Following are the equivalent stress and total mechanical equivalent strain plots following the 2D axisymmetric analysis:
The following figures show the equivalent stress and total mechanical equivalent strain plots on the extruded 3D model after mapping (MAP2DTO3D,SOLVE):
As expected, the results closely match those of the corresponding 2D model. Results may differ, however, if contact settings are not equivalent in the 2D and extruded 3D models. In such cases, experiment with the contact settings to obtain matching results.
The following figures show the equivalent stress and total mechanical equivalent strain plots on the 3D model after solving for the bending load via the multiframe restart analysis:
The following figure shows the bending stress plot on threads after solving the 3D model with bending load:
This figure shows the contact pressure plot on the threaded region for the 3D model after mapping (MAP2DTO3D,SOLVE):
As expected, the contact pressure is uniform in the circumferential direction.
Following is the contact pressure plot on the threaded region at the end of the analysis:
Due to bending, the threaded connection bears most of the load at only one side.
This animation shows the change in contact pressure for the threaded connection during the entire analysis:
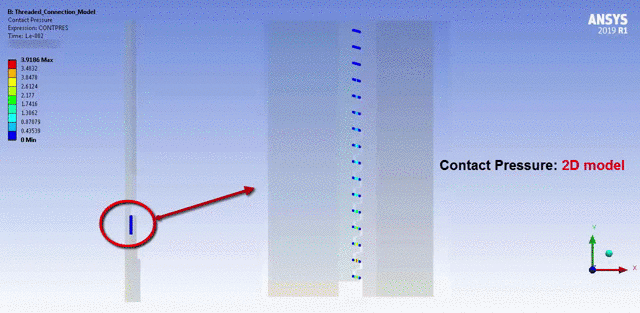
This animation shows the equivalent stress result during the full analysis, and the change in the threaded-connection status at the last load step (during bending):
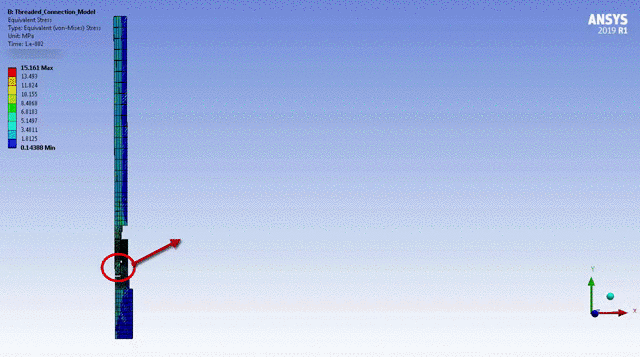