As engineers designing parts, we have long known that we need to adjust our CAD models to compensate for the anticipated distortion that occurs during manufacture. Distortion compensation capabilities in simulation software can be powerful tools to correct for these distortions. The process of creating a successful distortion-compensated geometry may be as simple as a single solve, or it may take multiple iterations of compensating and resolving to converge on the tolerance criteria. The determination of which approach to use depends on our application requirements. The Distortion Compensation Add-on in Ansys Mechanical provides two alternate approaches:
A single-run approach, in which a compensated geometry is created by reverse-distorting a single, static structural result set using a distortion compensation factor. This approach is very quick and may provide a satisfactory geometry in many cases.
An automated, iterative approach, in which simulations are run until a geometry is generated that, after manufacture, deforms to within tolerances of the original design. This approach usually involves longer overall run times than Single Compensation because of multiple iterations but results in an optimized geometry.
The example below uses the iterative compensation technique to illustrate the concept of distortion compensation. The image on the left shows a geometry that deformed out of tolerance during an LPBF process. The gray outline represents the starting geometry before simulation. The red dashed lines represent the allowable tolerances. The image on the right shows the same geometry after automatic, iterative distortion compensation. The gray outline now shows the final, compensated geometry that is required as the starting geometry to result in a geometry after processing that deforms within tolerances.
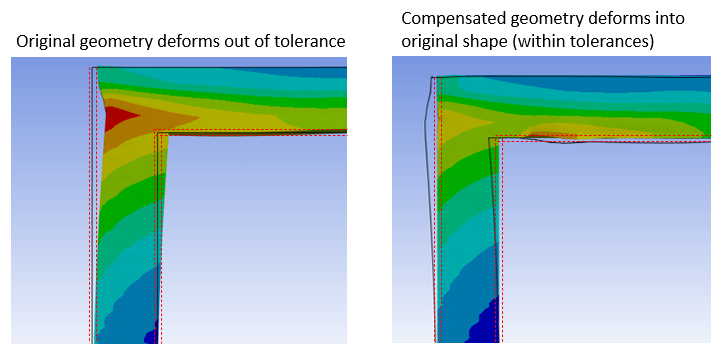