The Gap Size constraint prevents the formation of closely spaced features in the optimized shape. The appearance of such features is more pronounced when the maximum member size constraint is used, since the algorithm may satisfy the maximum member size constraint by placing small holes to reduce the size of large features. It is only available for the level-set based optimization method and can only be activated in conjunction with the Maximum member size property.
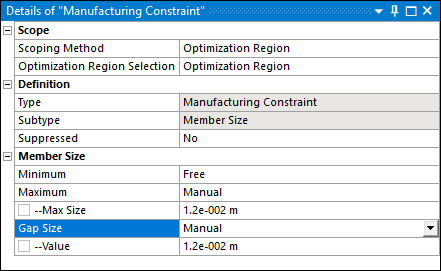
Industry Motivation
This specification is motivated by several industrial manufacturing processes:
During casting process, it is linked to the capability of constructing molds with thin features as well as with their life cycle.
During milling process, as well as other tooling processes, it is related to the characteristics of the tooling machine (head and bit radius, etc.).
Gap Size Definition
Theoretically, the computation of the gap size is performed in two steps:
The pointwise distance between structural members is computed for every point on the boundary along the exterior normal vector.
The minimum value of the distance field is defined as the gap size of the structure.
However, this formulation presents two main drawbacks:
It is not derivable, due to the minimum operator and the computational procedure, therefore, it is not suitable for gradient-based optimization algorithms.
It is quite restrictive for topology optimization since it hinders structural members from approaching each other and finally merging.
A specific formulation has been devised to overcome these problems. As a consequence of adopting a rather qualitative formulation [14], closely spaced features may still appear in the optimized shape.
Setup and Technical Specifications
The setup only requires specifying the lower limit not to violate, denoted
, in terms of length units. However, for the sake of accuracy
in the calculation of the member size,
, must respect a certain ratio with respect to
, as shown below.
Level Set Based | |
---|---|
Both relations are motivated for accuracy reasons. However:
|
Recommendations
As any constraint, the Gap Size affects the objective
performance. Namely, by increasing , the feasible domain shrinks and probably leads to smaller
objective gain.
Example
For the following example, the Optimization Type property is set to the option. This analysis uses a pillar structure clamped on the bottom with a vertical load applied to the top, as illustrated below. The optimization problem is to minimize the structural compliance under a volume fraction constraint of 0.4.
![]()
|
![]()
|
Here is the finite element mesh (144,828 elements).
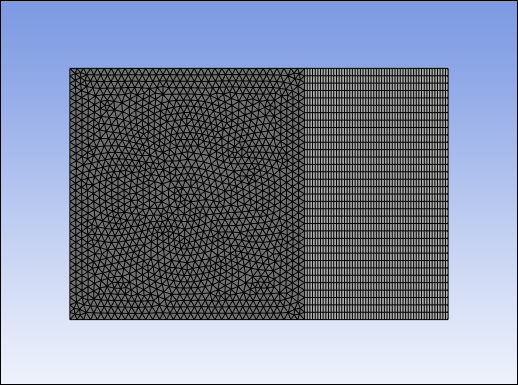
As shown from the Topology Density result as well as a User Defined Result, the optimized result without considering manufacturing constraints. As expected, the optimized shape is a cylinder. Note that the User Defined Result shown below is a cutout of the result using the Section Plane feature.
![]()
|
![]()
|
Adding an maximum member size constraint of 0.012 leads to the optimized shape shown below. One can observe the indentations that are created to satisfy the maximum member size constraint. The structural compliance is equal to 1.85953 e-04 (+1.5%).
![]()
|
![]()
|
Adding a Gap Size constraint with limit dGapSize = 0.012 results in the optimized shape shown below, wherein the distance between structural members increases. The structural compliance equals to 1.92452 e-04, namely 5% less stiff due to the maximum member size and gap size constraints.
![]()
|
![]()
|