The Taper Edges option for Modeling Plies is suitable for defining individual taper angles for specific modeling ply. Its intended purpose is for use with a single tapered ply, such as a core, however it can be used for tapering multiple plies. If the Modeling Ply tapering option is used for multiple layers the taper angle is applied to each Modeling Ply and the vertical ply thickness distribution is superimposed. In such a case, the total taper angle of the lay-up is generally higher than the individual taper angles. The total taper angle scales non-linearly with the number of plies and their thicknesses. Furthermore, the taper size is a dependent on the size of the mesh. For this reason, care should be taken when using the Taper Edges option for multiple plies. When modeling a composite with a defined total taper angle a Selection Rule definition may be more suitable. The trailing edge of an airfoil blade is an example for such an application.
The example below shows the effects of superposing multiple modeling plies that have the same taper angle. The middle column shows a lay-up schematic while the right column displays the corresponding representation of a section cut in ACP. The superposition of two different ply thicknesses results in two taper angles of which one is steeper than the nominal angle.
Figure 3.18: Superposition of Modeling Plies with Identical Taper Angles. Schematic (Middle) and Section View Illustration (Right)
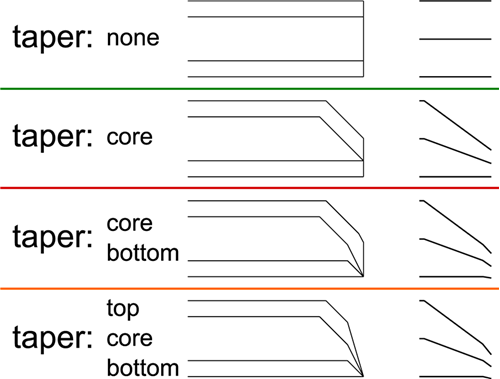