Within the Ansys Workbench application, there are two ways to analyze composite solid models: The analysis can be done in the Workbench Mechanical application, or it can be carried out in the Mechanical APDL software (Ansys Classic). While the functionality is identical, the user interface is very different. As an alternative, composite solid models can be exported from the ACP application for processing outside of Ansys.
Analysis with Mechanical Application
In the Mechanical application, the composite layered solid element model appears as a meshed body. Any other bodies in the ACP (Pre) component are not carried forward. You can define loads, boundary conditions, and connections to other parts in the Mechanical application as usual. An example of such a solid model workflow is shown below:
Analysis with Mechanical APDL Application
A further option is to link solid models to a Mechanical APDL application system where the boundary conditions and loads are defined. Typically, an APDL script is used to set boundary conditions and analysis settings for a workflow with the Mechanical APDL application. An example of a solid model workflow with the Mechanical APDL application is shown below:
Figure 4.9: Workbench Software Workflow for Composite Solid Modeling with Mechanical APDL Application
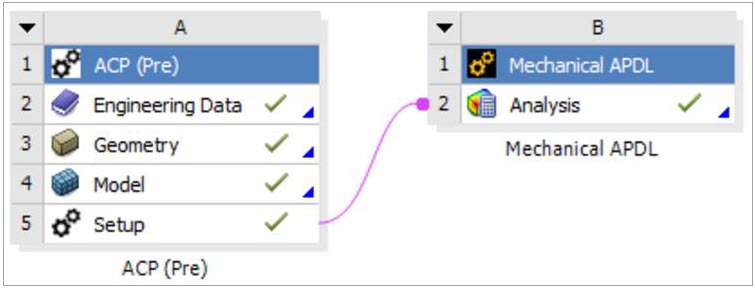
Adding an ACP (Pre) Component to the Project
The solid modeling workflow in Ansys enables the assembly of many preprocessing components into one analysis system. In some cases, it may be desirable to analyze thick-walled composites in isolation but often it is desirable to see the interaction between multiple bodies. The connection procedure is explained with the help of two examples for both analysis methods (Workbench Mechanical and Mechanical APDL applications).
Link with Workbench Mechanical Application
The procedure for building an analysis model is illustrated with a Static Structural Analysis system as an example. A composite doubly-curved tensile test specimen is held by two metallic grips at its two ends. Both the composite and the metallic parts are integrated into an assembly model.
A Project Schematic is shown below:
Figure 4.10: Analysis of a Composite Doubly-Curved Specimen and Metal Grips Modeled with Mechanical Application
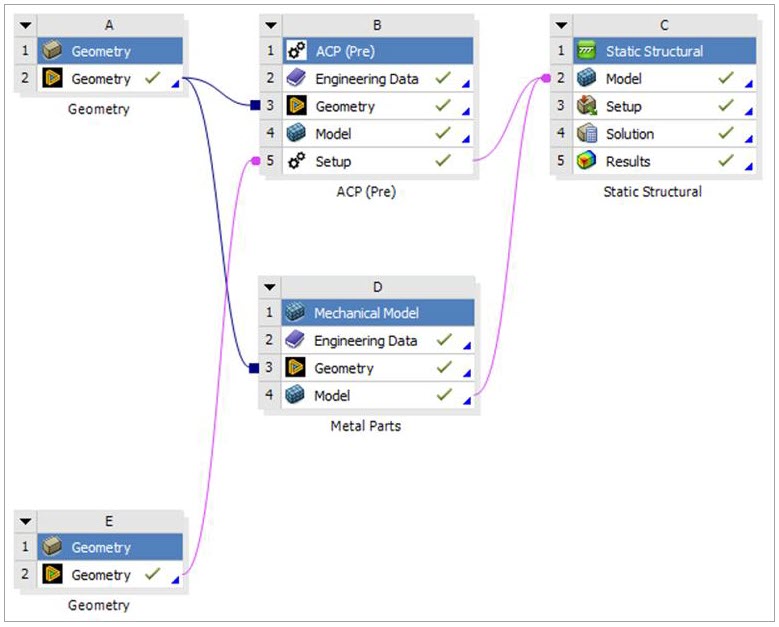
In this example, the geometry consists of one layered solid specimen and two metal grips. The link between ACP (Pre) (B5) and Static Structural (C2) only transfers the generated layered solid element model. The link between the Mechanical Model (D4) and Static Structural (C2) transfers all metallic parts. The connections, boundary conditions, and all other preprocessing definitions can be defined in Setup (C3) as usual. The global solution and postprocessing can be determined and analyzed in the Workbench Mechanical application.
Link with Mechanical APDL Application
Two composite components — a plate and a t-joint — serve as an example for the workflow procedure in the Mechanical APDL application. A Project Schematic is shown here:
The proper sequence of connecting the system always begins with connecting an ACP (Pre) component first. In this case, it is not important because both inputs are ACP (Pre) solid models.
In the Mechanical APDL component the boundary conditions, loads and all other preprocessing definitions can be defined through APDL macros. These macros can be linked with the Mechanical APDL cell which will be integrated in the automatic update functionality of Workbench. A macro file can be added to the component through the right-click context menu (see figure below). Add Input File... appends the APDL running sequence with an additional macro. Check the order of the files of the Mechanical APDL component. The macros should be listed after the Solid Model Process Setup file(s).
Multiple Parts (Adding Other Systems)
It is possible to add multiple components to one analysis system: two composite parts or a composite part connected to two isotropic parts, for example.