predicted X Deflection Along Edge to Measured Data - Additive in Mechanical
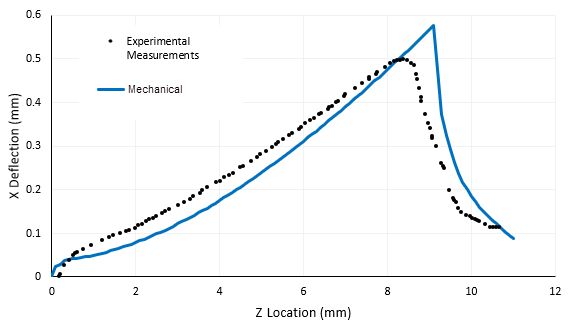