Understanding the Effects of Curvature and Proximity Settings
If neither Curvature or Proximity is activated, the mesher ignores the aspects of surface curvature and local proximity. In general, a uniform mesh should be generated in such cases, however, in some cases the mesher may use biasing in order to match edges meeting at a common vertex. This matching is done to avoid high aspect ratio elements.
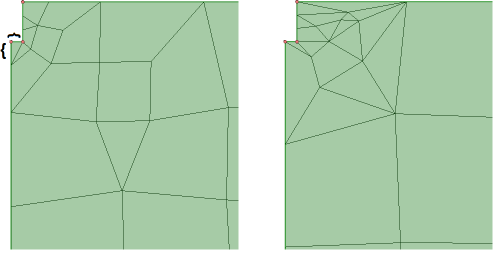
If you want the mesher to better respect curvature or proximity, these options can be activated and work as follows:
Curvature: Surface curvature is computed by finding the angle between normals of adjacent elements. The mesher reduces the mesh size in the areas of curvature to the Minimum size when possible. Situations that may prevent the mesher from capturing the curvature include the following:
The Normal angle will limit refinement. Thus, once the mesh has been refined such that all angles between normals for adjacent mesh elements is smaller than the defined angle, the refinement will stop even if the Minimum size has not been reached.
Mapped mesh takes priority over curvature-based refinement. That is, if the software can either get a mapped (swept) mesh or a refined mesh capturing curvature, then mapped meshing will take priority. This could lead to the mesh being refined in one direction of a mapped face but not in both directions.
Proximity: Proximity of thin regions is computed. The mesher tries to enforce the defined number of Cells across gaps when possible. Situations that may prevent the mesher from capturing the proximity include the following:
The Minimum size will limit refinement. For example, if a 1 mm gap is found and you have set Cells across gaps to 3 and Minimum size to 0.5, then you should only expect 2 cells in the gap. In this situation, the recommendation would be to set Minimum size to something slightly smaller than 0.5 (such as 0.49) just to be safe.
Mapped mesh takes priority over proximity-based refinement. That is, if the software can either get a mapped (swept) mesh or a refined mesh capturing proximity, then mapped meshing will take priority.