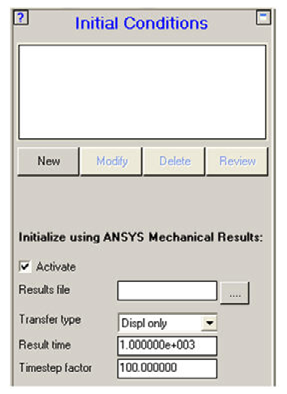
This panel lets you create Initial Condition Sets that can be used in Fill operations for Parts.
You do not have to use an Initial Condition Set to fill a Part, but there is a major advantage in using one.
Any subsequent changes you make to an Initial Condition Set are automatically applied to the Parts that have been filled using that Initial Condition Set.
This means you do not have to refill the Parts (this is currently not true for Euler Parts).
- Initial Condition Set List
The box at the top of this panel lists the Initial Condition Sets you have currently defined for your model. You can select an Initial Condition Set in this list.
- New
Define a new Initial Condition Set.
- Modify
Modify the selected Initial Condition Set.
- Delete
Delete one or more Initial Condition Sets from your model.
- Review
Review the parameters for the selected Initial Condition Set in a browser window.
- Implicit-Explicit Model Initialization
- Activate
Initialize an Autodyn analysis model using the results of an Ansys Mechanical implicit analysis.
- Results File
The Ansys .rst results file to be used to initialize the Autodyn analyses.
- Transfer Type
The initialization method; either the Displacement Only or the Material State option as described below.
- Results Time
The result time from the Ansys Mechanical implicit analysis at which to extract results from the .rst file.
- Timestep factor
(Note that this option is applicable only for the Displacement Only method.) The initial timestep from the Autodyn solution is multiplied by the timestep factor. The resulting time (PVELTM) is used together with the nodal displacements from the Ansys Mechanical analysis to calculate constant nodal velocities. These nodal velocities are applied to the Autodyn model over PVELTM in order to initialize the Autodyn nodes to the correct positions.