Composite materials are created by combining two or more layered materials, each with different properties. These materials have become a standard for products that are both light and strong. Composites provide enough flexibility so products with complex shapes, such as boat hulls and surfboards, can be easily manufactured.
Engineering layered composites involves complex definitions that include numerous layers, materials, thicknesses and orientations. The engineering challenge is to predict how well the finished product will perform under real-world working conditions. This involves considering stresses and deformations as well as a range of failure criteria. Ansys Composite PrepPost provides all the necessary functionalities for preprocessing layered composite structures, while Mechanical provides postprocessing capabilities for composite analyses.
ACP Workflows
Ansys Composite PrepPost (ACP) is an add-in to Ansys Workbench and is integrated with the standard analysis features. As a result, the entire workflow for a composite structure can be completed from design to final production information.
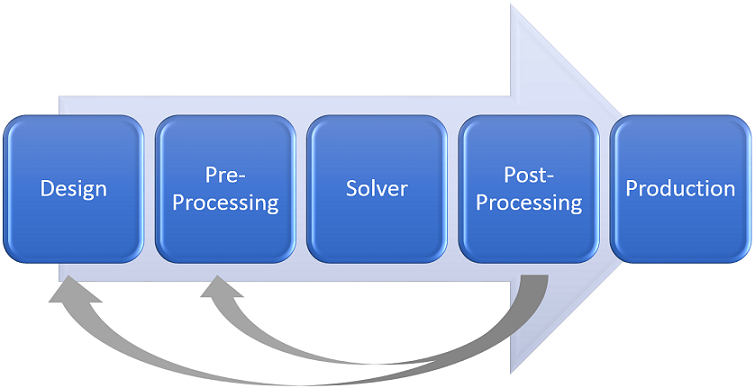
The geometry of the tooling surfaces of a composite structure is the basis for analysis and production. Based on this geometry and a FE mesh, the boundary conditions and composite definitions are applied to the structure in the preprocessing stage. After a completed solution, the post-processing is used to evaluate the performance of the design and laminate. In the case of an insufficient design or material failure, the geometry or laminate has to be modified and the evaluation is repeated.
ACP has only a preprocessing mode, in which all composite definitions can be created and mapped to the geometry (FE mesh). Then, these composite definitions are transferred to the FE model and the solver input file. After the composite analysis is completed and the result file(s) are imported, postprocessing results (failure, safety, strains, and stresses) can be evaluated and visualized in Mechanical.
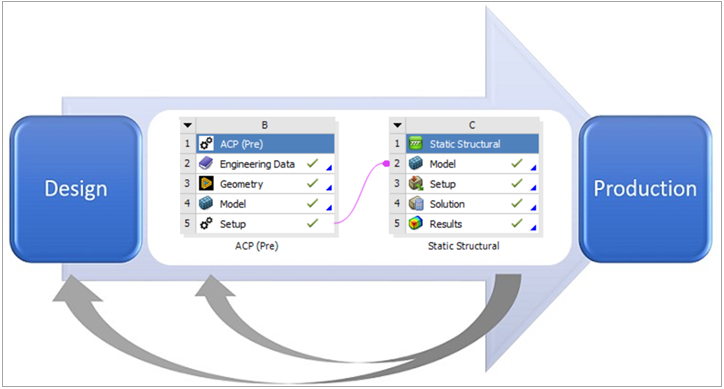